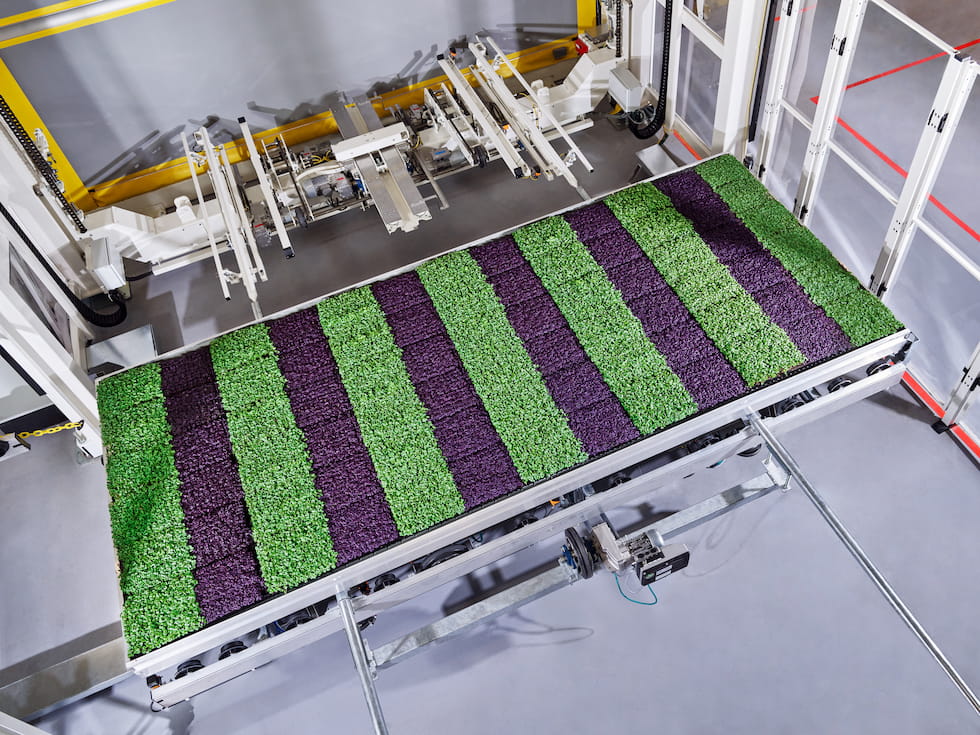
Growth in America’s greenhouse horticulture market—projected in 2019 at a compound annual growth rate of 11.3% from 2018 to 2023 by Wise Guys Reports—is driving strong demand for accurate, versatile mixing systems that can deliver nutrients, growth stimulants, crop protection products and even air into irrigation and hydroponic systems.
Today’s closed-system farms—greenhouses and vertical farms—are built around smart systems that precisely administer inputs and react to changes in crop stage or environment. In short, they provide perfect growth conditions, not just for crops that range from cabbage to cannabis, but for pumps and systems experts, too.
Closed-system farms are taking many shapes, from classic glass-roofed greenhouses of all sizes to compact freight farm installations inside 40-foot shipping containers, a 90,000-square-foot AeroFarms site being constructed now in Abu Dhabi, and a 150,000-square-foot vertical farming project by Britain’s Jones Food Company taking shape in Danville, Virginia.
Few industries have captured the imagination of both farmers and Silicon Valley entrepreneurs like indoor agriculture. Foodies salivate over the chance to savor truly local produce in crowded cities. Utopians celebrate the chance to provide nutritious produce to people in food deserts and supply-short supply chains. And no-nonsense pragmatists see dollar signs where top-quality fruits and vegetables can meet high-paying markets without running up astronomical freight bills.
High Inputs
Plenty, which is developing warehouse-scale indoor farms from coast to coast with investment from the likes of Amazon’s Jeff Bezos, says 1 square foot of one of its vertical farms can yield 350 times as much produce each year as a square foot of farmland. Plenty also says its produce requires just 1% of the land and 5% of the water used in conventional vegetable production.
Every drop of water in closed-system indoor farms is managed carefully. In drip-irrigated and hydroponic systems, water is more than just vital nourishment for plants; it is also the delivery mechanism for plant nutrients, crop protection and air around their roots. Everything about that water—from sourcing it (often from municipal supplies) to the inputs it carries to the energy required to treat, deliver and recycle it—is costly. So, efficiently managing every ounce, as well as every ounce of the other materials it carries, is key.
State-of-the-art closed-system farm management has its roots in the long history of greenhouse production. And for generations, greenhouse managers have relied on either water-run pumps or Venturi injectors for dosing and mixing inputs into their water. As closed-system farms become more precise, growers are assessing their choices with an eye toward ever-greater precision and efficiency.
Dueling Technologies
Water-run pumps use pressure from the irrigation flow to push up an injector piston, which draws in a dose of fertilizer or chemical before being forced back down by a spring. Each pulse delivers a known quantity into the sealed chamber, and injection rates are calculated as a ratio to the flow of irrigation water through the main line. Venturi injectors use flow pressure to compress a stream of water in a constricting conical inlet chamber
and then release it through its outlet port. As the flow expands in the outlet port, it creates a vacuum that draws in nutrients, chemicals or air and mixes it thoroughly. Injection in Venturi systems is measured in percentages (parts per million or gallons per acre).
Venturi injectors contain no moving parts, so there is minimal wear and virtually no maintenance. In contrast, water-run pumps require regular replacement of seals and springs, which increase capital and maintenance costs. Venturi injectors can be specified in sizes ranging from a half-inch to 4-inches in diameter and controlled with almost infinite precision, and they blend injected materials into the irrigation stream evenly.
A Venturi injector creates a homogeneous mixture that is going out into that irrigation system. Water-run pumps usually require a mixing chamber or static mixer. Users must also consider compatibility with biological products like compost teas or microbial pesticides; pistons can exert a lot of force and tear up the microbes.
Under Pressure
Venturis create a pressure differential of about 25% between the chambers. They can be used for modern drip and hydroponic systems, which typically run at 8 to 12 pounds per square inch (psi), which is less than the 30 or 40 psi mainline pressure.
Aerated Irrigation Water
The injection system can aerate the crop root zone. International studies of the air injection systems—which use a Venturi to inject air into irrigation water—indicate that aerating the root zone increases yield and quality in a wide range of crops.
A recent study at the Center for Irrigation Technology at California State University, Fresno, and Memorial University of Newfoundland, Canada, suggested that this type of technology improved nitrogen use efficiency, reduced nitrogen oxide production potential, and altered the microbial population of the soil in favor of aerobic bacteria that tends to coincide with more vigorous crop growth.
Root zone air injection with Venturis can improve an operation’s carbon footprint, as well as its energy bill. Air can also be injected with microbubble and nanobubble systems, but as with water-run pumps, they require energy and maintenance.
an automatic fertigation unit, manual mixing process or air injection system, using the flow of irrigation water to create a vacuum that draws and mixes inputs. (Image courtesy of Mazzei Injector Company)
Given the mission of most closed-system farms to raise the bar on food quality and lower their carbon footprint, pump and systems professionals should consider using Venturi injectors and other sophisticated tools to help take these facilities to the next level and make urban farmers’ space-age dreams come true.