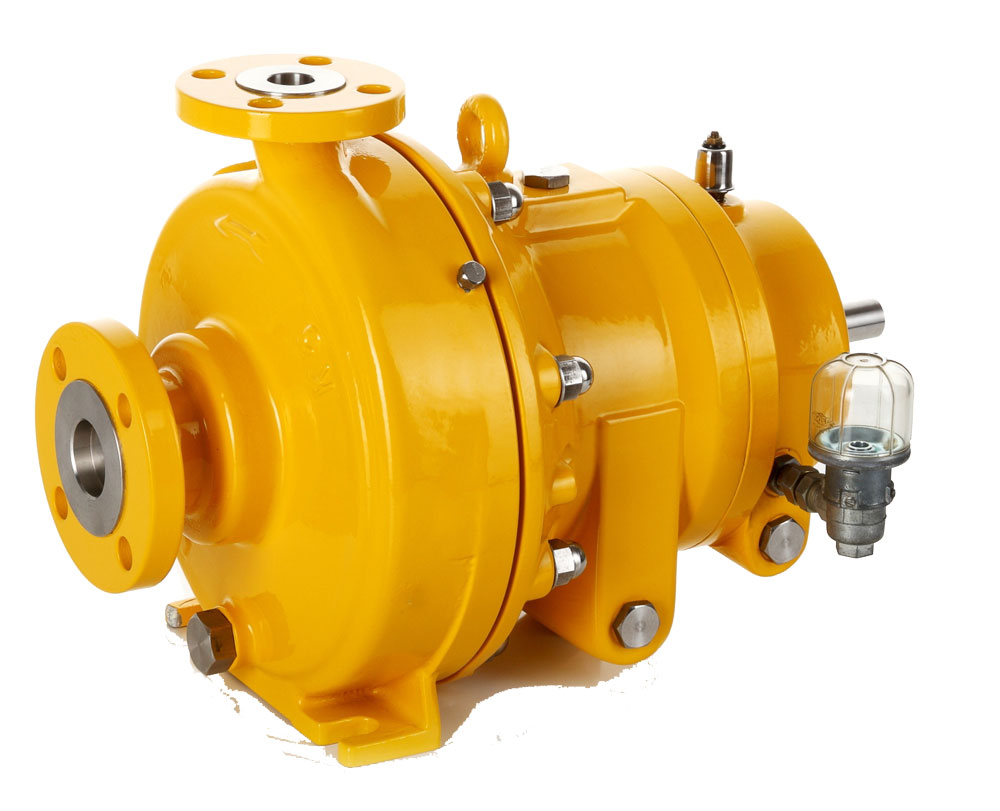
The chemical industry is one of the first industries to return to pre-pandemic production levels. Extensive demand in China, India and North America is fueling this growth. As demand for products in other markets returns to normal, the chemical processing industry (CPI) plays a related role because glass, plastics, vinyl and thousands of other materials made with chemical processing are essential. Below is a look at some of the faster growing segments of the CPI.
Chlor-Alkali
Almost half the world’s chemicals depend on chlor-alkali products, which come from salt. Chlorine and caustic soda are produced when an electrical current is introduced into an aqueous salt brine solution. Chlorine is used in 15,000 commercially traded compounds (including bleach, plastics and many others). Caustic soda (sodium hydroxide) is used to make 10,000 products— including paper, textiles, detergents—and for water treatment. A wide range of pumps and compressors are used in the chlor-alkali process.
Isocyanates
Isocyanates are the raw materials that make up polyurethane products. They are used in the automotive industry to make paints, coatings, foams, car seats and rubber. Isocyanates are pervasive in the construction industry via varnishes and insulation materials. They are also used to make a variety of packaging materials.
Agricultural Chemicals
Chemical agents like herbicides and insecticides control crop-harming insects and weeds. Nitrogen-based fertilizers (like ammonium nitrate and urea) are produced from natural gas. Typically, American Petroleum Institute (API) 610 multistage pumps or sealless mag-drive pumps are used in these processes, as well as API 617 centrifugal compressors.
Polycarbonates
Polycarbonates (PC) are thermoplastic polymers that are easily molded but virtually unbreakable. Their durability and low-scratch resistance make them ideal for windows, eyewear, automotive windshields and more. Each year, almost 3 million tons of PC are produced globally. PC is manufactured by dissolving chlorinated solvents in water. It is a toxic process that is corrosive to the pumps handling the input materials. As a result, sealless pumps are a preferred option for PC manufacturing.
Inorganic Specialty Chemicals
Water, salts, acids and bases form the bulk of the inorganic chemical market. These chemicals are produced by hundreds of manufacturers and are used in virtually every industry. As an example, sulfuric acid is the most produced chemical in the world.
Plastics & Polymers
Hundreds of chemical companies use base chemicals to make polyethylene for bottles and containers; polypropylene for packaging; polyvinyl chloride for piping and construction materials; and polystyrene for toys, recreation equipment and appliances. These plastics and polymers represent more than half of the CPI’s output worldwide.
Requirements for Pumps Used in Chemical Applications
Solutions specific to a user’s requirements
Chemical companies move some of the harshest materials on the planet. Leaks can cause health and safety issues, as well as plant downtime. CPI manufacturers have differing needs, ranging from standard “off-the-shelf” pumps to highly engineered equipment that is designed specifically to flow, pressure/head and material handling requirements.
Manufacturers that best serve the CPI should have the ability to support both ends of the product spectrum. They should work with users in a consultative fashion for the design, construction, testing and commissioning of equipment. A pump manufacturer’s quality and testing processes should be rigorous, regardless
of whether the product is off-the-shelf or not, in order to ensure there are no surprises for the user once the equipment is installed.
Leak-free handling via sealless pump designs
Many of the compounds used throughout the CPI are classified as human carcinogens. Effects of hazardous exposure can include lung problems and severe irritation to eyes, nose and skin. For the pumps handling these substances, leaks must be avoided. As a result, sealless magnetic drive pumps are commonly used. With sealless pumps, there are no leaks or emissions to the atmosphere, offering a cleaner working environment with a reduced probability of accidents. Standards play a key role in the CPI, assuring customers that performance and safety requirements are met while also guaranteeing interoperability throughout a plant. Pumps should adhere to all American National Standards Institute (ANSI), American Society of Mechanical Engineers (ASME) and International Organization for Standardization (ISO) standards. For petrochemical applications, sealless pumps should comply with API 685 standards. Chemical resistance
The precursor materials pumped in CPI applications are toxic and aggressive so the pumps used should feature corrosion-resistant containment shells. Lined pumps with ethylene tetrafluoroethylene (ETFE) containment shells are a preferred option. This configuration resists corrosion and provides durability for a pump’s internals. As an example, the chemical polymers used to coat the electrodes in lithium-ion batteries are extremely harsh, and they have a reputation for corroding pump internals. It takes materials like ETFE to stand up to highly corrosive chemicals. For higher temperature applications, metallic pumps are required. Materials (including stainless steel, alloy 20 or alloy C) with silicon carbide internal bearings should be available, as it takes a wide range to address the needs in the CPI.
EHS and ESG
Environmental, health and safety (EHS) and environmental, social and governance (ESG) issues are more important than ever. Many CPI companies use EHS and ESG scores as criteria for purchasing pumps and compressors. Shareholders and employees at these companies also care about these issues; so, it is essential that equipment manufacturers provide updates relating to EHS and ESG.
Aftermarket support
Pumps in chemical plants can run for decades. Equipment manufacturers should be proactive when it comes to re-rates, exchanges and service. Manufacturers should have service centers that can provide local support anywhere in the world. They should not wait for problems to arise before proactively engaging with users. Exchange programs for the key elements (such as the mechanical seal and gearbox) offer opportunities for pump manufacturers to connect with end users at appropriate times when equipment is nearing service milestones. A pump manufacturer’s channel partners should proactively make sure that users are always aware of their options to keep equipment running at peak performance.
Flexibility to address changing conditions
Chemical manufacturers face challenges when a plant’s process conditions change. For two years, plants (in almost every industry) have reduced capacity or quickly ramped up capacity. As process conditions change, equipment needs to be tuned and re-rated. It is important for pump manufacturers to make flexible equipment that can be easily adapted to address changing plant requirements.
Availability despite supply chain issues
Every business today faces supply chain issues. CPI users that require highly engineered equipment should consider the lead times associated with conceptual design, procurement, construction, testing and commissioning. Providers can mitigate long delivery times by manufacturing equipment on multiple continents.
Examining the total cost of ownership
About 10% of the cost for equipment is the initial purchase. Another 10% comes from the installation.
Almost 50% of the total lifetime costs are operating expenses (i.e., the power bill). Single-stage pumps can deliver multistage performance. Efficient designs should be specified where smaller motors can be used to save on power costs.
Roughly 30% of equipment total cost of ownership (TCO) is due to maintenance costs. To increase pump reliability and to reduce maintenance costs, equipment used in the CPI must be engineered to run at its best efficiency point (BEP). The use of corrosion-resistant materials and secondary containment options extends meantime between maintenance (MTBM) intervals, while also reducing the need for unplanned maintenance. There is also a wide range of ancillary financial benefits that come from deploying sealless pumps for CPI applications—eliminating seals means there are no seal support systems to maintain. In addition to simplifying installations and reducing spare part inventories, this also enables maintenance resources to be deployed elsewhere in the plant. Eliminating leaks and emissions reduces additional risks with Environmental Protection Agency (EPA) monitoring. Minimizing the probability of accidents reduces a plant’s liability, which can help to reduce insurance costs.
When it comes to deploying pumps for CPI applications, operators should seek equipment that is safer for operations and better for the environment, and they should seek solutions that offer the best total value. The eight criteria presented in this article provide operators with a useful guide to evaluate and select the right pumps for chemical processing applications.