In the universe of industrial manufacturing, the general definition of the term unit operation is rather benign: a basic step in a process. In the world of chemical processing, however, unit operations are much more than that. Namely, they are the blueprint for the series of production stages that must be precisely completed for the manufacturer to turn a collection of raw materials into a viable end product. There are five classes of unit operations in chemical processing. This article will focus on fluid-flow processes, which most commonly consist of transfer, filtration, solids fluidization and transportation activities. For reference, the other four unit operations are heat transfer (evaporation and heat exchange), mass transfer (distillation, extraction, adsorption and drying), thermodynamic (refrigeration and gas liquefaction) and mechanical (crushing, pulverization, screening and sieving). Over the years, centrifugal pumps have built a reputation as the default pumping technology for fluid transfer applications in chemical processing. In all fairness, centrifugal pumps do possess the basic capability to meet the operator’s needs in these situations since their method of operation makes them well designed for the high-volume transfer applications that are common in the industry. Centrifugal pumps also work well with thin, water-like fluids that must be transported through networks of piping with variable flow rates.
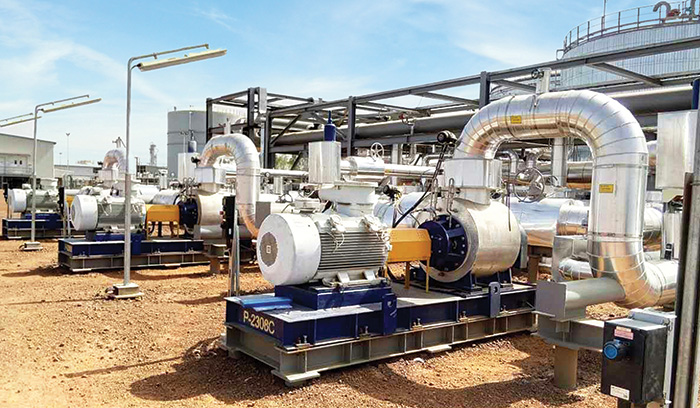
The Challenge
The biggest challenge in making the screw pump more prevalent in chemical processing applications is moving the industry’s operators away from the ingrained perception that centrifugal pumps are the one and only choice for their fluid transfer requirements. In many cases, chemical processing systems have been designed around the pumping technology, rather than the other way around. This means that engineers are first familiar with centrifugal pumps and attempt to work within their operational limits. They know how centrifugal pumps operate, know their benefits and are confident that they are the best technology for what they are trying to accomplish. Based on this mindset, design engineers will design systems that can blend or heat raw chemical materials or compounds as a way to manipulate the process and bring the viscosity of the fluid down to less than 300 centistokes (cSt), which makes the fluid more manageable for the centrifugal pump to handle. In this case, what they are doing is reconditioning the fluid to fit the pumping technology—irrespective of the cost impact. Despite the ability to recondition the fluid to meet the operational needs of the centrifugal pump, operators must still ensure that the centrifugal pump is operating on or near its best efficiency point (BEP). Centrifugal pumps rarely operate at their exact BEP because pristine pumping conditions are seldom experienced. With this in mind, a centrifugal pump is assumed to be operating at its highest level of efficiency in a window between 80 percent and 110 percent of its BEP. However, when the operation of the pump moves too far to either side of the BEP, uneven pressure will be applied to the impeller, which can lead to increased radial thrust that will cause the pump’s shaft to deflect. When deflection occurs, higher loads will be placed on the bearings and mechanical seal, which will damage the pump’s casing, back plate and impeller..jpg)
- Oversized pumps are often chosen as a way to lessen the complexity of pump selection, which can result in increased operation and maintenance costs, inefficient operation and higher-than-necessary energy consumption.
- In centrifugal pump operation, flow rates decrease as differential pressures increase. Therefore, time-sensitive operations that are dependent on maintaining a constant flow rate will take longer, which may be costly. Centrifugal pump performance will be adversely affected when pumping a fluid that has a viscosity greater than 100 cSt.
The Solution
One alternative can be positive displacement (PD) screw pumps. The difficulties with increasing the use of screw pumps in chemical processing are twofold: the built-in advantages of the centrifugal pump’s vast installed base, and convincing design engineers to acknowledge that there are alternatives like screw pumps. Many engineers are also of the opinion that screw pumps are capable of producing only low flow rates. In reality, today’s screw pumps have experienced remarkable advancements in terms of the flow rates that they can create, with flow ranges from 220 gallons per minute (gpm) (833 liters per minute [L/min]) to 11,000 gpm (41,635 L/min) increasingly common. The design of PD screw pumps makes them capable of handling various liquids, even those with higher viscosities. The screw pump’s method of operation allows opposed screws to engage in order to form a sealed cavity with the surrounding pump casing. As the drive screws turn, the fluid is shifted and steadily and constantly conveyed to the discharge port of the pump, which creates a volumetrically consistent flow rate regardless of the pumping pressure. The list of benefits provided by screw pump technology in chemical processing fluid transfer applications is a long and significant one:- ability to handle a wide range of flows, pressures, liquid types and viscosities
- constant flow, even in the presence of varying backpressures that are created by viscosity changes
- high volumetric and overall operating efficiencies, resulting in reduced operational costs
- controllable output or capacities possible through high pump turndown speed ratios
- low internal velocities
- self-priming operation and good suction characteristics
- low mechanical vibration that lengthens service life
- intrinsically smooth and quiet operation
- extremely low pulsation that reduces stress and prolongs the life of associated fluid transfer components (piping, hoses, seals, bearings, etc.)