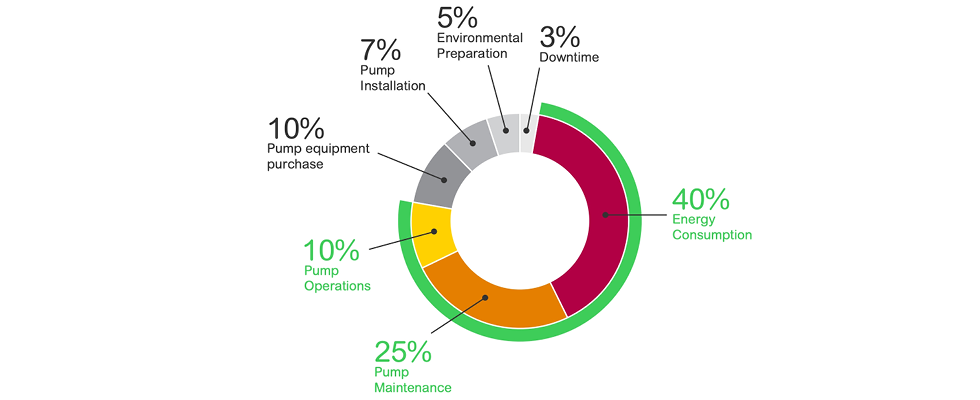
Water and wastewater treatment plants play a vital role in public health, environmental protection and economic sustainability. However, these facilities face mounting challenges, including aging infrastructure, an aging workforce, limited financial resources and the ever-present need for regulatory compliance. Aging equipment often leads to frequent maintenance, costly repairs and increased energy consumption, which can strain already tight budgets. At the same time, operators are under pressure to improve service delivery and enhance resiliency in the face of evolving demands.
Digital transformation presents an opportunity to address these challenges. By leveraging modern technologies such as AI, real-time monitoring, advanced analytics and automation, treatment plants can optimize their pump station operations, extend the lifespan of critical assets and reduce costs to provide a return on investment (ROI) from across a facility.
Digital Transformation Benefits
Digital transformation in pump station operations hinges on the integration of advanced technologies, including the industrial Internet of Things (IIoT), cloud computing and data analytics. These tools enable real-time monitoring and intelligent decision-making, paving the way for improvements in energy efficiency, maintenance processes and overall operational performance.
One tangible benefit of digitization is energy cost reduction. Pumps often operate under conditions that deviate from their best efficiency points, leading to unnecessary energy consumption. With digital monitoring and control, facilities can optimize performance by operating closer to target curves, leveraging more efficient equipment and taking advantage of lower-cost energy periods. Additionally, analytics can identify energy waste and suggest corrective actions.
Digital technologies also enhance maintenance efficiency. Condition-based monitoring allows operators to detect potential issues before they escalate into costly breakdowns. For instance, pressure sensors and analytics can monitor pump suction and alert operators when performance begins to drift. This reduces the reliance on schedule-based monitoring and manual inspections and minimizes labor costs, enabling facilities to focus resources on more critical tasks.
Operational optimization is another key benefit. By synchronizing pump performance with other systems, such as hydraulic networks or auxiliary processes, plants can improve overall efficiency. Real-time data provides actionable insights, helping operators make informed decisions that maximize operational effectiveness.
Digital Pump Station Management Platforms
Digital management platforms are designed to support the modernization and digitization of pump station assets. With integrated architectures that align connected devices, edge control and apps/analytics, operators have access to a more holistic view of their operations for both management and process improvement.
At the foundation of the platform are the connected products, such as pumps, motors, drives and sensors. These are equipped with intelligent capabilities and are interconnected to collect and share data. For example, energy meters can measure real-time consumption, while pressure and flow sensors provide insights into hydraulic conditions.
The edge control layer, which includes programmable logic controllers (PLCs) and IIoT-enabled devices, facilitates seamless data exchange. This serves as the bridge between the connected assets and the analytics applications. It ensures that operational data is processed and delivered to the appropriate systems for further analysis. At the top, cloud-based apps and analytics tools provide actionable insights into energy usage, maintenance needs and operational performance. This might include identifying energy waste points, recommending maintenance schedules or helping optimize systems.
With any digital management platform, cybersecurity must be addressed. Pump stations must strive for the highest cybersecurity levels under the global standards of International Electrotechnical Commission (IEC) 62443. This includes leveraging products that are cybersecure by design, implementing segmentation in the IT/OT architecture, backing up systems regularly and testing operations to ensure employees understand how to maintain a cybersecure environment.
By using this integrated approach, pumping operations are able to achieve reductions in energy, maintenance and operational costs. Moreover, these digital platforms provide the flexibility to adapt to changing conditions, ensuring long-term sustainability and resiliency.
Case Study: Northern Spain Water Treatment Plant
A water treatment plant in Northern Spain serves as an example of the benefits of implementing a digital pump station management platform. The plant faced several challenges, including high energy costs, frequent maintenance and inefficiencies in plant-wide communication.
To address these issues, the plant manager set clear objectives: reduce energy expenses, improve operational efficiency and reduce overall operating expenditures. The implementation process began with deploying a performance improvement architecture, which included existing energy meters, intelligent motor drives and pressure/flow sensors. These devices were integrated with a central IIoT edge box that communicated with the cloud-based digital management platform.
Within three months, the plant achieved the following:
- Energy cost savings: Adjustments to pump speed control reduced energy consumption, saving approximately $8,189 annually in energy charges.
- Maintenance improvements: By shifting to condition-based monitoring, the plant eliminated biweekly inspections, saving approximately $3,509 per year.
- Operational optimizations: Automating the chlorination valve reduced operating costs by approximately $5,300 annually.
Altogether, the plant realized annual savings of approximately $21,641, with ROI achieved in under three months. These savings were attained without replacing aging pumps, as control loop tuning and refurbishment of impellers and wear rings proved sufficient.
Key Takeaways
- Evaluate current operations: Assess the efficiency, energy consumption and maintenance requirements of the pump station. Identify areas for improvement and estimate the potential ROI.
- Implement targeted improvements: Introduce secure digital monitoring tools, adjust control strategies and optimize equipment performance to address identified inefficiencies.
- Monitor progress: Use real-time data to track performance against set objectives. Leverage analytics to identify opportunities for improvement.
- Adjust performance: Fine-tune operations based on insights gained from monitoring. This may involve recalibrating control loops, scheduling maintenance or implementing new operational strategies.
Continuous optimization is critical. As conditions change, ongoing adjustments will be necessary to maintain peak performance. A central digital management platform provides the flexibility to adapt to these evolving challenges while achieving long-term savings and efficiency gains.
Digital technologies are transforming the way water and wastewater treatment plants manage assets. By taking the first steps toward digitization, facilities can unlock new levels of performance and efficiency, ensuring they are equipped to meet the challenges of the future.