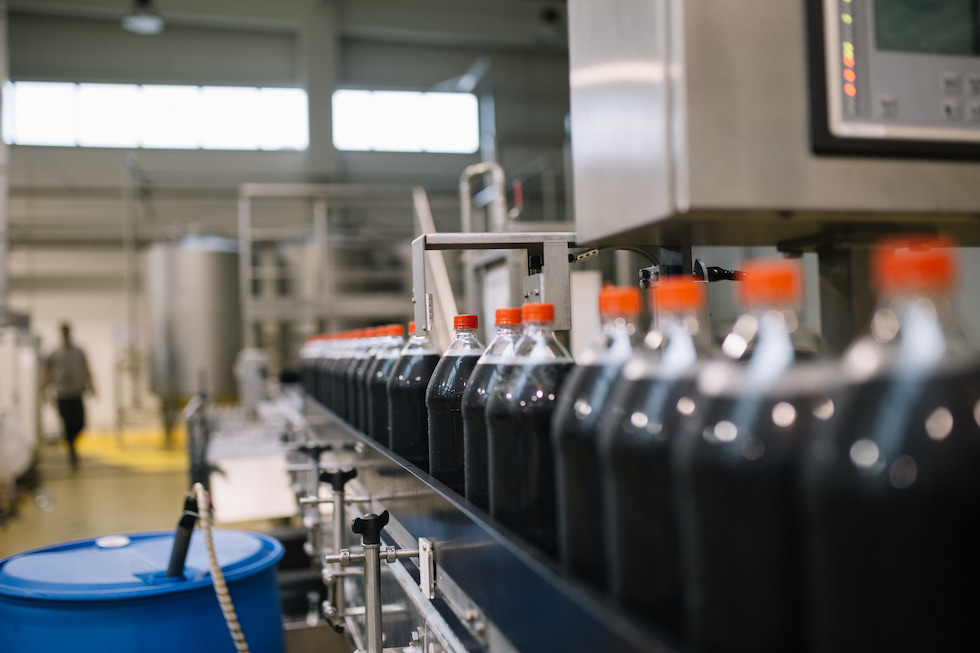
Coca-Cola’s largest franchisee, Coca-Cola FEMSA, solved multiple challenges—odor control, safety enhancement and cost reductions—in one of its 10 large bottling plants in Brazil by installing a reinforced geomembrane odor control system with integrated activated carbon filters at its on-site wastewater facility. Odor control was the primary reason that prompted plant management to take action. The installation of the geomembrane covers also reduced operating costs, including energy and chemical use, and greenhouse gases over the past three years.
The bottling plant is located in the town of Marília (population 230,000). It is about a five-hour drive from the megalopolis of São Paulo.
In 2017, complaints about odors from the wastewater facility at the plant were being received more frequently, particularly from a neighboring hotel. Meanwhile, the operators of the plant had also been looking to improve the safety of the wastewater tanks and investigating cost-saving practices that could be implemented. The Mexico City head office of Coca-Cola FEMSA, which already had several successful installations of odor covers at other wastewater plants in various Latin American facilities (bottling, dairy and juice plants), recommended to the Marília plant managers that they consider installing the same system used elsewhere in their facilities to solve all of Marília’s challenges.
The wastewater plant in Marília had two rectangular reactors with existing rigid covers. They were still emitting odors even while using costly odor-reducing chemicals. Coca-Cola FEMSA Marília decided to go ahead and install the reinforced membrane odor control system with integrated activated carbon filters on the two reactors. At the same time these improvements were implemented, plans to build a new glass-lined steel homogenization tank were underway with plans to cover it with an odor control solution.
The geomembrane covers, which are suspended above the liquid, are made to fit each tank perfectly, providing a tight seal around the edges. This ensures that all gases are forced toward the filters. One advantage considered by plant managers when choosing the geomembrane covers for the new and existing tanks was the “breathability” of the carbon filters. The porosity of the filters prevents pressure from building up below the covers and the subsequent creation of dangerous gas buildup in confined spaces—a key safety feature.
The filter design is engineered to allow gases—such as hydrogen sulfide (H2S) and ammonia (NH3)—and water to flow freely through the filters while they capture the odor-causing contaminants. Gas-specific filters for H2S and NH3 can be combined in the system for optimum control, even under grates and manhole covers.
To facilitate the operation and maintenance of the basins, access ports were included in the geomembranes’ design for each membrane, according to the customer’s specifications.
Third-party contractors installed the geomembrane odor control system on both reactors and the homogenization tank. First, they removed the old rigid covers on the reactors while the new homogenization tank was being built. The simple installation of covers was completed in a few days for both reactors. The installation work of the homogenization tank with the geomembrane odor control system was completed one month after the reactors together with the assembly of the prefabricated tank wall sections.
Once the covers were installed, there were no longer any odors detected from the reactors. Consequently, odor complaints from the nearby hotel and community ceased completely following installation. Since the homogenization tank’s geomembrane covers were pre-installed before commissioning, there were never any discernible odors emanating from its inception.
Benefits of the Cover System
The streamlined structure of the geomembrane cover system, which integrates the activated carbon filters within the reinforced membrane in pockets for easy maintenance and filter changing, offers a potential space-saving benefit to wastewater facilities. Depending on the facility design, the geomembrane cover system could liberate the physical space occupied by pipes, pumps and the chemical dosage unit because they are no longer needed.
Apart from having solved its odor problems, Coca-Cola FEMSA received a quick return on its investment. By eliminating the use of odor control chemicals, the wastewater facility managed to cover the cost of the three geomembrane odor control covers and the installation for the equivalent of what it would have spent on the use of chemicals in a six- to eight-month period.
The only operational expenditures (opex) required with the geomembrane odor control system consisted of changing the activated carbon filters on a regular basis. In the Marília facility, the first filter change was done at the 10-month mark, where previously the filter change was every two-and-a-half weeks. The odor control system also saw cost-cutting benefits resulting from the reduction of energy consumption and labor and maintenance.
The timing of filter changes is a common concern of wastewater facility operators. On average, the life span of filters ranges from nine to 15 months, based on practical experience in a variety of industrial and municipal wastewater plants. Various approaches are used to establish the lifetime of the filters. It is different in each case, depending on the type of gases emitted, intensity, flow, etc.
Some wastewater facilities do sporadic checks with manual gas detection equipment. Others even invest in olfactometric analysis. But if there are no regulatory or other mandated requirements to use instruments for scientific odor monitoring, the easiest and most common method is to use olfactory senses.
Staff at a wastewater facility will simply detect a gradually increasing odor level to indicate the time has come for a filter change. Unless the facility changes the treatment processes, after the first filter change they will have a more accurate idea of the filter changing cycle for which to plan.
The carbon filters integrated into the three geomembrane covers at Coca-Cola FEMSA also function as water drains. For Marília, a town with a hot climate and a torrential rainy season, this additional benefit is invaluable. Rain falls throughout the year in Marília, but there is extreme seasonal variation in the monthly rainfall. Most of the rain falls during the 31 days centered around Jan. 10, with an average total accumulation of 7.8 inches.
Since early 2018, the three geomembrane covers installed at the wastewater facility at Coca-Cola FEMSA’s Marília bottling plant have kept odors under control. Fortunately, the soft drink facility has since remained free from complaints.
With a payback of less than one year, the environmentally friendly, chemical-free odor control system has also achieved a reduction in operating cost and helped the company meet its sustainability objectives of reducing greenhouse gases and protecting the global environment.