Would you run your automobile engine without oil? Assembling a bolted joint without using a proper thread lubricant is a comparable scenario. Thread lubricants are often overlooked but can have a huge impact on the success of a bolted joint. In any industrial plant, there can be thousands of bolted connections, primarily in the flanged connections throughout piping systems, on packed stuffing boxes on pumps and valves, and on heat exchanger covers, for example. All of these pieces of equipment are used to join components while maintaining a leak tight pressure boundary for a system. These systems can operate under high pressures, high temperatures and in dangerous chemicals, and a failure of a bolted joint can lead to an extreme hazard for personnel.
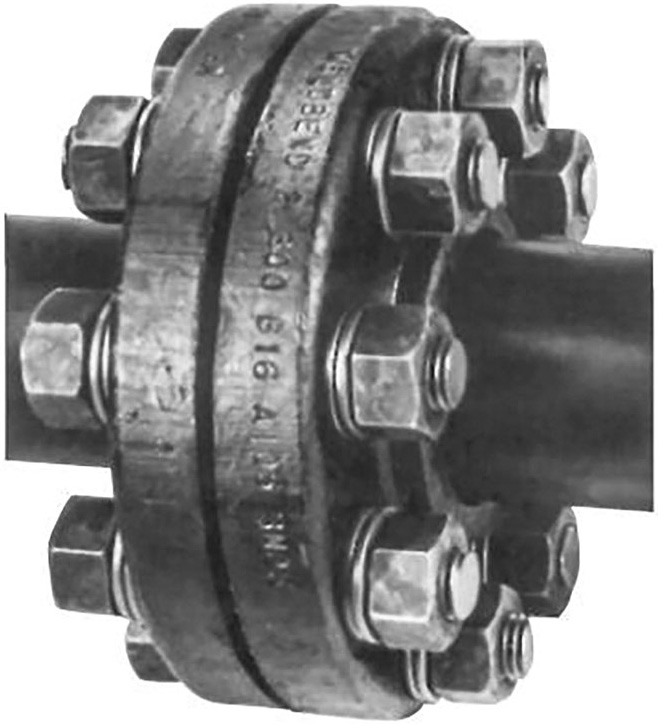
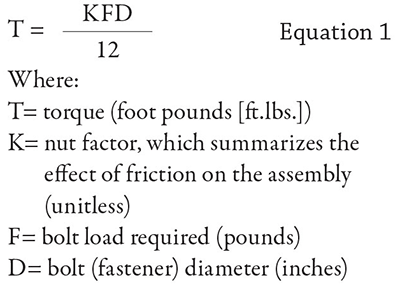
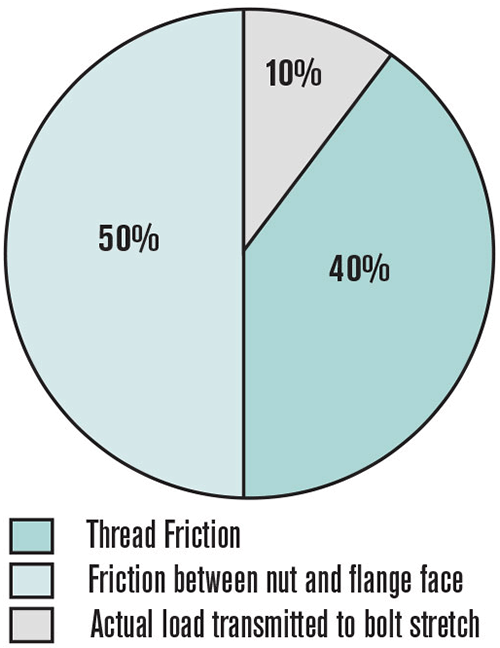
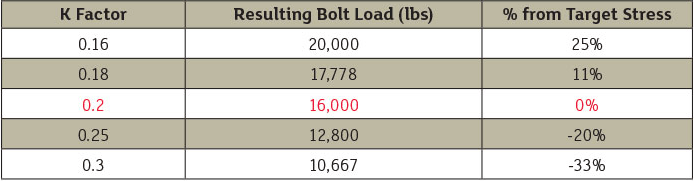
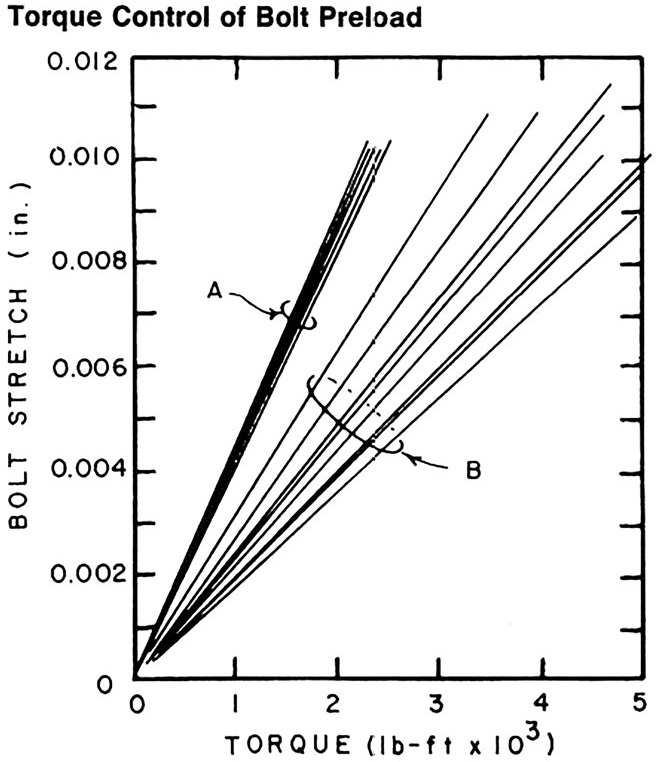