While instrumentation and monitoring software are widely used in manufacturing facilities around the world, these tools alone will not solve every production problem. In addition to software and other resources, the field workforce plays a major role in the overall effectiveness of a plant's reliability strategies. This is especially true in the pump industry because pumps are frequently located in remote or difficult-to-access locations. For this reason, instrumentation and remote monitoring software must be combined with tools that empower the field workforce to manage and maintain systems reliably and efficiently. This comprehensive strategy can help field workers increase their knowledge of system processes and procedures, analyze important equipment information, and make well-informed decisions.
The Importance of Remote Monitoring
A comprehensive reliability strategy is vital because two primary elements make up nearly 80 percent of the total cost of ownership (TCO) of pumps: energy consumption and maintenance activities (see Figure 1). A variety of pumping applications demonstrate that remote monitoring of energy consumption is critical to energy optimization. In addition, remote monitoring of the pumping equipment can result in increased uptime because of the ability to prevent unexpected failures. Because pumps represent more than 50 percent of all energy savings potential and consume almost 25 percent of all motor energy, energy savings is one of the most clearly quantifiable benefits of incorporating remote monitoring into a facility's predictive maintenance strategy. The ability to monitor and adjust system operation to ensure optimal energy consumption is a primary benefit. While data collection through remote monitoring cannot improve efficiency on its own, it is a critical first step to closing the loop around process variables.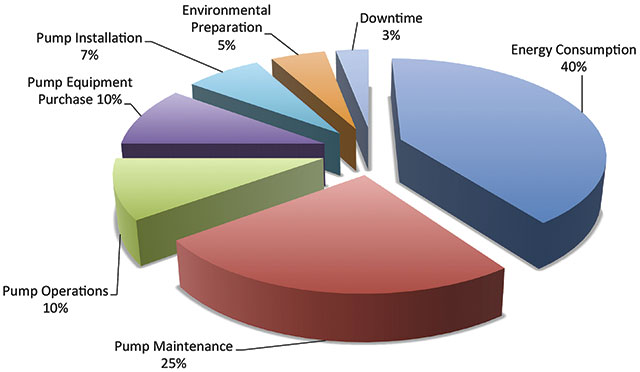
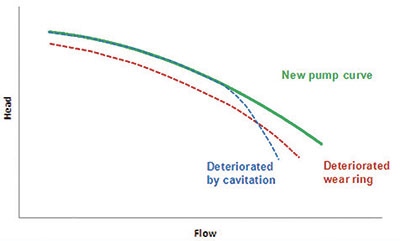
Improving Predictive Maintenance
Predictive maintenance can be custom-designed for a user's specific system, built from regular observation and recordkeeping that can reveal trends and uncover anomalies. When equipment is commissioned, a facility may create a pump health log to use as a baseline for alarms and required maintenance triggers during the lifetime of the system. End users can leverage this historical data to take future actions to optimize their operational efficiency. With minimal investment using standard features built into a variable frequency drive (VFD) or other smart motor control system, users can greatly expand reliability and reduce operational costs. For reference, users should remember that pump equipment purchase prices are estimated to account for only 10 percent of the overall lifetime expense of the system.Monitoring Stranded Assets
Stranded assets, or assets that are not instrumented or only partially instrumented, are found in industries such as refining, upstream and midstream oil and gas, petrochemical, metals and mining, power generation and distribution, water and wastewater, pulp and paper, and discrete manufacturing. In some cases, stranded assets can make up as much as 40 to 60 percent of a plant's total asset count. Because these assets are not constantly monitored electronically, field personnel must monitor the equipment to ensure that it remains safe and reliable. In addition to stranded assets, a host of regulations require that personnel fill out forms that ensure compliance with such rules. Many companies rely on paper-based or experience-based monitoring of stranded assets and compliance activities. But others have adopted advanced mobile decision support software applications that allow them to collect, report and analyze non-instrumented data. Every option for remote monitoring of stranded assets has pros and cons. For every option, however, users must decide how to combine remote monitoring with human interaction. For example, when paper and experience are relied on as the preferred methods for monitoring stranded assets, field workers often lack the situational awareness to make well-informed decisions. Differences in experience level, miscommunication, training deficiencies or employee ownership may result in poorly made decisions that can lead to premature equipment failures, unit shutdowns or even worse—personal injury. By contrast, when companies adopt advanced mobile decision support applications running on mobile computers, they are able to achieve the following:- Positive asset/location identification
- Remote access to standard procedures
- Heightened situational awareness
- Advanced scheduling
- Visibility to non-instrumented data