Fifth of Six Parts Parts 1 through 4 of this series (Pumps & Systems, November 2015, December 2015, January 2016 and March 2016, respectively; read them here) discussed what engineers and facilities can do to minimize the risk of breakdowns resulting from new challenges in wastewater transport, including the increased use of so-called "flushable" wipes. It is important to note that special side conditions or particular requirements that cannot be changed are increasing the risks associated with wastewater handling. One example is sewer pressure drainage systems that have long pipelines (high pressure) but low flow. The combination of low flow, high pressure and high solids content with wipes should be a red flag that prompts engineers to consider more details in early stages of a project. Applications such as large stormwater retention tanks, which collect a lot of rags and have to be emptied in a short period of time, or pump stations that have dischargers but also low flow, such as those near retirement homes or hospitals, must be addressed carefully during the planning stage. As mentioned previously in this series, sewage grinders can solve some of the issues with larger ragballs at these types of pumping stations; however, problems at the treatment plant will increase if the screen cannot stop the smaller particles going through the system. The chance that this content, full of small waste particles, will enter rivers and oceans is pretty high. As a result, it would be much better to pump the wastewater as it is up to the screen in front of the treatment plant and remove the wipes and fibers there. Many of these challenges have been solved successfully in real-world applications, so some specific technical solutions are available. Outlined below are two proven options for very heavy cases. As mentioned above, pressure drainage systems often are used for residential development areas. Most of the time, grinder pumps or pumps with vortex impellers are used. Both kinds of pumps have limits, especially when it comes to very high heads and low flow. In this case, it makes sense to use a solid-separation system. This innovative technology temporarily prevents solids and other sewage content from reaching the pump while allowing the pump to handle the complete content afterward (see Images 1 and 2). This process enables the hydraulic to use smaller free passages without clogging, leading to higher efficiency and a less limited head.
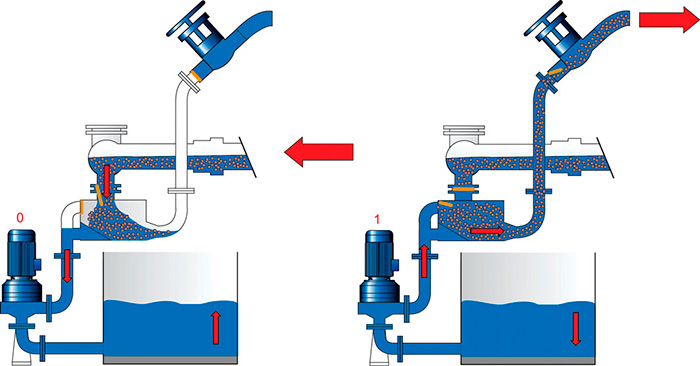
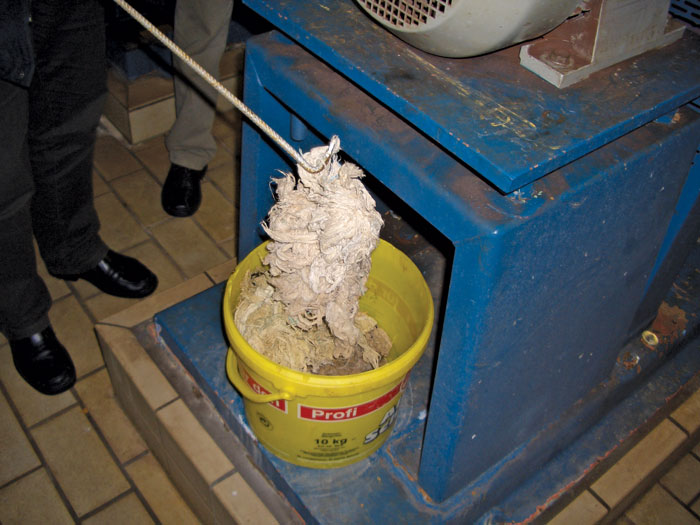