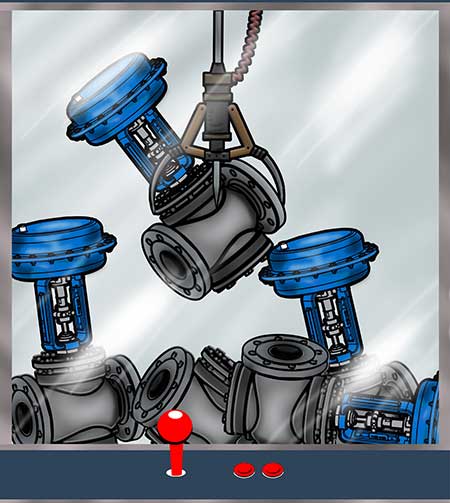
When selecting a control valve for a pipeline to serve as a pressure, flow, tank level, temperature or metering control valve, the first common misconception for someone new to the process is to oversimplify it. If something can fit in a pipeline and it modulates, it will work, right?
Wrong. In many cases, when approaching this situation, one might rely on an International Society of Automation (ISA) sizing sheet, where information on a particular valve tag, for a particular system, in a particular pipeline is readily available. What happens when a user is without an ISA sizing sheet though, and is charged with fitting a control valve to a pipeline to perform a particular job?
There are many characteristics to consider when selecting a control valve.
To start, collect all the information available about the pipeline—the function of the control valve and a little about the system that it is in—and draw a rough piping and instrumentation diagram (P&ID) sketch of how it will work together, for reference. Key factors to keep in mind during the process include:
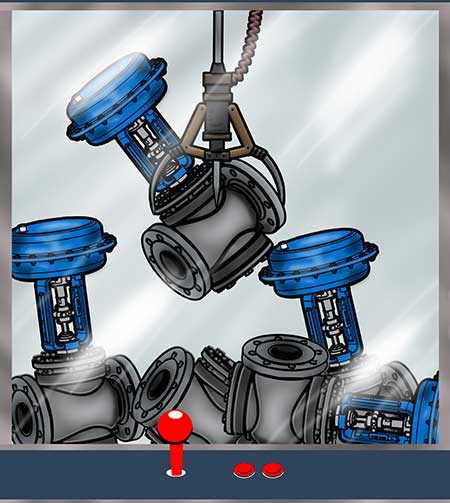
- What is the fluid, and what is its temperature?
- What is the inlet pressure?
- What flow rates are required and under what pressure drops on the valve are presumed adequate?
- Based on this fluid, are there special materials of construction choices that must be made?
- Based on the maximum inlet temperature and maximum inlet pressure, what American National Standards Institute (ANSI) pressure class does this valve safely fall into?
- What function of control valve is envisioned—two-way, balanced, unbalanced, caged? Three-way mixing/bypass? Three-way diverting?
- What style of control valve is envisioned?
- What type of actuator is preferred—pneumatic, electric, self-contained?
- If pneumatic, what air pressure is available?
- If electric, what voltage is available for power?
- What is the area that the control valve assembly must fit into and does the actuator orientation (vertical versus horizontal) come into play?
- Is the valve modulating 100 percent of the time or does it also have to function as a close-off valve?
- If it does also act as a close-off valve, what would be the acceptable leakage factor? ANSI Class IV or ANSI Class VI, for example?
- What is the control signal?
- Are there other required accessories for the valve, testing requirements or area classifications?
Many of the choices to make are dependent on or interactive with other attribute selections.
The process of sizing and selecting a control valve requires a great deal of product and industry knowledge, independent research on products, along with familiarity and training on sizing and selecting tools.
Control valve manufacturers often produce several valve styles and, within these valve styles, several different product series with different characteristics offered. Users must realize what happens inside a control valve to first learn about how damage can result from oversizing or cavitation. There are also special flowing conditions, like flashing or choked flow,
to consider.
While it does not take a lifetime of experience to properly size and select a control valve, patience and thorough research are a must for any application. In the end, be sure to secure a computerized report detailing how the valve is performing to ensure accuracy.