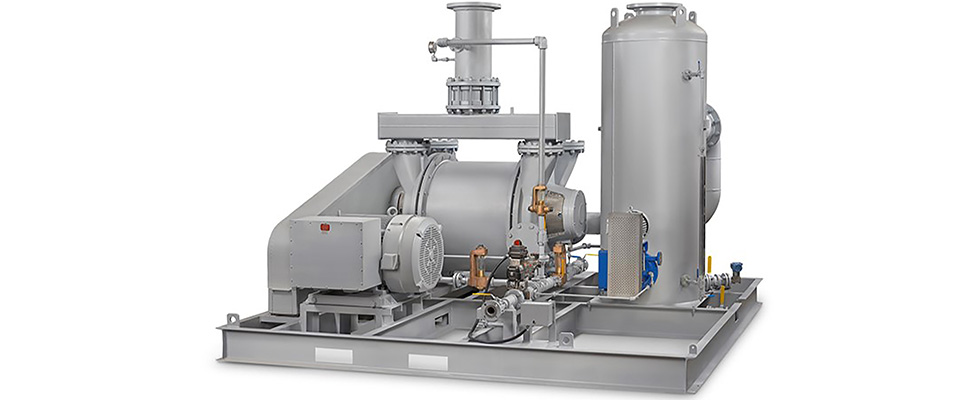
A packaged pump system could be compared to assembling an automobile from the ground up, specifically for each user. Each would have the same starting point of selecting an engine and drive train.
The end user would then choose the components—chassis, suspension, transmission, electrical controls, etc.—to build a vehicle with certain characteristics that meet their particular needs, such as fuel economy or speed and handling.

3-Torr service. (Images courtesy of Dekker Vacuum Technologies)
Similarly, a packaged vacuum pump system is a fully operational, plug-and-play, designed/manufactured product consisting of a vacuum pump and all necessary components, pipework and control units that specifically meet the application and industry requirements of the user. It is a turnkey vacuum system. All major vacuum pump manufacturers have the capabilities and expertise to package pumps into a fully operational system.
What’s in the Vacuum Package?
The process for producing a packaged vacuum system begins by choosing the pump type (liquid ring bareshaft, rotary vane module or screw set), and determining parameters such as working capacity (actual cubic feet per minute [ACFM]), motor size, brake horsepower (BHP), motor voltage, area classification, type of drive and inlet or discharge connection type. This is the engine and drive train.
The package assembly begins by adding a coupling, gear box, variable frequency drive (VFD), V-belt drive or direct drive with an electric motor or a gasoline or diesel engine onto the specified frame. Some manufacturers of rotary vane pumps offer the pump, drive, electric motor and 2-phase discharge separator as an off-the-shelf package.
Packaged systems typically include matched components such as inlet and discharge separator tanks, precondensers, heat exchangers, valve technology, gas ejectors, boosters, exhaust gas condensers, sensors, frequency converters and regulation/control systems.
Piping specifications are part of the complete package design and include materials of construction, threaded and welded parts, flanges, gaskets and appropriate specifications for constructing the pipe system and testing it. Consider a package system if maximum reliability and efficiency is the main goal.
Advantages of the Packaged System Model
The manufacturer offers single-point responsibility.
A single-source supplier streamlines the important communications and collaboration that takes place with the user. Facilitation becomes much more convoluted when several suppliers must coordinate their activities.
The manufacturer understands their own products best.
The engineering teams of each pump manufacturer have years of experience with their own vacuum pump or compressor design, performance and operation, as well as how their products are best used within the industry.
This knowledge allows them to engineer and design systems that precisely target user considerations, such as durability, reliability, energy consumption, low maintenance, environmental footprint and life cycle costs.
The manufacturer provides all final completed system testing and operation (or factory acceptance testing [FAT]).
These inspections involve mechanical run tests (testing electric motor, vacuum pump or compressor and circulation pump if included), checking electrical controls (making sure that all electrical controls/starters are working as specified) and testing performance (ensuring that the vacuum pump or compressor is performing as specified).
The manufacturer produces a detailed operation manual of the system for the user.
The manufacturer can provide necessary startup assistance.
Ordering a Packaged Pump System
There is the occasional need to replace just the pump of on an older existing system, usually under emergency circumstances. More often, new projects that involve replacing a complete, older system or an expansion, new production line or new plant require a new packaged system via a collaborative effort between buyer and manufacturer.
Vacuum users today understand that vacuum pumps and systems, especially liquid ring, are complex in their design and operation. Challenging issues such as gas/vapor load, saturation, and the compression of flammable and potentially explosive gases require knowledge of vacuum technology and the industry.
Packaged pump system customers gravitate toward the pump manufacturers that specialize in their industry. Most manufacturers produce vacuum systems for general industrial use that meet specific OEM or large volume end user applications that also specialize in major industries such as power generation, pulp and paper, petrochemical, mining, wastewater, and food processing and packaging.
Even under most nonemergency situations, fulfilling orders can still be time consuming. The period of time from taking the order until the equipment ships can vary from a few days to six months or so, depending on project complexity.
A simplified packaged system process will involve these steps:
1 Specification
Some knowledgeable users will have detailed specifications entailing the performance required, materials of construction, standards, testing, inspection, tagging and painting. Others will require consultations and site visits to develop the completed specifications. In this case, the manufacturer will usually require a few weeks to finalize the specification.
2 Quote
If the user already has specifications developed, it can take from as little as a day to as much as three weeks for the manufacturer to make a quote. The user reviews the vendor quote or quotes. Selection is based on vendor experience, the solution itself, initial price, delivery, operating costs, terms and conditions, warranty and other factors.
3 Manufacturing
After the order is placed, the vendor creates shop drawings. When drawings are approved, the process moves on to the manufacturing stage. This may be when the installation review determines the location and available space for the package.
4 Final completed system testing, operation and shipping
Once FAT is completed, the system would be packaged for shipment per user specification. If it is not part of the specification, the vendor would package for shipment according to the normal protocol.
5 Startup
To properly and safely start the new packaged system, the manufacturer, engineer or field technician may assist with commissioning (testing to ensure the system performs as anticipated and correcting any problems prior to operation) and training plant operators and the engineering team.