The Hydraulic Institute (HI) is the global authority on pumps and pumping systems. HI develops and publishes pump standards, guidelines and guidebooks through volunteer collaboration by pump industry member professionals. HI published its Application Guideline for Variable Speed Pumping, released in March 2017. One company authored an appendix devoted to the specific technology of eddy current drives (also known as magnetic drives, eddy current clutches or magnetic clutches). These machines are driven at constant speed by an alternating current (AC) motor and use a simple electromagnetic device to control speed to the driven load. The input drum (shown in blue in Figure 1) is a cylinder of magnetically permeable steel coupled directly to the motor shaft and thus rotates at constant speed. The variable speed magnetic rotor (shown in red in Figure 1) is mounted concentrically within the drum.
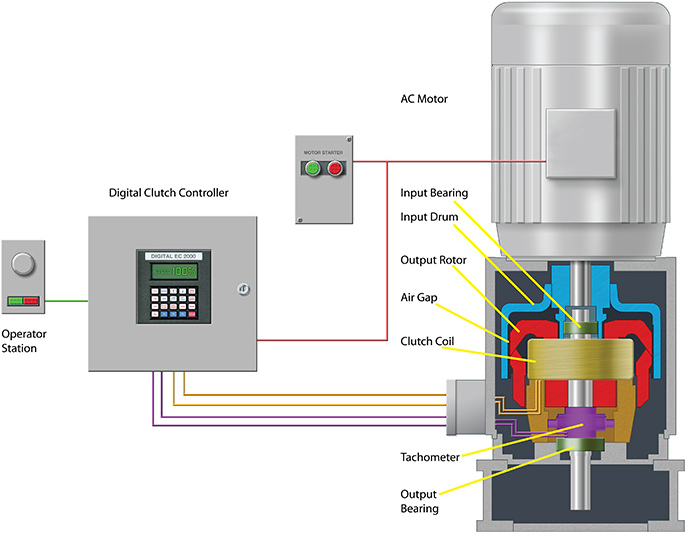
- Long service life. Eddy current drives can be expected to remain in reliable service for several decades, matching the service life of the motor and the pump for which they are used.
- No power source harmonic distortion Because the motor runs directly from the electric utility supply at constant speed, there is no electronic conversion of the power that would generate harmonic interference. No harmonic study is warranted, and no auxiliary equipment is needed for harmonic mitigation.
- No harmonics in the motor circuit The motor runs at constant speed without any high frequency voltage pulsations, which are known to induce elevated shaft voltage. This leads to bearing damage as the voltage finds a path to ground through the anti-friction bearings.
- Audible noise Eddy current drives produce minimal noise in operation and don’t affect motor noise.
- Long leads If necessary, the rotating mechanical equipment can be located several thousand feet from the control equipment without any special consideration.
- Air conditioning unnecessary Losses produced are dissipated by the rotating drum. This drum turns at constant motor speed. Ambient air is almost always sufficient in volume to absorb and dissipate this heat, so no special cooling equipment is needed.
- Small footprint Eddy current drives are easy to retrofit to existing equipment, especially vertical units. The added height is usually easy to accommodate, and the small wall-mounted enclosure for the controller is normally 30 inches by 36 inches.
- Simple to diagnose and repair Generally, eddy current drives can be repaired by local service organizations. Factory assistance is available to facilitate repairs if necessary.
- Obsolescence Rotating mechanical designs are largely unchanged for decades. Controls are available for any eddy current drive ever made.
- Low-end torque An eddy current drive can easily deliver all the torque available from its drive motor at any speed, including zero. This is a significant advantage for starting certain loads, especially positive displacement pumps that have a residual load of pumped material within the pump.