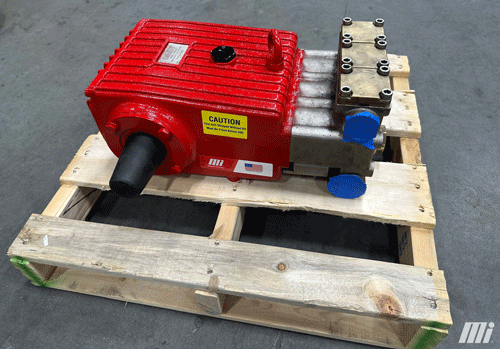
In almost all oil and gas drilling, along with utility line drilling operations, a plunger, triplex or mud pump must be used. These three terms are synonymous with a crankshaft-driven, multiple-piston pump design capable of high volumes and pressures. The pump’s main goal is to provide lubrication and cooling for the drill bit, pressure control of the well and removal of waste drilling material from the hole. The drilling process conditions constantly change during operation, including depth, ground hardness, mud quality, drilling direction, etc. The mud pressure required reflects changes in all these parameters.
With all these variables, it is essential to control the mud pressure and flow quickly and accurately. The most common mud pump power sources are mechanical gearboxes, chain transmissions with a diesel engine or an electric motor as the prime mover. The mechanical transmission design makes controlling the mud pressure and flow more difficult, as the drilling operator must continuously adjust the pressure by changing the flow accordingly. This task is done by either re-switching the transmission speed, dropping in additional mud pumps or adjusting the pumping flow power with other means.
Mud Pump Designs
The most prevalent mud pumps are 3-piston plunger pumps with a typical crankshaft. Most of these pumps have a built-in mechanical transmission ratio of 3:1 or 5:1. The high-speed input shaft is then driven by a diesel engine or electric motor via some speed shift design. The crankshaft’s maximum speed varies depending on the design and size, but a common value at full power is approximately 100 to 150 rotations per minute (rpm) for mud pumps and up to 400 rpm for cement pumps. The normal operational speed is less, and the average speed of 50 to 150 rpm is the most common. Shifting the gear transmission or the diesel engine speed provides the means for flow control. The challenge is to keep steady pressure in the well, which depends on different flow demands.
Horsepower (hp) is horsepower, speed is speed and torque is torque. No magic or secret sauce gives one drive system a huge advantage over the other. One of the many options is a hydraulic drive system.
Plunger pump drive requirements
- high power, 150 to 2,000 hp
- variable speed, 100 to 400 rpm
- high start torque
- exposure to changing environmental conditions
- Hydraulic drive system pros
- direct shaft mount of drive motor—no mechanical connection required
- easily achievable variable speed by varying the motor input flow
- efficient starting torque capabilities
- high-power capabilities
- dual motor drive on common input shaft = natural load sharing
- central pump system to feed multiple drive motors
- ability to stall drive without damage
- space savings
- constant pressure maintainable at lower mud flows
- easy handling of high stop/start loads
- simple-to-provide freewheel of pump crankshaft
Hydraulic drive system cons
- possibly higher initial cost—overall life cost must be considered
- potential oil leakage/spills
- lack of hydraulic system knowledge by some end users
- less efficiency with higher-speed drives
Typically, the initial cost of the hydraulic drive system is the biggest consideration when deciding which plunger pump drive to install. It is important to understand each drive’s advantages and disadvantages and the control type required in the pump application.
2 Types of Hydraulic Drives to Consider
Open-loop, variable-volume
This system design consists of a variable-volume, pressure-compensated pump driven by a prime mover with traditional control valving, such as inline electro-proportional control valves for motor speed and direction control. Additional pump controllers, such as load sense and hp limiting, are available to adjust pump flow output based on changes in the system downstream. These types of controls can all add up to a more responsive and efficient system. This type of system design would also include overpressure regulation for maximum torque control and stalling capability, pressure and flow sensors, along with typical fluid conditioning components for filtration and cooling. When the motor is not driving, the variable pump de-strokes and will sit at pressure standby, waiting for a pressure drop in the system to come back on to stroke. Oil turnover in the system is directly related to the pump’s output flow.
A typical reservoir design would require a 3:1 ratio of oil flow to oil storage. This type of system can be controlled via a programmable logic controller (PLC) that can monitor speed and pressure, allowing system control on the fly. This system design is efficient and most often better understood by maintenance workers.
Closed-loop, hydrostatic
This system design is another method of hydraulic drive that offers distinct advantages over the open-loop design and provides higher efficiency. In the closed-loop design, motor speed and direction are controlled by a variable-volume, bi-axis pump driven by a prime mover. Pressure control valves can all be part of the pump assembly and do not have to be installed inline. The motor is in a closed loop, with the pump outlets with the oil volume used to acquire the given motor speed returning to the other side of the pump. The primary pump is supercharged by a small, fixed displacement pump that charges the loop with flow used in the pump control circuit, and makes up flow for leakage within the pump and motor, thus filling the loop.
Oil turnover in the system is directly related to only the charge pump’s output flow, not the main loop flow. This factor allows for a much smaller reservoir size than a traditional open system. Proportional, electronic stroke pump control provides variable output flow to the motor, changing the speed as required by the plunger pump. A simple PLC can also be used in this type of system to control output speeds and pressures of the plunger pump. It is common that the closed-loop system is not as widely understood by maintenance workers, often requiring additional training for proper troubleshooting and maintenance.
System Controls & Sensors
Both systems described can use sensors and controls to easily automate the system, controlling the plunger pump’s demand for flow. Using motor speed, tachometer feedback is common to close the speed control loop allowing simple potentiometer control by an operator or a more complex control (PID Loop) with a PLC programmed to monitor and control the plunger pump output flow based on input rpm. System pressure sensors can destroke or stop the pump at a given load pressure if required by the application. In addition, maintenance-related sensors can be added to help determine when system maintenance is required. These sensor types include oil filter element condition, reservoir oil level, oil cleanliness monitoring, oil water content, etc. Such system controls can be presented in a user-friendly format via touchscreens and operational dashboards.
Although not all rotating applications should consist of a hydraulic drive, this drive type can be the most effective and efficient solution in many cases. Specific to plunger pumps, hydraulic drive designs are unfortunately not considered enough as a viable alternative. When selecting a design drive to use in a plunger pump operation, the features and benefits provided by a hydraulic drive can be the best choice for overall pump performance, efficiency and control. The closed-loop, hydrostatic drive system is most often the best design choice to achieve the performance required from a plunger pump.