Upgrades include integrated control electronics and IE4-rated motor efficiency.
Xylem
10/04/2018
Aging infrastructure, global urbanization, increasing energy costs and the need for sustainable solutions make cost reduction and reliability a priority in wastewater pumping. Small wastewater pumps can be given a new level of functionality and intelligence by integrating advanced software functions and state-of-the-art hardware into a conventional submersible design. Sensing the operating conditions, intelligent pumping systems make smart decisions and provide feedback to the operator.
Understanding Pain Points in Pumping Wastewater
Market survey responses indicate that many pump users are constantly looking to lower energy consumption and overall costs while achieving higher reliability and longer lifetime of the equipment..jpg)
Integrating Intelligence
An answer to these challenges is the creation of integrated intelligence in wastewater pumping. This is made possible by innovation and adaptation of components in a submersible wastewater pump: integrating electronics such as processor, software, sensors, synchronous electric motor and self-cleaning hydraulics inside a submersible shell.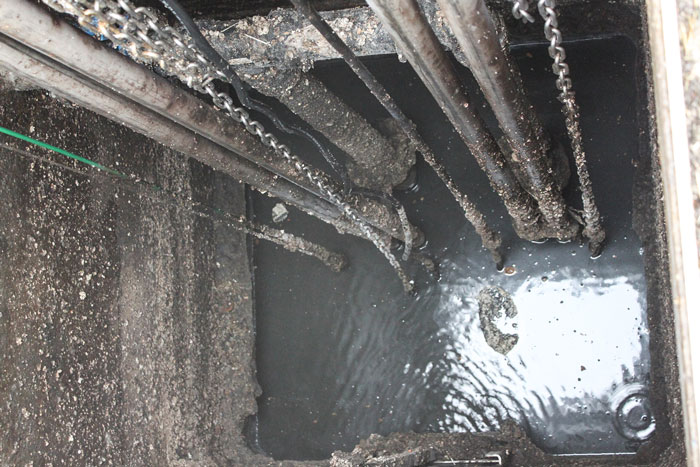
- energy minimizer
- sump
- pipe cleaning functions
- other functions
Intelligent Pumping Systems
Among the intelligent pumping system’s hardware components we can highlight:- integrated control electronics
- new generation nonclog self-cleaning hydraulics
- IE4-rated motor efficiency.
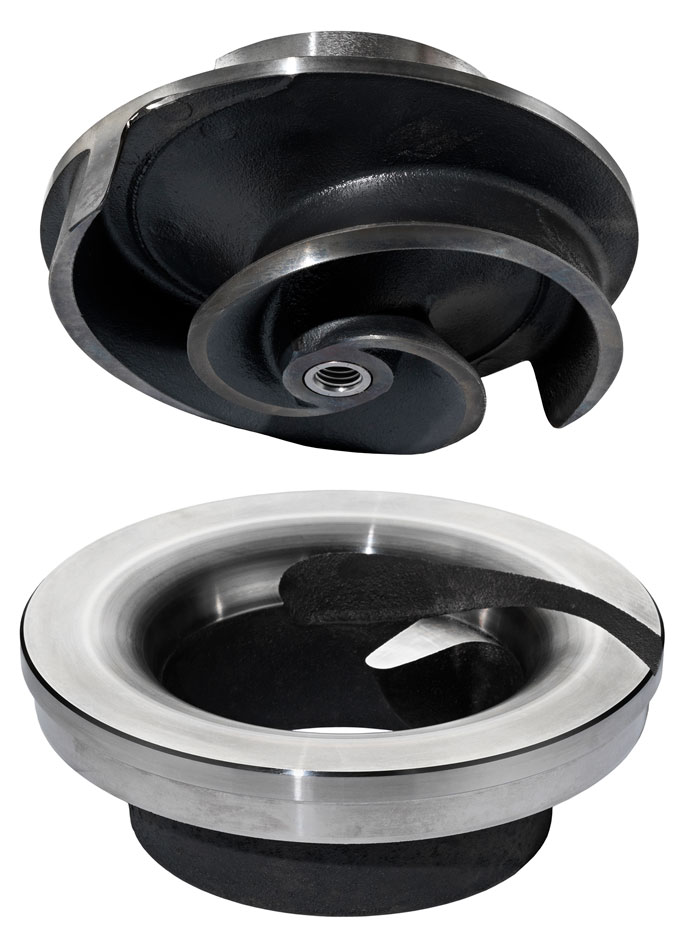
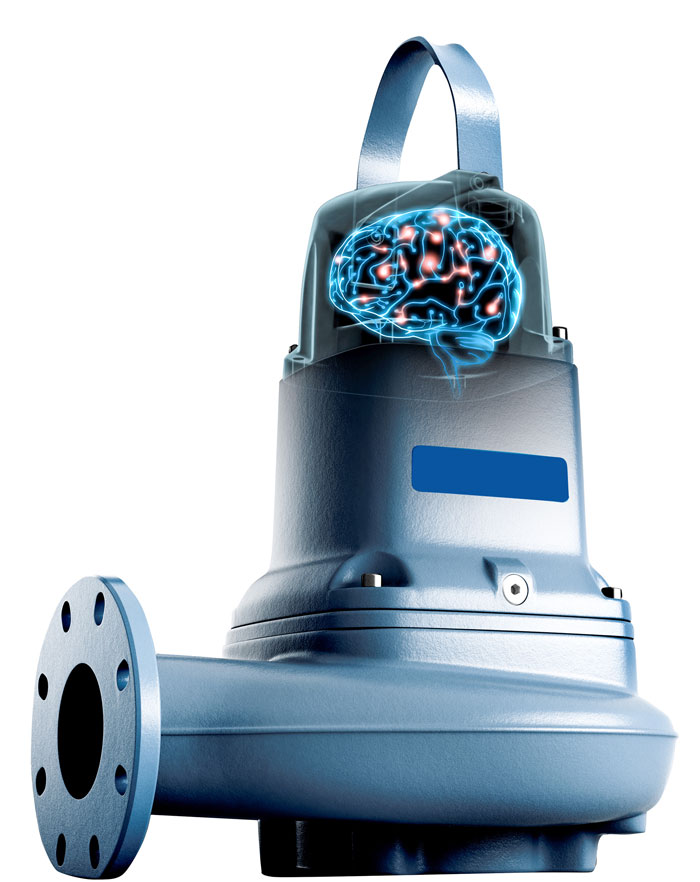
- precise process control
- reduced risk of clogging
- clean and odor-free pump sumps
- substantial reductions in energy consumption
- reduced asset management
- comprehensive data reporting