Integrate critical assets in a single network.
Behr Technologies
12/13/2018
The worldwide pump market has witnessed significant uncertainty in recent years due to the sinking price of oil and other commodities. Stagnant end-user demand and stringent energy efficiency regulations create further challenges. Pump manufacturers also face difficulties when it comes to maintaining, servicing and managing on-field products.
Operational Challenges of Pumps
Pumps are extensively deployed in many process industries, including power generation, oil and gas, mining, and water and wastewater. For all of these industries, minimizing asset downtime and increasing process transparency is a high priority since it augments performance and cuts down on costs. Pump failures disrupt an entire process, leading to equipment service costs, expensive production losses, impaired product quality and increased production waste. In hazardous areas such as oil fields, fires may even be ignited, resulting in disastrous consequences. Failures, nevertheless, are often detected only after pumps actually malfunction. Comprehensive on-site inspections are required to diagnose the location and causes of incurred failures before overhaul and reparation activities can be carried out. Since the whole process is time-intensive, plant downtime and accompanied costs quickly escalate.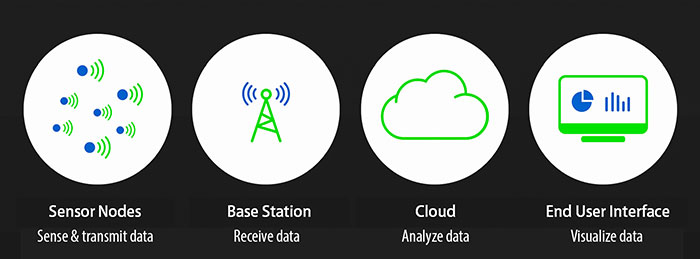
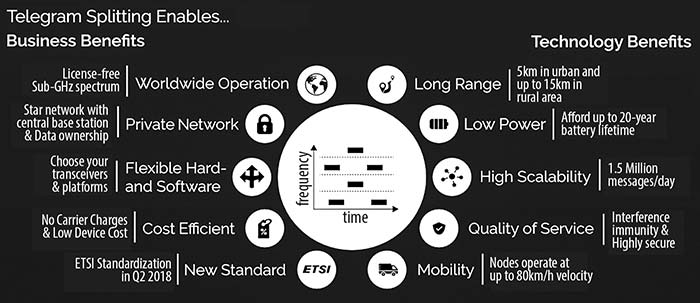