In 2015, irrigation accounted for almost 42 percent of all freshwater withdrawals in the United States, according to the U.S. Geological Survey (USGS) (1). This amounted to about 118 billion gallons per day. In addition to agricultural use, irrigation of golf courses, parks, nurseries, turf farms, cemeteries and other self-supplied landscape-watering uses also are included in the estimate. Agricultural irrigation accounted for about 81 percent or 95.6 billion gallons per day of the total. Surface water sources supplied about 52 percent and groundwater sources supplied about 48 percent of the total for agriculture. Many irrigation systems are pressurized and therefore need a pump. Because the heart of most irrigation systems is the pump, it is important to select the correct type for the irrigation system and it must be as efficient as possible.
Considerations for Choosing a Pump
Choosing an irrigation pump is based on the type of pump and also on the relationship between pump efficiency and the total dynamic head (TDH) at a specific flow rate. Types of pumps used in agriculture irrigation include:- centrifugal (above ground)
- deep-well turbine
- submersible
- propeller
- the type of water source
- the required pumping flow rate (determined by the irrigation system requirements)
- total suction head (lift from the water surface to pump intake)
- total dynamic head (total pressure supplied by the pump)
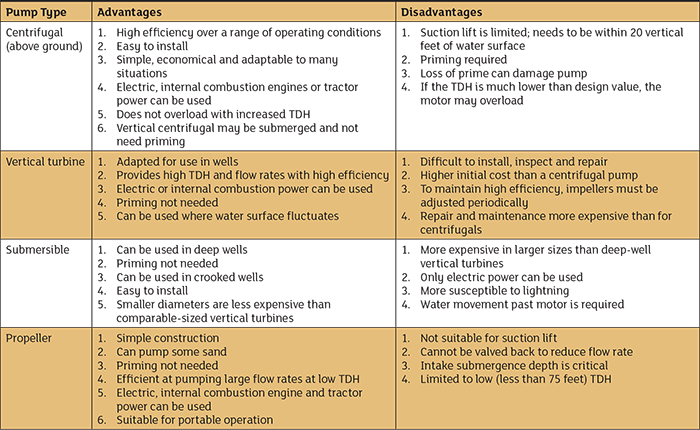
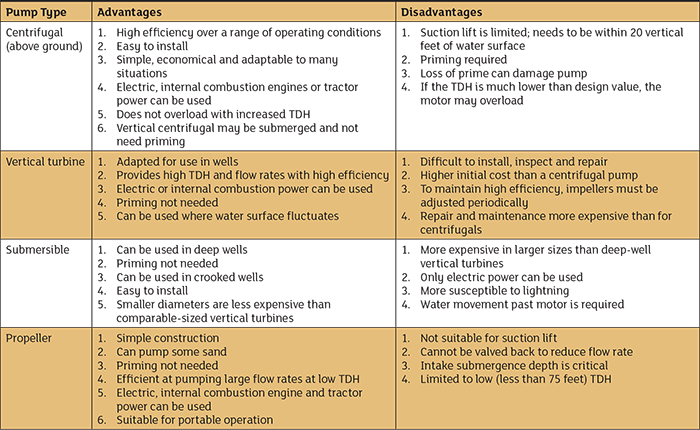