Compression packing used as a valve stem seal requires a compressive load. The appropriate compressive load can be accomplished by the most common method—to compress the packing by a fixed percentage of its axial height. An alternate method is to use torque measurement on the packing gland hardware. Users should consult the packing manufacturer’s installation instructions to determine the recommended compression percentage or the recommended sealing stress. Once the required sealing stress is determined, the torque required to provide the stress must be calculated. Torque measurement will be this article’s focus. When torque measurements are used to apply the stress on a compression packing seal, two important considerations are the determination of the appropriate load and complete, accurate transmission of that load to the packing.
Appropriate Load and Transmission
Users should always consult the packing manufacturer to determine the appropriate torque method for a packing set. Some variations exist between manufacturers in how the torque is determined and in the sealing stresses that are recommended for specific packing materials. The following is an example of the type of calculations that are used. First, the overall load on the packing is calculated.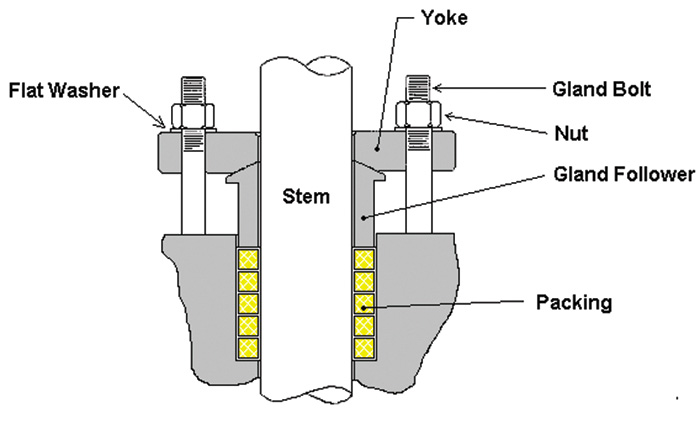
- The gland yoke should not be bent. Hardened, flat washers should be used on top of the gland yoke to prevent galling of the yoke and the nuts.
- The gland follower should be cleaned with a wire brush to ensure that no corrosion, paint or other debris can contact the stuffing box bore and cause resistance to movement or transmission of compressive load.
- Bolts or studs should be replaced if they are corroded, stretched, nicked, cross threaded, excessively worn or otherwise damaged in a manner that would affect the transmission of compressive load. Bolts or studs should be cleaned with a wire brush to remove debris.
- The nuts’ threads should be in good condition and clean, free of corrosion. The nuts should turn freely over the bolts or studs over their entire length of travel.
- Lubricant should be applied to all fasteners and nuts.
- Flat washers should be clean and free of any galling.