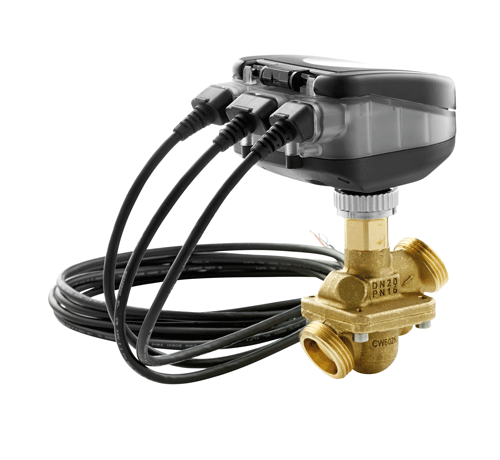
Business conditions in the commercial heating, ventilation and air conditioning (HVAC) market change rapidly. Today’s challenge is to improve indoor air quality (IAQ) at a justifiable cost and reduce the operational expenditure (OPEX) of the building, creating a more attractive investment for the long term. Managers and engineers have to decide how much outside fresh air to use versus increased filtration and electronic sanitization technologies. This is a balancing act. Every building is different. The cost-effective solution is not the same from one building to the next, and the costs to maintain a commercial building are increasing.
Some engineers have found that they can offset the increased cost of IAQ by improving the energy efficiency of the building and harvesting the savings. Optimization of HVAC systems can provide the necessary space comfort for inhabitants while using the least amount of energy. Thermodynamics can help analyze the performance of a building to determine if an energy efficiency strategy is the right choice. Water has always been the most effective and efficient media for heat exchange. With this in mind, how should a hydronic HVAC system be designed?
Hydronic HVAC Design Options
There are three common designs. First is brute force pumping. This is a system where there are powerful constant-speed pumps providing high pressure to force the water to every part of the piping system. When energy costs were low, this was the system of choice. Now, this option is expensive and makes any thermodynamic energy savings impossible to capture. Low Delta T from supply to discharge is an indication that this type of system is not working.
A second option, distributed pumping, places many pumps into the piping risers and horizontal legs. The further away from the chiller and boiler, the smaller the pumps become. The objective here is to maintain constant pressure and fluid velocity throughout the heat exchangers in the system using pumps with variable frequency drives (VFD). This system can be effective, but many pumps require precise control and balancing to maintain consistent building pressures. Pressure-dependent valves cannot be relied on to maintain consistent flow without being rebalanced often. It has been found that maintaining thermodynamic contact between the water and the coil cannot be controlled effectively with these valves. The result is low Delta T with the added problem of higher than comfortable space temperature fluctuations.
Why is low Delta T bad? Look at the performance of a standard chiller. Chillers (and particularly condensing boilers) have performance curves that indicate where they will make the chilled and hot water most efficiently. A high Delta T moves the chiller into the lowest kilowatts per ton and the boiler into the lowest metric million British thermal unit (MMBtu) of natural gas burned.
The third design option for a hydronic HVAC system is the balanced pumping approach. At the onset, maintaining a high Delta T is as important as maintaining space comfort and relative humidity. Here, a new control valve is introduced: the mechanical pressure independent control valve (PICV). In continuous service for 30 years, this technology combines a differential pressure regulator with a linear globe valve in the same valve body. The benefit is that the valve stem can be limited so that the maximum flow to the coil can be set. Then, with use of an electronic actuator, the valve can be opened or closed to modulate the space temperature as needed. In addition, any natural changes in the system pressure are absorbed by the differential pressure regulator. Users now have a system that maintains the highest Delta T automatically. In addition, the least amount of water is used to provide the perfect amount of heating and cooling.
Benefits of Digital Actuators
Traditional controlled actuators offer an analog feedback signal to the building management system (BMS) room controller. Digital actuators transmit many digital system parameters directly to the BMS via building automation control and Network (BACnet) or Modbus. For example, they exchange accurate information about the actuator/valve position, settings, temperatures, alarms, etc., providing actionable feedback on the system’s operation. This allows building managers to optimize system performance and identify pending maintenance needs so that problems can be addressed before reaching a critical stage.
All the information provides system integrators and facility managers with unique insight and remote access to the HVAC system. The actual HVAC data can
be used to adjust system operation, improving the indoor comfort of an energy-efficient building.
So now users do not have to choose between space comfort or energy efficiency as using digital actuators with PICV valves provides both. In addition, increased energy efficiency capture from the pumps and the chillers is possible. The VFD-controlled pumps now need to pump less water since the system is getting what it requires. Less horsepower used means less electricity that can be quantified. The water is coming back at the highest Delta T possible, so the chiller and boiler run at their highest efficiency and lowest cost.
Energy and HVAC equipment costs have been rising consistently for the past five years. The savvy building owner of the future will demand that their mechanical engineer design an energy-efficient HVAC system that will perform well for at least
30 years. Ultimately, analysis of the energy costs and the total cost of ownership of HVAC systems should dictate the selection of PICV with VFDs for energy-efficient HVAC performance that gets the balance right.