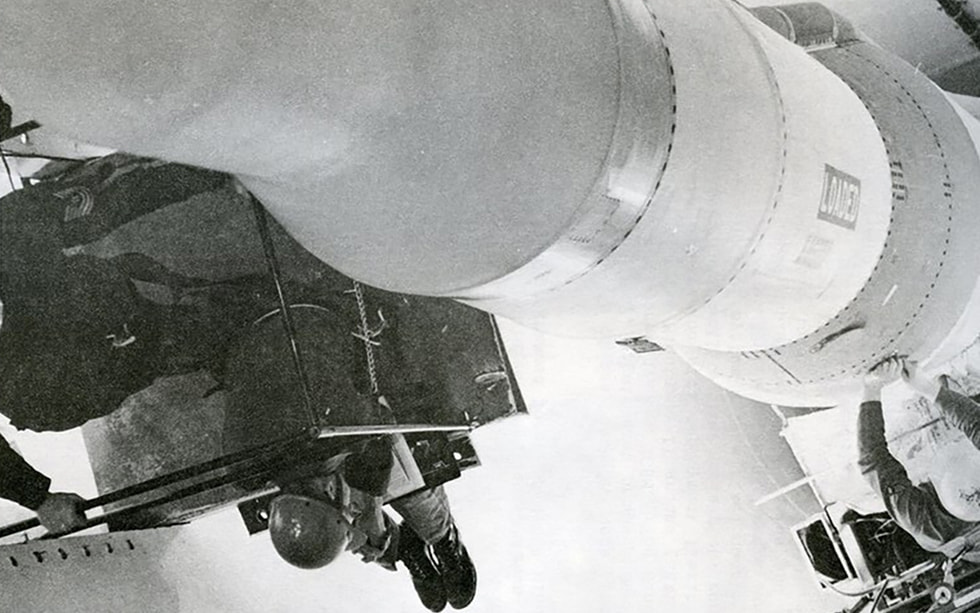
On Dec. 5, 1964, Bob Hicks had a crucial task in a remote part of South Dakota. He had to descend into a Minuteman I missile silo to disarm the missile and retrieve its warhead. At the time, Hicks was a missile maintainer stationed at Ellsworth Air Force Base. Late at night, he received a phone call from his crew chief, who informed him about an accident that occurred at one of the intercontinental ballistic missile (ICBM) silos. According to released documents cited by the Rapid City Journal, the warhead was no longer on top of the missile.
The accident happened when two other airmen were carrying out routine maintenance on a missile. Their improper use of a screwdriver to remove a fuse caused an explosion in one of the missile’s retrorockets. As a result, the missile’s cone, which houses the nuclear warhead, was damaged and fell to the floor of the silo. The two maintainers escaped unharmed.
Inside a metal cage that was lowered into the silo through cables attached to the walls, Hicks worked diligently. He used a metal rod to disconnect the electrical connections between the different stages of the missile, rendering it incapable of being fired. Additionally, he came up with the idea of using a cargo net to recover the damaged cone and lift it out of the silo.
After several days of practicing the procedure in another silo, Hicks successfully executed his cargo net method. It took two hours to raise the cone out of the silo, and then it was carefully placed on mattresses inside a trailer truck. The cone was transported to Lackland Air Force Base in San Antonio for disassembly.
An Air Force report indicated the accident cost approximately $1.85 million in today’s dollars and was attributed to personnel error. In March 1965, the base newspaper discreetly recognized Hicks as the “maintenance man of the month for his division,” without mentioning the accident. Shortly after, he received an Air Force Commendation Medal in recognition of his brave actions.
It is not uncommon to see people use the wrong tools regarding gasket installation. For example, using a screwdriver to remove a gasket from a flange can cause damage to the flange face profile, resulting in leak paths the gasket cannot seal against. Another example is someone putting anti-seize on a gasket because they thought it would make it easier to remove but never thinking about how it would result in a leak path created when the lubricants dry. Also, there are situations where the wrong gasket has been selected because, just like using a screwdriver to remove a fuse, it was easier than looking up the right material for the service (STAMP: S-gasket size, T-temperature, A-application, M-media, P-pressure).
Another example of being prepared has to do with the actual bolting components of the flanged assembly. The USS Iwo Jima had incorrect bolting material that caused a massive failure in a steam valve that resulted in 10 servicemen losing their life.
Complacency is still important some 50 odd years since the accident in South Dakota that Bob Hicks fixed. On Sunday, Nov. 25, 2018 (Thanksgiving weekend), ethylene oxide (EO) was accidentally released into the air from an EO plant in Delaware. The Delaware Memorial Bridge was closed for five hours as a precautionary measure because of the potentially hazardous nature of EO, which is flammable and toxic. No injuries to plant personnel, responders or nearby residents were reported. Investigations by the company and the state determined the release was caused by a failed flange gasket on the water reboiler piping servicing the purification column. The gasket used was of a material not suitable for the operation.
In many cases, when leaks occur at a flange joint, the common assumption is that it is due to a gasket failure. However, the gasket divisions of both the Fluid Sealing Association and the European Sealing Association (ESA), which include many gasket material manufacturers worldwide, have reported a significant portion of these reported gasket failures are actually caused by poorly designed, installed and assembled bolted flange joint assemblies (BFJAs).
Despite the considerable effort and time invested in designing a BFJA that effectively contains the intended substances at the correct pressure and temperature, the industry has observed less than satisfactory results in achieving leak-free conditions. In recent years, there has been increased awareness within the industry regarding emissions leakage, prompting a focused effort on enhancing assembly and installation practices. Improving these practices is seen as a crucial step in guiding end users toward creating environments that are free from leaks.
When designing a bolted joint there are many factors to consider, but two of the most crucial for creating a leak-free BFJA are selecting the right gasket and installing it properly. Unfortunately, the importance of skill and knowledge required for installation is often overlooked. A significant amount of both are necessary to understand the conditions and procedures needed to achieve a reliable and leak-free bolted joint.
The Fluid Sealing Association and ESA recognizes PCC-1 (Guidelines for Pressure Boundary Bolted Flange Joint Assembly) as the industry guideline in the Americas and EN 1591-4 (Flanges and their joints - Qualification of personnel competency in the assembly of the bolted connections of critical service pressurized systems) in Europe for installation of gaskets. These documents represent generally accepted good practices that can be used in conjunction with existing codes. The guidelines outlined in PCC-1 cover the assembly elements essential for a high level of leak-tightness integrity of otherwise properly designed/constructed BFJAs.
Lifelong learning and training is critical for maintenance workers, engineers and planners. Making sure the training provides the latest methods and techniques can lower the risk of an accident. The Fluid Sealing Association and its members can also assist with training aids (Compression Packing Technical Manual/Gasket Handbook/KnowledgeBase) and training to lower the risk of potential gaps in workforce knowledge. The Fluid Sealing Association has created a guide on flange sealing installation that reviews both the American Society of Mechanical Engineers (ASME) and International Organization for Standardization (ISO) recommendations in one place.
We invite your suggestions for article topics as well as questions on sealing issues so we can better respond to the needs of the industry. Please direct your suggestions and questions to sealingsensequestions@fluidsealing.com.