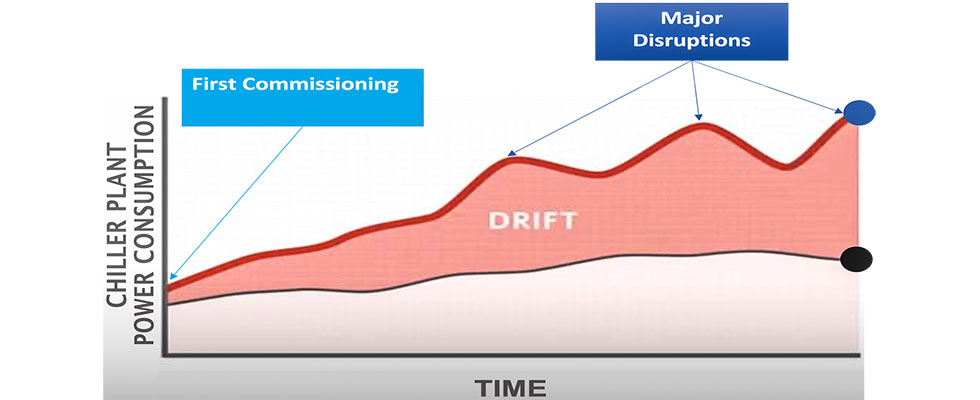
Artificial intelligence (AI) is used to describe a broad concept of intelligent machines that can simulate human thinking and behavior. Machine learning is one application of AI that allows machines to learn from data without being programmed explicitly.
Machine learning, at its most basic, is the practice of using algorithms to parse data, learn from it and then make predictions about something in the world. So, rather than hand-coding software routines with a specific set of instructions to accomplish a particular task, the machine is trained using large amounts of data and algorithms that give it the ability to learn how to perform the task.
This article will discuss how machine learning can be used in heating, ventilation and air-conditioning (HVAC) applications, how it can impact HVAC performance and how it works.
Why Should We Be Interested in Machine Learning Technology?
The choices made around machine learning solutions will impact projects. By implementing machine learning technology, building construction costs can be lowered by up to $3 per square foot. It can also help reduce operating cost by approximately 40 cents per square foot.
The third value of machine learning relates to occupant comfort. Several solutions can provide occupant comfort in existing buildings, but at what cost? The goal is to reach 100% occupant comfort without idle assets so building developers and owners do not have to bear the cost of extra equipment sitting unused for most of its life.
Performance/Energy Drift
As a chiller plant goes through its life cycle, changes affect performance and efficiency. As mechanical systems age, they do not operate as efficiently as they did when they were first commissioned. This change is called performance drift or energy drift.
Drift is caused by small changes in equipment performance due to fouling or incomplete maintenance of certain components, such as clogged strainers or dirty filters. Because of this, the system performance gradually degrades.
Image 1 shows how power consumption increases over time and that there are peaks when disruptions occur, such as small failures or when a maintenance procedure is required. Once the maintenance is completed, system efficiency is somewhat corrected, but system performance generally does not return to the desired level. Note that in most buildings, it is only when a disruption occurs that poor performance is noticed and a correction is made.
The ideal management practice or habit would be to complete full maintenance of all systems, get them working properly
and recommission on a continuous basis. Minor amounts of drift would still occur because of wear on the system, but performance and efficiency would be closer to the ideal state.
Persistence
Persistence is the measure of how energy savings endure after commissioning or recommissioning. This measure does not look at the first days and weeks of operation, but instead looks at the life cycle of the building and provides an indicator of how well the system is maintaining the efficiency for which it was originally designed.
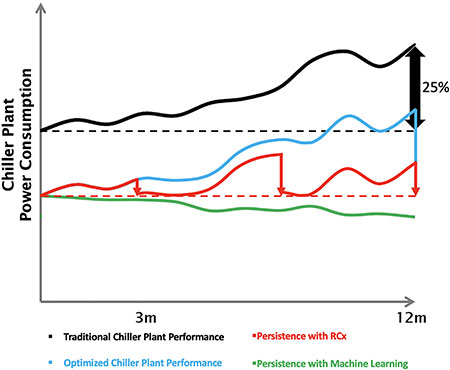
The expectation is that not only can the efficiency targets achieved at commissioning be maintained, but that operators can implement lessons learned regarding plant operation to achieve better efficiencies over time.
Overcoming Drift & Improving System Efficiency
As mentioned, performance in a traditional chiller plant will drift. On average, one would expect to see a 25% increase in power consumption for the same level of output.
Would this change if the system was optimized? In an optimized chiller plant, better efficiencies would be noticed initially, but with no method of identifying the objective for performance has been deviated from, drift would still be seen.
Ideally, to maintain performance, the system would have to be recommissioned every time drift occurs. But how often is a building operator going to do this? Can maintenance staff afford the time to complete this monthly, quarterly, annually or even less often? What will be the effect on operating costs and labor hours? How will this compare to the impact of not doing the regular recommissioning? To really manage the system and maintain performance correctly, recommissions must be done on a continuous basis. This is where machine learning can help.
When machine learning is added, the practice and the technology not only maintain plant efficiencies, they can actually improve system operation and efficiencies over time. With this, combinations and configurations can be learned to operate a plant so that performance and efficiency are better than when the system was first commissioned.
How Machine Learning Works
Machine learning, by definition, processes input data, applies learning through evaluation and improves the quality of the output data.
A digital twin is an exact digital replica of something in the physical world. The creation of a digital twin is made possible thanks to internet of things (IoT) devices that gather data from the physical world to reconstruct the replica in a digital format. With a digital twin, it becomes possible to bring insights about improving operations, increasing efficiency or discovering an issue before it occurs. The lessons learned from the digital twin can then be applied to the physical system with less risk and better return on investment.
So, how is the concept of a digital twin related to machine learning? Often, machine learning is used to analyze a model of operations represented by a digital twin. For mechanical systems in buildings, a digital twin is a data-only representation of all the variables of interest in a component, device or process. Importantly, a digital twin is not a single snapshot.
A digital twin captures new data constantly and updates all the variables of interest over time so changes in a modeled environment can be seen. Based on what is learned, a predictive model using digital twins can be created to understand what the results would be if operated differently.
Machine Learning vs. Existing Traditional Models
The traditional optimization model is an equation-based model with only one road programmed to operate the system. This model has static equations with fixed coefficients only adjusted on day one commissioning when all the equipment is at its best. When equipment needs to be serviced, the equation will not change, and the algorithm will continue to use the
same optimization path. That is what will lead to lost efficiency until the failing equipment gets serviced and the plant
gets recommissioned, leading to drift over time.
On the other hand, by using machine learning algorithms, optimization can occur with real-time traffic data. It is a data-based model using digital twins with an evolving digital control map. Once it has created the control map, it will start operating on that map with the operating points of the equipment. These control maps evolve over time by exploring outside of the optimized operating zones that it has established. This allows for new ways to operate the plant to be discovered.
What Else Does Machine Learning Bring to the Table?
Machine learning brings new opportunities for condition-based maintenance because of the diagnostic capabilities. This provides automatic notifications of any failure of a piece of equipment, notification on service requirements and notification of deviation of performance long before a performance drift starts. This creates an opportunity to improve service protocols; operators can go from scheduled maintenance approaches to condition-based maintenance.
If several plants are connected to a remote diagnostic service in the cloud, and all their information is brought back and analyzed, the learning from one plant is combined to a larger population of similar plants. By looking at multiple sites and applying AI, it can:
- show trends that have improved performance through machine learning exploration mode
- help implement learning right after commissioning of a building
- reduce the wait time of the learning period
Machine learning with digital twins is an evolving data-based model that identifies more efficient ways to operate a plant. With self-learning and self-calibrating capabilities, these technologies ensure persistence through a learning and exploring algorithm. They support condition-based maintenance and transparency in real time for immediate assessment of actions required. These technologies improve building performance, maintenance and occupant comfort.