This pared-down technology can make smaller and simpler applications more practical and economical.
05/08/2015
Many pumping stations and other remote locations need a local operator interface and remote monitoring but cannot afford a personal computer (PC)-based human machine interface (HMI). To address this issue, new embedded HMI platforms are becoming available (see Image 1). These options offer much of the functionality of a PC-based HMI but at a lower cost and with a smaller footprint. They are prepackaged for industrial use in the harsh environments often found at pumping stations.
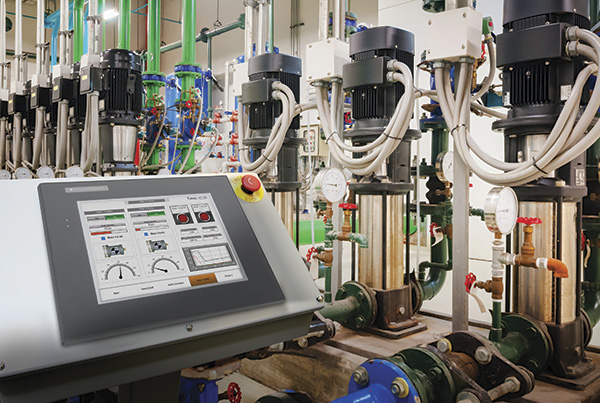
Remote Monitoring Benefits
Remote access allows a single user to monitor and maintain several remote sites in different areas, even if they are in separate regions around the world. In the past, maintaining the same coverage would require several employees. Remote monitoring provides the opportunity for users who are far from the site to solve some problems remotely and react proactively to others. Emails and text messages provide real-time information, giving operators or maintenance personnel the ability to take action before a problem results in downtime or reduced productivity. Personnel do not need to use a browser to find remote site status because data are pushed to them quickly. Once an alert is received, any Web browser can be used to access the HMI and obtain more information. Users can log and store data files of events in the HMI, then access them remotely or send to a group via email using file transfer protocol (FTP). This allows managers to gain insight into trends occurring over time and to be proactive in addressing issues affecting productivity, cost or downtime.Remote Monitoring Options
Any control and monitoring software that runs on a platform capable of hosting an embedded operating system (OS) can be described as embedded HMI. Compared with a PC-based OS, an embedded OS requires much less processing power and memory because it is dedicated to a single function, in this case hosting the HMI software. This results in a lower-cost solution than a PC-based HMI and provides other benefits, such as OS and application longevity. A PC and its OS have a shorter life cycle than an embedded HMI. Replacing the obsolete PC can be complex and time-consuming, as can porting the HMI application to the new platform. A simpler and more cost-effective solution is to use an embedded HMI platform to provide a local operator interface and remote monitoring. These prepackaged solutions are well-suited for the harsh environments often found at pumping stations and offer a myriad of remote connectivity options.Connection to Mobile Devices
Many new embedded HMIs can send notifications through emails or text messages when important events, irregular activities or alarms occur. These embedded HMIs can also be accessed from any Web browser. Most engineers and technicians use a mobile device such as a smartphone or a tablet every day, providing them with a wireless link to embedded HMIs at remote sites. These mobile devices can connect to the Internet with either Wi-Fi or cellular connection and are becoming more inexpensive and common. Embedded HMIs are less expensive and easier to integrate than PC-based HMIs. Their physical design and mounting configuration make installation simple, providing a rugged solution in a harsh environment. If an embedded HMI fails, it can be quickly replaced with a new unit loaded with the same application software. While implementing an embedded HMI platform is simpler than using a PC-based HMI, certain steps must be followed for a successful installation. As with a PC-based HMI, PC-based software is used to configure the desired embedded HMI screens, objects and buttons. The software configuration is then downloaded to the target embedded HMI. These units enable quick integration with automation components using standard interfaces and protocols such as Ethernet and Modbus. When the application requires remote monitoring, as with a pump station, additional steps must be taken for configuration and setup. With many embedded HMIs, setting up the unit for remote browser-based access and sending emails or text messages is relatively simple. The remote site must provide the capability to connect to a network accessible from the Internet. The user simply connects the embedded HMI to the network and configures the Internet Protocol (IP) address. Then security must be set up by configuring built-in embedded HMI tools. The user then configures remote access usernames and passwords along with user access levels. Once connected, users can remotely operate and monitor the local embedded HMI using any web browser connected to the Internet.More Is Better
Some complex installations might require a PC-based HMI (see Image 2). For example, a pump station with scores of pumps, storage tanks, dynamic pipe routing options, and extensive process control and monitoring may be too much for an embedded HMI to handle. In these and other complex installations, the need for the best-in-class connectivity and graphical capability provided by a PC-based HMI can justify the system's higher cost. These installations often also require copious data storage and the ability to monitor dozens of processes—features inherent to a PC-based HMI.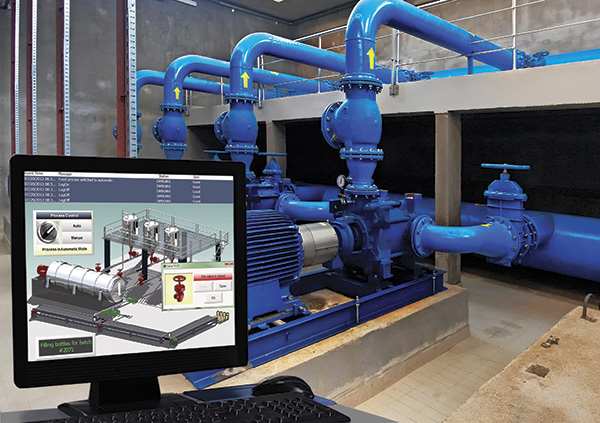
Monitoring Cuts Costs
Most pump stations are monitored remotely and must operate automatically without a local operator. Local monitoring is often required for troubleshooting and making some kinds of changes. An embedded HMI is the best fit for these types of applications. Pumping systems in irrigation applications, for example, can benefit from remote monitoring and control using an embedded HMI. In these applications, multiple pumps control water supply based on demand, with one or more pumps used to regulate water pressure (see Image 3). The demand for water also changes based on time of day and environmental conditions.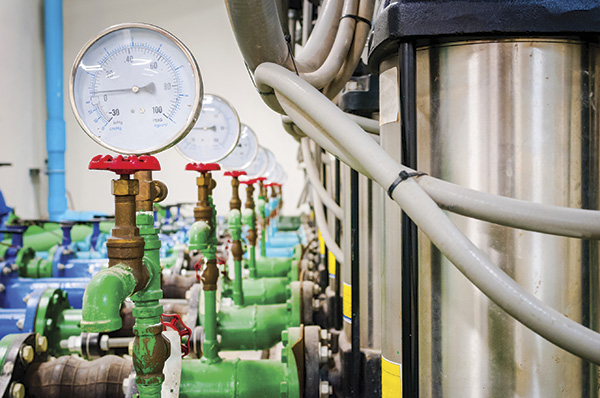
Advantages of Embedded HMI over PC-based HMI
- Compact with minimum space requirements
- More affordable
- Easier to maintain
- Simpler installation
- Simpler configuration software
- Robust industrial design for use in harsh environments
- Longer software life cycle