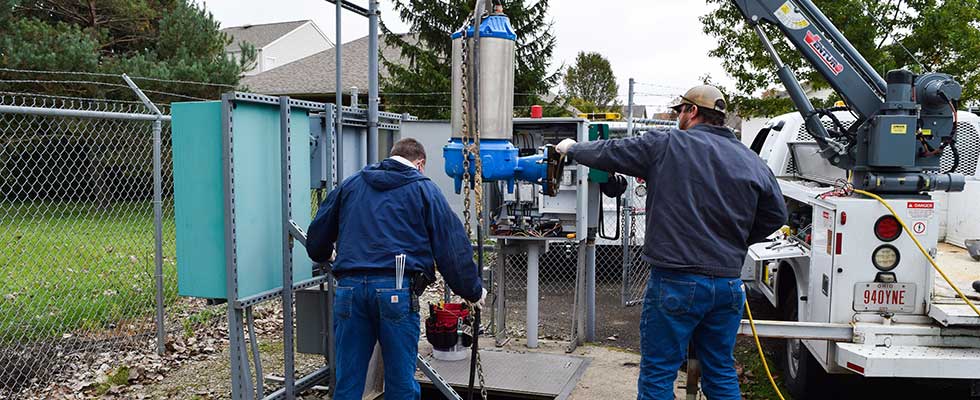
The city of Bluefield is one of the core cities that sits on the West Virginia/Virginia border. Serving a population of about 22,000 people, the Bluefield Sanitary Board is comprised of approximately 350 miles of sanitary sewer lines all leading back to two treatment plants. About 9.5 million gallons of sewer run through the two plants every day, with the Westside Treatment Plant treating 8.3 million gallons and the Ada Treatment Plant treating 1.2 million gallons.
Pump Station Details
Bluefield has seven pump stations, all of which have had consistent problems with clogging issues, mechanical failures and constant maintenance. The pump issues had become daily occurrences as hair and plastic would frequently get stuck in the existing pumps. Each time a pump would clog or fail, it resulted in costly downtime for the treatment plant. Surrounded by mountains, the city of Bluefield prides itself on its community-oriented and safe atmosphere. With these daily issues, the Bluefield Sanitary Board knew that it needed to upgrade its equipment to live up to these promises to the community.
Installation
This was the perfect opportunity for a local distributor to step in and test a new solution for Bluefield. In February 2021, it installed a non-dry run submersible nonclog pump in a triplex dry-pit station at the treatment facility. The pump is a 4-inch discharge, 15 horsepower (hp) pump with a maximum flow of 800 gallons per minute (gpm). With the help of the 4x6 base elbow, the pump was easily installed with minor piping changes from the original pump. Since installation, the pump’s average daily run time has been about seven hours, with eight to twelve starts per day and no clogs since the new pump has been in service. The Bluefield team has noticed a reduction in surface temperature of this new pump in comparison to the other units in the station due to the motor cooling jacket. Since installation, the motor’s max temperature was 90 F, which was attributed to the pump doubling flow on that specific occasion.
Since installation, Bluefield has not experienced any issues with the new pump. Due to the cooler surface temperature, reduced clogging issues with no occurrences since installation and the ease of the installation itself, the Bluefield Sanitary Board is considering replacing the other units in the triplex station with the new pump. It is also planning to outfit the sister station with a similar solution.
Key Takeaways
Pain points from the original installation included costly time and maintenance to unclog debris from pumps on a daily basis. Pumps were running hot, causing safety concerns for those servicing the units. The new pump’s impellers are designed for clogging resistance and optimal pumping efficiency. The new pump’s more efficient motor design with a cooling jacket allowed for a much safer working environment—removing the risk of burns when servicing the unit.