Proper selection, installation and maintenance can ensure optimal performance and longevity.
07/21/2016
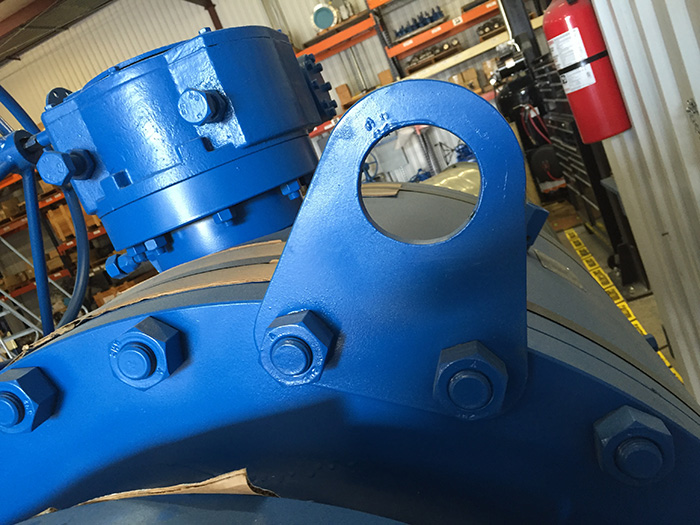
Valve Selection
The most critical factor in maintaining a valve’s optimal performance level is to ensure that the right valve has been selected for the right application. One of the major causes of valve leakage and failure after installation is misapplication by quoting the wrong valve design or material of construction for the media flowing through the valves. The vast majority of valve leaks are caused by misapplication because the right questions were not asked during the quoting phase. It is important to ask the basic questions: What is the media? What is the temperature? What is the pressure? Is it in an open or closed position? Nine times out of 10, the manufacturer will flag a specifications error during the quoting phase for either the distributor or end user to provide more clarification and information because of discrepancies between the valve specs and the operations specs. Reviewing valve specifications diligently and thoroughly, asking specific questions and waiting on the answers at the beginning of a project will save time and money from being misappropriated during the installation and maintenance phase of a project. These steps will also prevent the wrong valve(s) from being quoted. For example, an inquiry arrived for a carbon steel ball valve for a sulfuric acid application. The end user was unaware that carbon steel is chemically incompatible with sulfuric acid. Alloy 20 material was quoted as an alternate option. If this discrepancy had not been caught during the quoting phase, the end user would have received a valve that would not have held up, causing economic damages and potentially disastrous repercussions. One of the most common misapplications occurs in determining when to use a floating ball valve versus a trunnion ball valve. An example of misapplication of a floating ball valve design is when the valve is placed in a vertical position in a low-pressure application. Because of the vertical position, there will not be enough line pressure to push the ball to seal the seats of the valve. A trunnion valve is needed because the energized seats will seal bidirectionally, with no bearing on the pressure of the line or the valve’s position in the line. In this situation, saving money by purchasing a floater would not be advantageous for the end user because the valve would leak.Installation
Once the correct valve for the application has been purchased, end users must be vigilant in the upkeep of the delivered valves while waiting for installation. Allowing valves to sit in the field without protection from the outside elements is a common practice that increases the end user’s cost of ownership because of corrosion. Field technicians add further insult to injury when they remove the valve endcaps. When endcaps are removed, dust and foreign objects will settle in the valve, potentially causing damage to the ball and seats and resulting in leakage once installed. There is no reason to remove the endcaps, as they provide the first line of defense in keeping the inside of a valve clean. Do not remove the valve endocarps. Another problem involves the turning of the travel stops on the valves and actuation. Travel stops are commonly misidentified as a nut or bolt to be tightened. Education about parts of a valve will deter field techs from trying to tighten a travel stop. Simply knowing where a travel stop is located on a valve and actuator, as well as what it looks like, is vital in ensuring that a valve will be able to seal properly. Travel stops are never to be touched because they keep the ball from rotating. The travel stops are preset prior to delivery to the location. Any slight adjustment will cause potential leakage by off-setting the ball of the valve. Do not touch the travel stops. Mishandling an actuated valve by grabbing the neck of the actuator (brackets, couplers, hardware) causes damage to both the actuator and valve. There are lifting eyes on the valves for use when transporting a valve in the field. Again, knowing valve anatomy is key to proper handling. Do not grab a valve or actuator by the neck. The single most important procedure during the installation phase, however, is to purge the lines before they are pressurized. One more piece of advice: “Do not throw trash in the lines. It’s not a garbage can.” That tip seems like common sense, but this is another malpractice witnessed too often.Maintenance
Unfortunately, maintenance programs are often the first to experience budget cuts, but they are the best way to prevent valve and actuation equipment failure. Stroking of the valves and applying general-purpose lubrication at least once a month provides long-term benefits in the functioning of inline valves. Please note that most valve manufacturers will have a preference of which lubricant type to use for optimal performance of their valves. Good preventive maintenance begins when the end user receives the valves at their specified location. The following checklist from a valve/actuation expert highlights important precautions:- Ensure that the valve, actuation and valve control accessories’ bill of materials matches the end user’s specification sheet.
- The valve package(s) must be inspected to ensure that the exterior of the valve(s) and components was not damaged in shipment and all grease fittings are present.
- Ensure that valve process connections are covered to prevent dirt and debris from entering the body cavity.
- Note the valve manufacturer’s instructions on lifting and transporting the valve. For example, the valve should never be lifted by gear drive or actuator. If the valve is to be stored for a period of time before installation, it should be stored in a climate-controlled or dry environment to preserve the integrity of the valve internals.