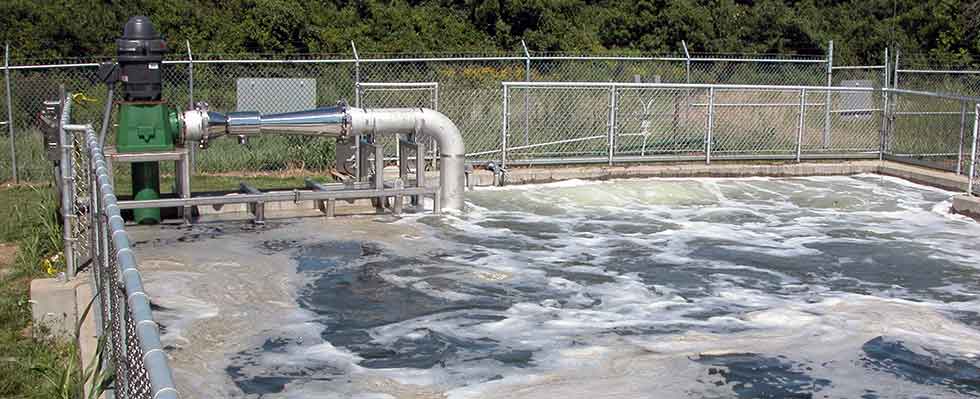
Industrial facilities are experiencing increased pressure from publicly owned water treatment works (POTWs) to pretreat their effluent—particularly to reduce the levels of biochemical oxygen demand (BOD) they discharge into public wastewater streams. Aeration plays major roles in the removal of BOD as well as the restoration of dissolved oxygen levels in discharge water, making it more important than ever.
Industrial water treatment aeration systems can run the gamut from small, simple skid systems to massive tanks stirred by huge motors. Though oxygen is relatively soluble in water, success in mixing and transfer can differ as widely as system designs do. This article explores two major approaches to industrial aeration: basin aeration and in-line aeration.
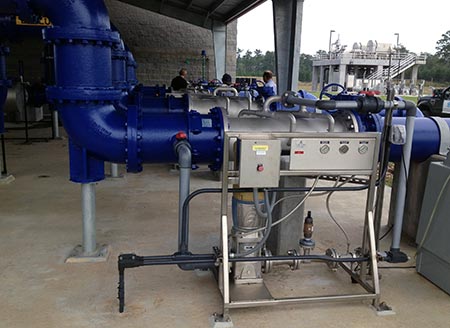
Basin Aeration
Basin aeration is widely used for effluent with high levels of solids, which is found in equalization tanks, sludge holding tanks or aerobic sludge digesters, to prevent solids from settling and for freshening, odor control and effluent homogenization.
In basins, every inch of depth counts because depth can replace surface area. Every square inch of surface area represents costly space in the facility’s footprint, along with all the infrastructure that goes with it. Increased depth can yield a decreased footprint for the basin, but it can create challenges for some aeration systems—particularly surface aerators or “splashers,” whose effects are concentrated at the topmost few feet of the basin. These high-maintenance splashers expend great amounts of energy to push air into the water, constantly fighting air bubbles’ natural tendency to float. In basins deeper than 7 or 8 feet, the layer that they can aerate with some success sits above a layer of poorly aerated or anoxic water. To make matters worse, the solubility of air in water is lower at the near-atmospheric pressures close to the surface, so splashers expend their energy in the least efficient mixing zone in the water profile.
Because oxygen transfer efficiency increases with pressure and depth, fine bubble diffusers are widely used for deeper basins, where the bottom-mounted diffusion stones emit air or oxygen that is largely absorbed into solution as it travels toward the surface.
Fine bubble diffuser systems are complex and precisely tuned, requiring careful maintenance. Gaskets and seals in the diffusers are prone to wear, breaks and blowouts—while membranes and diffusers are prone to fouling, especially where solids levels are high. If stones are damaged, leaks and coarse bubbles can reduce surface area and transfer efficiency. Shutdowns and regular basin drainage are also required to inspect and repair diffusers.
These challenges have driven many industrial wastewater managers to jet aeration systems, whose nozzles are easier to maintain and provide good transfer at the point of discharge.
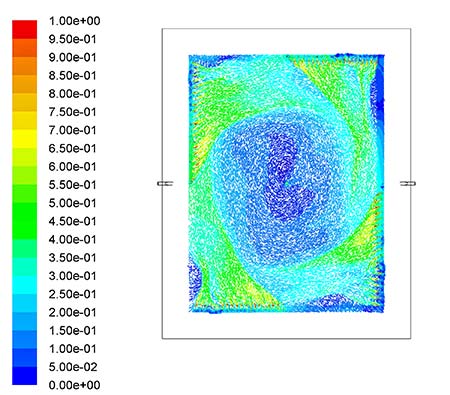
Venturi Injectors
The high-powered blowers that drive fine bubble diffusion or jet aeration systems require protection from the elements, more infrastructure in the form of roofs and even walls as well as periodic maintenance.
A lower-maintenance alternative is a Venturi injector system that uses a simple pump to push effluent through a manifold system that discharges into the bottom of the basin. The effluent flow passes through Venturi injectors where the velocity of the fluid increases and pressure decreases. The pressure drop creates a vacuum that draws in air or oxygen, shearing and mixing it with the liquid.
That mixing, driven solely by the flow’s energy, provides high gas transfer efficiency in the injector itself. Most of the remaining air is incorporated into the contents of the basin when it is emitted through high-shear mixing nozzles, precisely designed and placed to maximize circulation and mixing within all areas of the basin.
The Venturi system is efficient. It is driven by simple physics rather than by compressors and blowers—there are no moving parts to fix or replace, and no fouling-prone fine pores. As a result, injector systems have been used successfully in sludge digester and sludge holding systems with solids levels as high as 6 percent.
Computational fluid dynamics (CFD) can optimize aeration systems for the precise sizing, placement and orientation of injectors, pumps, pipes and nozzles. Guidance from CFD analysis has also allowed for the development of aeration systems with high turndown rates, allowing water treatment operators to adjust flow and energy consumption to meet system needs. The result can be high efficiency, both in terms of gas transfer and energy.
For instance, a Midwestern food processor replaced a set of 16 basin aerators—each with its own 25-horsepower (hp) motor—with a system of eight 40-hp pumps, submerged nozzles and Venturi injectors. The processor saw its wastewater processing energy costs drop 30 percent.
In-Line Aeration
Where the level of solids are lower, in-line aeration systems provide an efficient, compact aeration solution. Placed upstream of filtration systems to help precipitate metals like iron or manganese, prior to membrane bioreactors to enhance biological activity, or after filtration to re-oxygenate water prior to discharge, in-line aeration can dramatically enhance the treatment of effluent.
A wastewater treatment plant in Hancock County, Mississippi, installed a 2-inch sidestream Venturi injector system to meet dissolved oxygen standards for discharging treated effluent without breaking pressure in its pump line. The aerated sidestream is reintroduced to the main flow through a 6-inch by 24-inch pipeline flash reactor, which uses four precisely oriented mass transfer nozzles to achieve thorough mixing and transfer in just a few feet of pipe. The entire system fits on a skid, lending itself to the plug-and-play packaged treatment units that are gaining popularity in industrial and smaller municipal installations for their simplicity and small footprints.
In-line aeration systems—particularly those with high turndown capabilities that can respond to changing conditions or demands—can also be compatible with automated process control systems. In short, the simple physics of Venturi aeration systems can help industrial wastewater managers face complex chemical, logistical and economic challenges.