How this positive displacement technology improves energy efficiency and production rates.
Blackmer
12/12/2018
The need for more industrial operations to satisfy the demands of a constantly growing population can collide with edicts that manufacturers reduce their utility and overall operating costs while simultaneously operating in a more environmentally friendly manner. This has forced operators in the industrial sectors to reconsider the types of equipment they have been using in their facilities and operations, with an eye on upgrading to systems that can reliably provide both environmentally safe and cost-effective production.
A Positive Outlook
First, a bit of background. Positive displacement (PD) pumps were developed long before centrifugal pumps. Greek mathematician Archimedes is said to have invented the first screw pump around 225 B.C. The operation of PD pumps is signified by the displacement of a known quantity of liquid with each revolution of the pumping elements, which can include vanes, lobes, gears, rotors, screws, etc. The liquid is displaced through the spaces that are created between the PD pump’s specific pumping elements. After the liquid is collected in this space, the movement of the pumping elements transports it to the discharge port. In general, this method of operation allows PD pumps to handle liquids with viscosities up to 1,320,000 centistokes (cSt)/6,000,000 Saybolt Seconds Universal (SSU); capacities up to 1,150 cubic meters per hour (m3/hr) or 5,000 gallons per minute (gpm); and pressures up to 700 bar or 10,000 pounds per square inch (psi)..jpg)
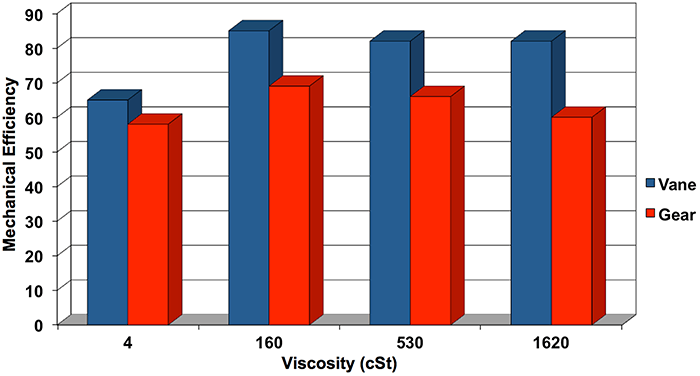
- PD pumps are inherently self-priming. Centrifugal pumps must be pre-primed. Industrial facilities can design their process around this by including pre-fill cycles, minimum tank levels or expensive below-grade installations. On the other hand, industrial facilities can reduce or eliminate these considerations by using a PD pump that is inherently self-priming. This capability allows the PD pump to draw a suction vacuum and compress air into the discharge piping, all while dry running. This enables the pump to be used in top-offload suction-lift installations or with long sections of suction pipe.
- PD pumps can line strip. Product recovery is critical for both safety and cost savings. PD pumps left on after a batch cycle can evacuate the suction and discharge piping, preventing product spillage when the pumps are maintained or when an operator disconnects a hose. This is a critical safety advantage. Further, PD pumps can extract costly products from the bottom of supply tanks (known as the liquid “heel”). The site may purchase an entire tanker, but a portion of the liquid may be left behind by centrifugal pumps, which creates the risk of product cross-contamination, as well as increased tank-cleaning costs. PD pumps can also recover liquid from within the piping system.
- PD pumps are insensitive to the system’s pressure fluctuations. Some operations feature a batch process, have high backpressure or struggle with operating near a centrifugal pump’s best efficiency point (BEP). PD pumps do not have a BEP and are immune to any system pressure fluctuations.
- PD pumps are viscosity flexible. There is no reduced performance at increasing viscosity (or decreasing viscosity for ultrathin multiphase liquids). PD pumps can operate continuously at 0.2 centipoise (cP) or 200,000 cP viscosities. In fact, many PD-style pumps can be used on a thin solvent and on thick crude oil, which makes them ideal for liquid-terminal or bulk-transfer applications.
- PD pumps operate at reduced speeds. This capability reduces the surface velocity of rotating seal faces and improves seal life. PD pumps often require less than 500 revolutions per minute (rpm), which yields slower sealing velocities, friction-heat buildup and the cooling-lubrication needs of the seal. The result is that seals are more robust, resulting in longer component life and reduced maintenance costs over the life of the pump.
- dry-priming capability that allows them to run dry for extended periods
- superior suction-lift capabilities
- ideal operation in low-flow, high-head applications
- low-pulsation, low-vibration pumping for shear-sensitive liquids
- suitability for use in metered-flow applications
- optional sealless construction for elimination of potential leak paths
- easy vane replacement
Sliding Vane vs. Gear Pumps
Rotary self-compensating sliding vane pump technology was developed in the early 1900s by an engineer who was looking for a solution to ill-performing gear pumps that were consistently wearing and losing volumetric efficiency, leading to product slip that hampered flow rates. At the time, gear pumps were far and away the most common type of PD pump used in industrial liquid-handling applications. There are two typical types of gear pumps: internal and external gear, both of which transport liquids through the action of a series of gears coming into and out of mesh. While the pumping action for both is comparable, external gear pumps use two similar rotating gears to mesh, whereas the internal gear pump uses a drive, or rotor, gear operating against a smaller internal, or idler, gear. Both modes of gear pumps possess some advantages that are similar to sliding vane pumps—nonpulsing, self-priming and dry-run capability; ability to handle thin liquids at varying pressures; and ease of maintenance. But because of the style of operation, gear pumps wear as the pump’s gears mesh, or come into contact with each other, to move fluid. This increases the internal pumping clearances, reducing flow capacity that results in less fluid pumped per rotation while simultaneously increasing slip within the pump. To compensate for these larger clearances the pump speed or size must be increased, which can result in higher energy consumption and accelerate the pump’s wear. The alternative in this gear-wear scenario is to tolerate a lower level of pumping capacity until the pump’s performance drops to an unacceptable level. However, the gear wear can often go undetected by the operator, which can sap the pump of efficiency—both energy- and performance-related—before the necessary maintenance can be performed. Conversely, because the self-compensating vanes in the sliding vane pump continuously adjust for wear, they can allow the pump to maintain near-original efficiency and capacity throughout their life. The pump speed also does not need to be increased over time, making sliding vane pumps natural energy-savers. If the sliding vanes wear out or are damaged, replacing them is quick and easy. Vane replacement can be accomplished by simply removing the pump’s outboard head assembly, removing the old vanes, inserting new ones and reinstalling the head, all without the need for special tools. Also, it is not necessary to remove the pump from the system. All replacements can be completed while the pump remains in line.Future Energy Consumption Predictions
To the surprise of probably no one, in its International Energy Outlook 2017 report, the U.S. Energy Information Administration (EIA) predicted world energy consumption would rise 28 percent between 2015 and 2040, from 573 quadrillion British thermal units (Btu) in 2015 to 736 Btus by 2040. This extrapolation is supported by the EIA’s “Reference case,” which “assumes continual improvement in known technologies based on current trends and relies on the views of leading economic forecasters and demographers related to economic and demographic trends for 16 world regions based on Organization for Economic Co-operation and Development (OECD) status.”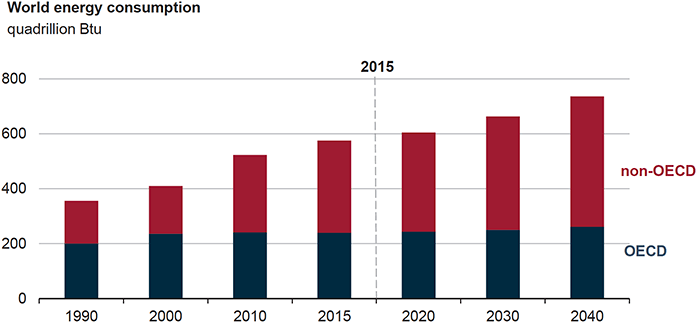
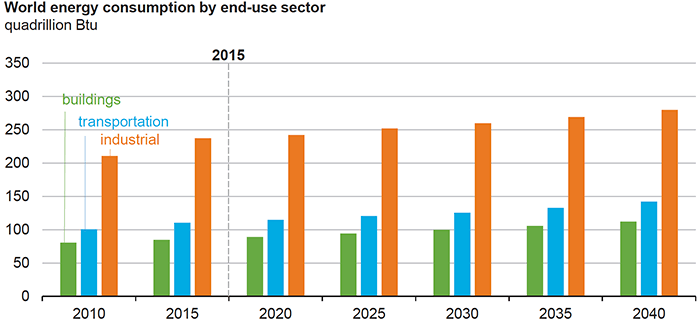