The practice of oil analysis has changed drastically from its inception in the railroad industry. In today's exploding computer and information age, oil analysis has evolved into a mandatory tool in one's predictive maintenance (PdM) arsenal. As a PdM tool, oil analysis is used to uncover, isolate and offer solutions for abnormal lubricant and machine conditions. These abnormalities can result in expensive, sometimes catastrophic damage that causes lost production, extensive repair costs and even operator accidents. The goal of an effective oil analysis program is to increase the reliability and availability of machinery while minimizing maintenance costs associated with oil change-outs, labor, repairs and downtime. Accomplishing this goal takes time, training and patience; however, the results are dramatic and the documented savings and cost avoidance are significant.
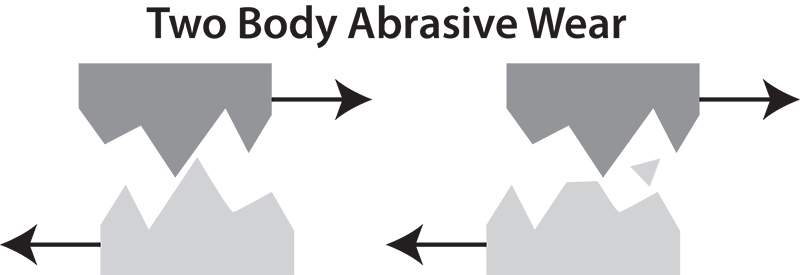
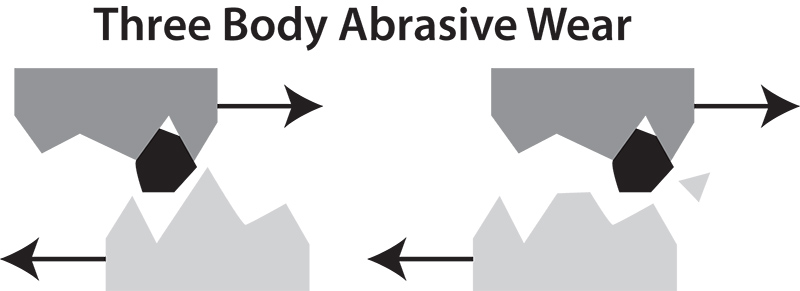
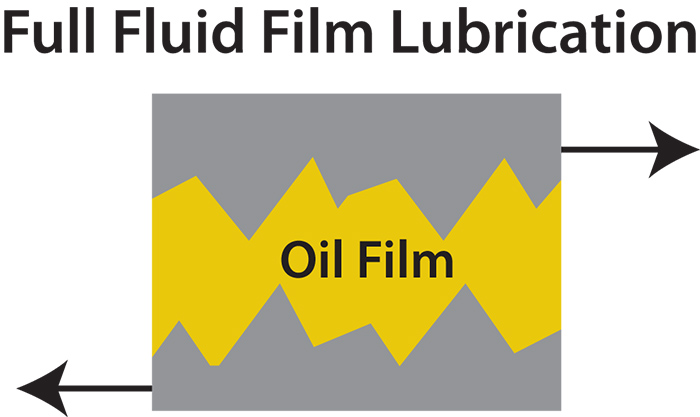
Lubrication Properties
Lube oil analysis helps companies maintain equipment. In order to take full benefit from oil samples' test data, it is important to understand a lubricant's basic properties. Equally important is the understanding of how these properties affect the lubricant's ability to function. Lastly, knowledge of the common test techniques and instrumentation used to analyze oil can aid in data interpretation and lead to more productive corrective action. To effectively monitor how well a lubricant is working, the lubricant's functions must be understood. The primary function of a lubricant is obviously to lubricate, that is, to reduce friction. By reducing friction, wear is reduced, as is the amount of energy required to perform the work. In 1699, a physicist named Guillaume Amontons deduced that friction is the result of surface roughness. Since no solid surface is perfectly smooth, opposing friction surfaces have peaks called asperities that come in contact with one another. Ideally, a lubricant will physically separate these asperities with an oil film. This is called full fluid film lubrication. When the proper lubricant is used and the proper load is applied, the asperities are not in contact and, in theory, no wear will occur. When inadequate lubrication is present or the load is increased, the oil film will not be thick enough to fully separate the asperities. Mixed lubrication, which is a cross between boundary and hydrodynamic lubrication, occurs when the oil film thickness is equal to the average asperity height. The largest asperities will come in contact and result in increased wear. Many oils are fortified with anti-wear additives to combat wear under these circumstances. As load continues to increase or lubrication degrades, boundary lubrication occurs and the oil film thickness cannot separate the friction surfaces. This can result in metal-to-metal contact. At this point, asperities are adhering to one another, causing severe machine wear. This can also manifest itself during periods of shock loading, startup or shutdown. Extreme pressure additives are used in oils that frequently encounter these types of situations.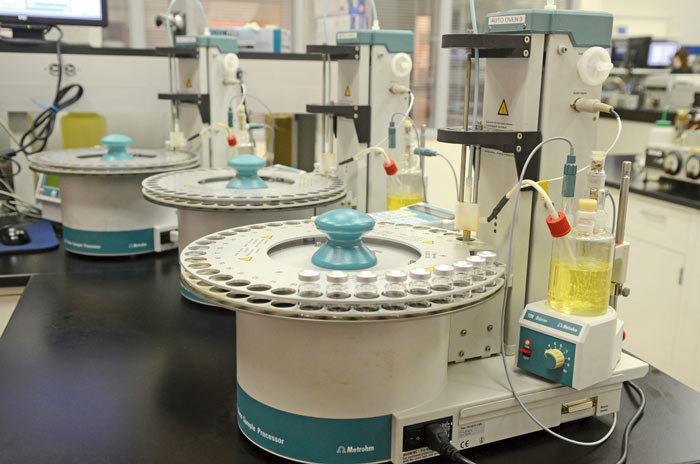
The Role of Oil Analysis
Selecting the proper lubricant, along with maintenance of that lubricant, is essential to ensure protection for any machine. Proper lubrication is defined as the correct amount of the correct lubricant at the correct time. Maintaining a lubricant means ensuring it has the correct viscosity and the necessary additives for the application. Steps must be taken to keep the lubricant clean and serviceable. Oil analysis is the most effective way to prolong the useful life of lubricants, while maintaining maximum protection of equipment. Oil analysis tests reveal information that can be broken down into three categories:- Lubricant condition: The assessment of the lubricant condition reveals whether the system fluid is healthy and fit for further service or ready for a change.
- Contaminants: Increased contaminants from the surrounding environment in the form of dirt, water and process contamination are the leading cause of machine degradation and failure. Increased contamination indicates it is time to take action in order to save the oil and avoid unnecessary machine wear.
- Machine wear: An unhealthy machine generates wear particles at an exponential rate. The detection and analysis of these particles assist in making critical maintenance decisions. Machine failure due to worn out components can be avoided. It is important to remember that healthy and clean oil leads to the minimization of machine wear.
Elemental Spectroscopy
Elemental spectroscopy is a test that monitors all three categories: lubricant condition, wear debris and contaminants. A spectrometer is used to measure the levels of specific chemical elements present in an oil Two types of spectrometers are commonly used. Arc emission spectrometers apply energy in the form of an electric arc to the sample. This excites the atoms into vapor form, creating a spectrum where light is generated. Individual light frequencies in the spectrum are measured and quantified to determine the presence and quantities of specific elements. The other common type of spectrometer is the ICP, or inductively coupled plasma spectrometer. This operates on a similar principle, except the energy is applied to the sample by a plasma flame rather than an electric arc. There are typically 20 elements measured by spectroscopy and reported in parts per million (ppm). These measurements represent elements in solution. Spectroscopy is not able to measure solid particles larger then roughly 7 micrometer (μm), which leaves this test blind to larger solid particles. Typical levels of wear can vary greatly depending on the type of equipment being sampled. For example, a gearbox will normally have much higher levels of iron than a hydraulic system. Levels of wear can vary across different units of the same type depending on oil hours, operating conditions, loading levels or other conditions. For this reason, it is impossible to establish firm limits for any piece of equipment based solely on the equipment type. To take full advantage of monitoring wear, a trend should be established to provide an operational baseline of data. This will ensure detection of abnormal wear rates as they develop and allows for the fact that similar equipment may not wear at the same rate. Monitoring additive levels provides information to ensure the proper lubricant is used for the application and for topping off. Four types of lubricants are generally used in most industrial applications, and each has different additive levels. It is important to note that an oil's level of additives measured by spectroscopy is not necessarily an indication of the oil's quality. The four types of lubricants include:- Engine oils, which will typically contain anti-wear additives composed of zinc and phosphorus. One should expect to see these elements present in approximately 1,000 ppm (±1200 ppm). A detergent package should also be present, composed of some configuration of barium, magnesium and calcium. These levels will vary depending on the oil.
- Extreme pressure oils, which are typically for gear applications. It is common to see significant amounts of phosphorus.
- Anti-wear oils, which include many bearing oils, some gear oils and hydraulic fluids. These oils contain both zinc and phosphorus from 200 to 600 ppm. There also may be very low levels of detergent (magnesium or calcium) present.
- Rust and oxidation inhibiting oils, which are the easiest to identify. They include turbine oils, compressor oil and some bearing and hydraulic oils. These oils have no metallic additives that can be measured by spectroscopy, so there should be extremely low numbers for all additive metals.