If you had researched the Industrial Internet of Things (IIoT) online in the mid-1990s, there may have been a handful of results. Now, maintenance automation is finally gaining a foothold in industry, but it is being held back from realizing its full potential by limited access to the contextual data related to items like pump wear and pump system performance degradation. As more industrial devices gain intelligence and internet connectivity, their data histories are increasingly exposed, offering advanced maintenance applications a richer supply of data for analysis. CISCO projects that more than 50 billion things will be connected to the internet by 2020, resulting in more traffic, more data, more storage and more energy consumption.1 Looking at this from an industrial perspective, IHS reports that only 9.1 percent of the more than 23.8 billion process and discrete automation elements are currently networked, but the compound annual growth rate of such deployments will increase to 24.1 percent in 2019.2 As an example of how increasing digitization might improve pumping system operations, some industry experts look to improve communications between drives and pumps. Pumps are typically dumb assets. They turn based on the amount of electricity supplied to them. But if the pump operating curve can be imbedded into a drive, when the drive sends electricity down into the pump, it knows how fast the pump should be turning. If the pump is not fitting the profile, the drive can contact someone to find out why. Increasing digitization of this sort will impact maintenance at all levels: reactive, preventive, predictive and prescriptive.3
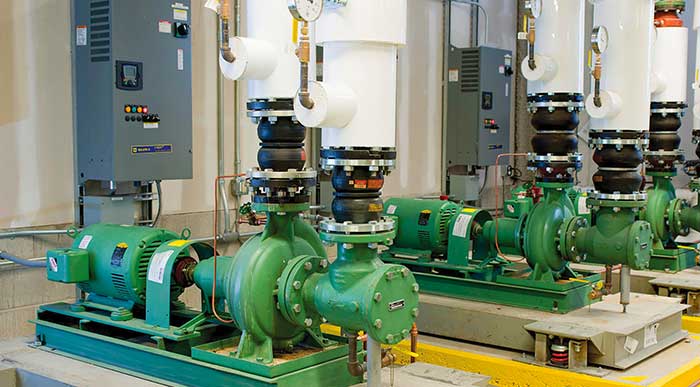
Limitations of Preventive Maintenance
Preventive maintenance has been shown to reduce costs over the lifetime of the asset, but it has its limitations. Preventive maintenance is based on the assumption that assets deteriorate at predictable rates based on age and utilization, which is valid. But the ARC Advisory Group points to U.S. Navy research showing that only 18 percent of equipment failures result from aging equipment. Preventive maintenance will not necessarily address the other 82 percent of random operating failure causes. However, IIoT may improve tracking, scheduling and other aspects of preventive maintenance, and promises to enable condition monitoring based on the analysis of complex variables.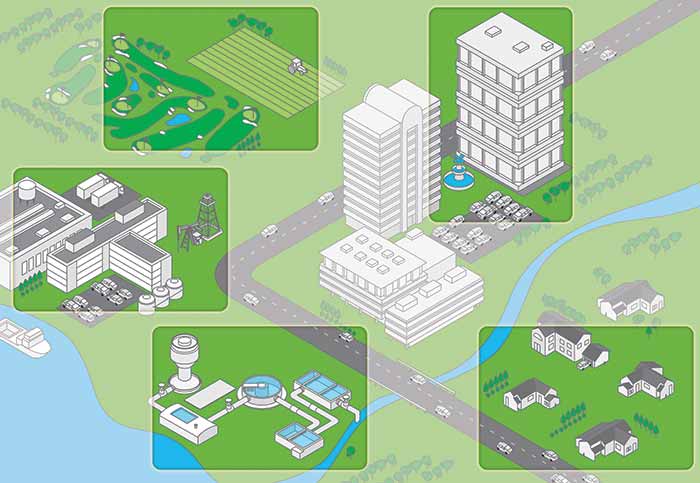
Delivering Predictive & Proactive Maintenance
Predictive and prescriptive (sometimes called proactive) maintenance strategies stand to gain the most from IIoT. In both approaches, process data is monitored to identify trends and issue alerts prior to failure. Predictive condition monitoring, as defined by ARC, is most appropriate for simple systems, where single variable math can be used to predict failure. More complex systems involve prescriptive condition monitoring where multiple variables are analyzed to predict failure. The advanced data historians and analytical software needed to deliver the potential of IIoT are already in place to help process the deluge of operating data that could be flowing in. Today’s data historians can collect data for analysis and report on asset operations, health, maintenance and regulatory compliance. They can collect continuously streaming time-series data from critical control, monitoring and smart devices, then archive this data—increasingly in the cloud using advanced storage and compression technologies. IIoT makes it possible for more companies to achieve measurable benefits within the pumping system, while extending the possibilities as well. It enables the real-time collection of data on the system operation, which can extend the lifespan of any pump asset and reduce capital expenses. Improved operating data helps capture the knowledge of experienced workers, which flattens the learning curve for new hires and helps minimize unplanned downtime.Maintenance Benefits
The following five trends are converging around IIoT to help more companies achieve maintenance benefits:- Advances in edge control enable flexible deployment of control systems with the power and flexibility to handle advanced analytics and the big data needed to support them.
- Expanded use of Ethernet connectivity in controls is making it easier to capture and share data, then analyze it with advanced applications.
- Deeper cybersecurity protection leverages the value of open standards that are essential to realizing the full potential of IIoT with less vulnerability to cyber attack.
- The advanced object-oriented engineering environment is simplifying the deployment of strategic asset management models.
- Asset management models themselves are evolving.

- increased productivity
- increased operational visibility
- cost-efficient energy management
- cybersecurity protection