The design behind this common pump type.
Hydraulic Institute
05/08/2018
How does a centrifugal pump work?
A. A centrifugal pump is a type of rotodynamic pump that uses bladed impellers with essentially a radial outlet to transfer rotational mechanical energy to the fluid primarily by increasing the fluid kinetic energy (angular momentum) and increasing potential energy (static pressure). Kinetic energy is then converted into usable pressure energy in the discharge collector. A cross section view of a centrifugal pump would show the use of a rotating impeller to add energy to the pumped liquid. The liquid enters the impeller axially at a smaller diameter, called the impeller eye, and progresses radially between the vanes until it exits at the outside diameter. As the liquid leaves the impeller, it is collected in a pressure container casing. One design, referred to as a volute, collects the flow and efficiently directs it to a discharge nozzle. Image 1 highlights the discharge nozzle, which is shaped like a cone so that the high-velocity flow from the impeller is gradually reduced. This cone-shaped discharge nozzle is also called a diffuser. During the reduction in velocity in the diffuser, energy in the flow is converted to pressure energy. An optimum angle of seven to 10 degrees is used to most efficiently convert velocity energy to pressure energy.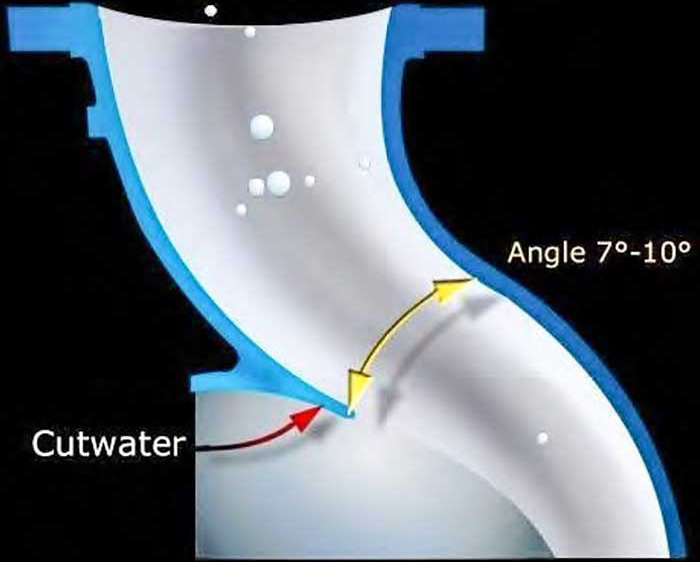
See other HI Pump FAQs articles here.