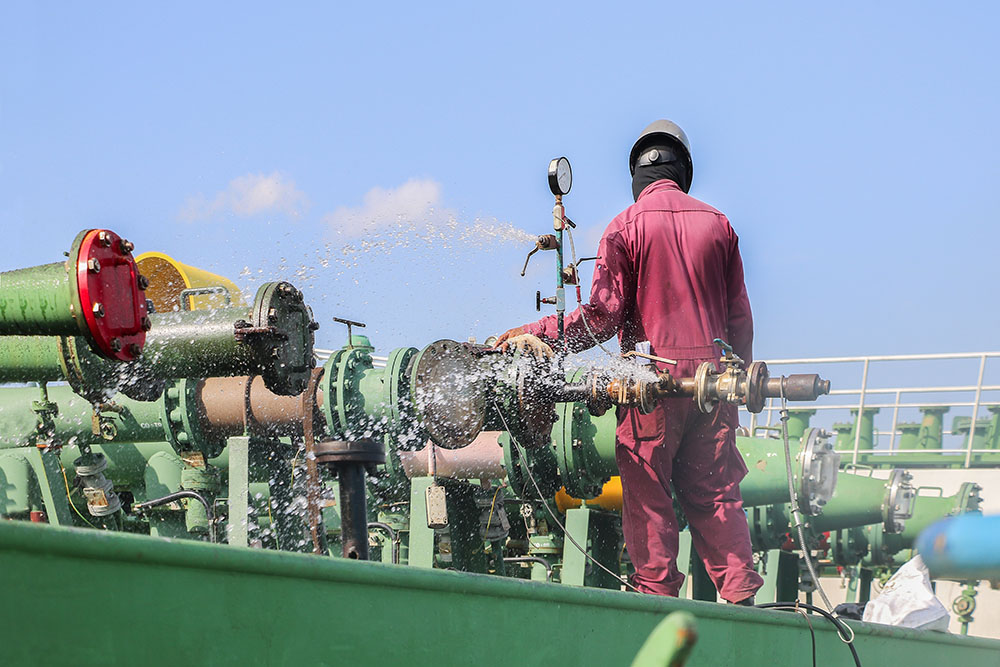
Piping systems consist of many subcomponents, each responsible for specific tasks, that work together to transport fluids for various processes. Expansion joints are one such component. They are critical in the compensation of thermal movement and vibration in piping and are subject to the same testing criteria illustrated in standard piping codes. The probability of a leak in bolted piping connections is a threat to safety and reliability, making hydrostatic leak testing an essential step prior to production startup.
Hydrostatic testing is the practice of using pressurized water to assess the piping system for leaks and adequate strength. Whether scheduled maintenance to replace worn components or the construction of new pipe runs, the final step before bringing production online would be to perform the hydrostatic pressure test.
Successful completion of the test demonstrates that the piping is free of leaks and irregularities, an affirmation that the a shutdown period will not have to be extended to make corrections. There are industry standard codes available that offer guidance on test parameters to help ensure repeated testing success.
ASME Codes
ASME B31 is a pressure piping code in which the standards are split into sections for various types and uses. The American Society of Mechanical Engineers (ASME) publishes sections B31.1 (Power Piping) and B31.3 (Process Piping), which reference hydrostatic testing in piping systems that also use expansion joints. The parameters state the system should be pressurized to 150% of the system design pressure and held for a minimum of 10 minutes, using water as the test media. During this time, inspections are conducted to check for leaks at bolted connections as well as other areas deemed vulnerable by the equipment owners.
Expansion joints are described in the code as either restrained or unrestrained. The difference between the two lies in whether the joint incorporates control rods that will contain the thrust load forces when the system is pressurized. If unrestrained, there are no control rods, so the pressure thrust must be accounted for in other ways during the test to prevent damage to the pipe anchors and equipment. If restrained, the control rods installed as part of the assembly will contain the additional thrust force at the 150% pressure rating.
The Process Piping code (ASME B31.3) covers systems found in petroleum refineries or chemical, pharmaceutical, textile or paper plants as well as others. Pipe runs where unrestrained expansion joints are used must have pipe anchors that are sized appropriately to withstand thrust forces at the hydrostatic test pressure, defined as a minimum of 150% of the design rating of the pipe system. Furthermore, restrained expansion joints must be incorporated with control rods sized appropriately by the manufacturer to contain the pressure thrust at the minimum hydrostatic test pressure. If the equipment owner decides to run the test at a pressure exceeding 150% of the design, it is allowable to omit the expansion joint from the test completely or use temporary restraints to contain the pressure thrust during the test. The temporary restraints should be removed upon completion.
The Power Piping code (ASME B31.1) is limited to electric power generating stations. Hydrostatic test pressure is outlined as no less than 150% of the design pressure of the system. Once the minimum test duration of 10 minutes is met, the system pressure can be lowered to the design pressure and held for any duration necessary to perform examinations for leakage on all joints and connections. For unrestrained expansion joints specifically, it is allowable to employ temporary restraints to contain the pressure thrust during the test to protect the piping and anchors from damage. If temporary restraints are not feasible, the expansion joint may also be isolated from the test using blanks to avoid the pressure thrust altogether. When expansion joints are omitted from pipe system leak testing, the equipment owner has the option to have the expansion joint tested separately at the manufacturer’s facility before being received for installation.
Manufacturer Shop Testing
ASME B31.3 grants self-restrained expansion joints allowance to be excluded from the system leak test when they have been previously tested by the manufacturer. Most manufacturers offer hydrostatic testing of the expansion joint prior to shipment to help with adherence to these guidelines.
The procedure for shop testing aligns with ASME B31 piping codes, where a standard hydrostatic test is performed at 150% of the rated pressure for a minimum of 10 minutes.
Having an expansion joint hydro-tested at the factory prior to shipment adds a layer of assurance that the component has been bolted and has demonstrated pressure retention without leaks before being received for installation. The option to have the expansion joint tested at negative pressure is also available.
During a negative pressure test, vacuum is pulled up to 26 inches of mercury (Hg) for 10 minutes to ensure suction forces will not pull apart the layers of the joint’s construction. Procedures for hydrostatic and vacuum shop testing have been published by the Fluid Sealing Association (FSA) as definitive protocol between all manufacturers. This procedure is available to anyone as reference, identified by standard FSA-PSJ-701-06.
In summary, performing hydrostatic leak testing is a fundamental method for ensuring safety and reliability in piping systems for all industries. Codes provided by ASME are helpful to understand what is and is not allowable for expansion joints during a leak test. Being familiar with these requirements has advantages in the critical time schedule that is required to resume production after maintenance shutdown periods.
References
1. FSA-PSJ-701-06 Piping Systems Non-Metallic Expansion Joint Hydrotesting and Vacuum Testing. Fluid Sealing Association (2006)
2. ASME Code for Pressure Piping – B31.1 Power Piping. American Society of Mechanical Engineers (2014)
3. ASME Code for Pressure Piping – B31.3 Process Piping. American Society of Mechanical Engineers (2012)
We invite your suggestions for article topics as well as questions on sealing issues so we can better respond to the needs of the industry. Please direct your suggestions and questions to sealingsensequestions@fluidsealing.com.
Read more FSA Sealing Sense articles here.