
In the life of almost every pump installation, there comes a time when the pump needs to be replaced. This may be due to age, failures or the needs of the station having outgrown the pump capability. In the case of wastewater pumps, dry run submersibles are a flexible solution that can replace several other pump types and provide benefits to the user other pump types cannot. This article will review wastewater applications and how dry run submersible pumps can replace other dry run submersibles, true submersible pumps and dry pit pumps, often with minimal upgrades to the station.
A dry run submersible wastewater pump utilizes a motor that is capable of operating submerged or completely dry. These motors can be used with a variety of wet ends—standard solids handling pumps, chopper pumps, screw impeller pumps, grinder pumps, among others. To operate dry, the motor needs to have appropriate cooling, usually in the form of a cooling jacket, which circulates liquid to move heat away from the motor.
Replacing Submersible Pumps
Submersible pumps are usually installed in a lift station containing anywhere from one to four pumps, and often on a rail system. They require a certain level of submergence for motor cooling, which can range from completely submerged to only partially submerged depending on the motor design and where the control levels are set. The distance between the “pump on” level and the “pump off” level is the active volume of the station, also called the storage volume and cycle volume, and is dictated by the design of the overall station and the pumps selected. In submersible pumps, the “pump off” level is set to ensure the motor is properly cooled.
The key difference between submersible pumps and those using dry run submersible motors is the level of cooling required. Submersibles require partial or full submergence, whereas a dry run submersible can operate continuously with the motor fully unsubmerged, which allows the active volume of the station to be shifted down. While this does not
seem like it would have much benefit, it provides more usable space in the wet well, which could be utilized to upgrade the pump capacity.
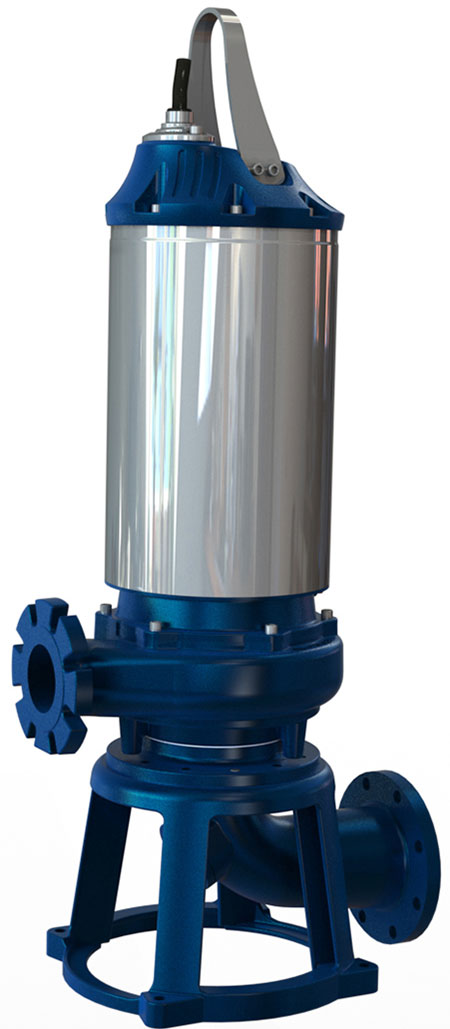
For areas that are experiencing population growth, it could be an easy solution to increase a motor size without changing much of the wet well aside from the pump and control panel. Note the pump discharge size would need to stay the same, as the dry run submersible can typically use the same rail system as the submersible.
Reducing the overall level in the lift station can also keep the wet well a bit cleaner. A constant challenge in wastewater is floating debris, which collects in the station and needs to be removed regularly. This is often done with a vacuum truck cleaning out the entire station, which is costly. Because dry run submersibles can pump the level down closer to the volute, the pumps are more likely to capture some of the floating debris and increase the time between vacuum truck visits.
Both points need to be taken with a note of caution. First, local codes may dictate the control levels and storage volumes, and those take precedence over any other design choices. Second, when setting the “off” level in a station, it cannot be too far down the volute, and that increases the risk of air entering the volute and causing the pump to air lock.
Replacing Dry Pit Pumps
Dry pit pumps have more installation flexibility than submersible pumps in that they can be vertical or horizontal, close coupled or long coupled, or have extended shafts that allow the motor to be installed multiple levels above the pump itself. A critical part of the installation is the pump cannot be submerged, hence the name dry pit. A common installation is a two-well system, where one is a holding well for the wastewater and the other is dry. The pump is located in the dry well and a suction pipe connects the pump to the wet well. This keeps the pump dry while the wet portion operates similarly to a submersible pump station. Dry pit pumps are typically an end suction style and utilize open drip proof (ODP) or totally enclosed fan-cooled (TEFC) type motors and double mechanical seals. Often, the seal chamber needs to have some sort of clean water flush, which adds complexity to the installation, as it requires additional piping, a source of clean water and a secondary pump to move the clean water.
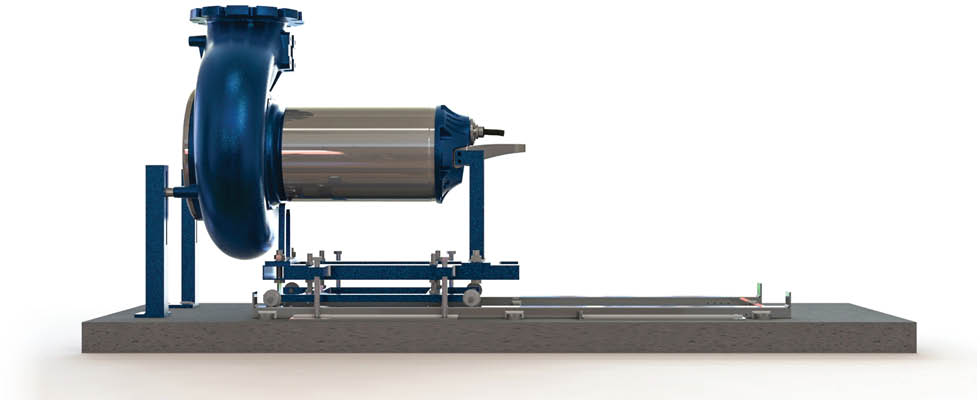
Since dry pit pumps cannot operate submerged, dry run submersibles have an inherent advantage. Not only does this remove the need for the dual well system, but it protects the installation from potential flooding. Flooding can happen for many reasons, including weather related and accidental. Incidents like force main breaks, valve failures and heavy rains can all cause flooding in pump stations. Dry pit pumps can be damaged during flooding, whereas dry run submersible pumps will not only be undamaged, but may even continue to operate, although this is dependent on how the station is designed and built.
The need for a clean water flush is also eliminated with a dry run submersible. Because these pumps are designed to be submerged, the seal chamber is completely sealed from the exterior of the pump. The seals do still need to be lubricated, but this is accomplished through the pumped fluid, the cooling jacket fluid or other means. This can be cost savings for the installation, a reduction in complexity and less equipment to operate and maintain.