Discover options for small internal surfaces to extend life.
Praxair Surface Technologies
04/30/2019
As oil and gas exploration and production moves to deeper and more remote places, components are exposed to harsher environments leading to wear from abrasion, corrosion, erosion and high temperatures. Operators are looking for technology that will extend the life and improve the reliability of critical components experiencing inner diameter wear.
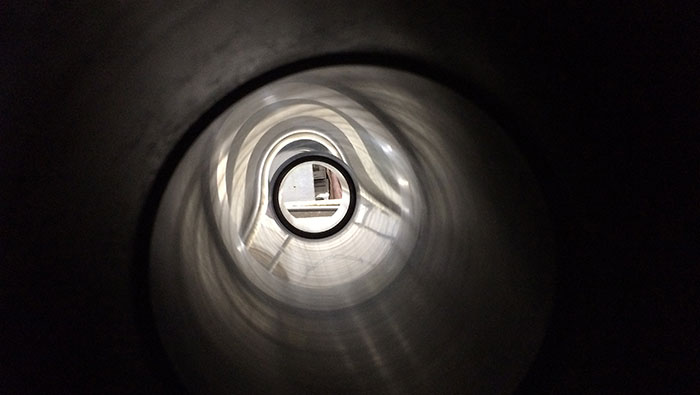
Protecting Critical Components
Thermal spray carbide-based dense coatings provide effective protection against aggressive wear. Thermal spray is a line- of-sight process—in other words, it is used to apply various coating powder feedstocks on (most commonly) external surfaces with a close to nominal spray angle. There are a variety of thermal spray solutions in the industry, and one of the most common solutions is high velocity oxygen fuel (HVOF). HVOF uses an internal combustion system to generate a supersonic flame jet for heating and accelerating powders to form a coating on the component. Either liquid or gaseous-based fuel is used in the HVOF process. Carefully metered oxygen and fuel are introduced into the combustion chamber where a spark ignites the mixture and continuous combustion occurs. The resulting high-pressure hot gas can expand through converging-diverging orifices and accelerated to supersonic speed in the nozzle. A carefully measured flow of fine powder is injected into the nozzle. The powder is heated and accelerated by the products of combustion, usually to temperatures close to or above its melting point and to velocities approaching or exceeding 1,800 feet/second (550 meters/second). The resultant coatings have a typical coating thickness range from 0.002 to 0.020 inches (50 to 500 micrometers).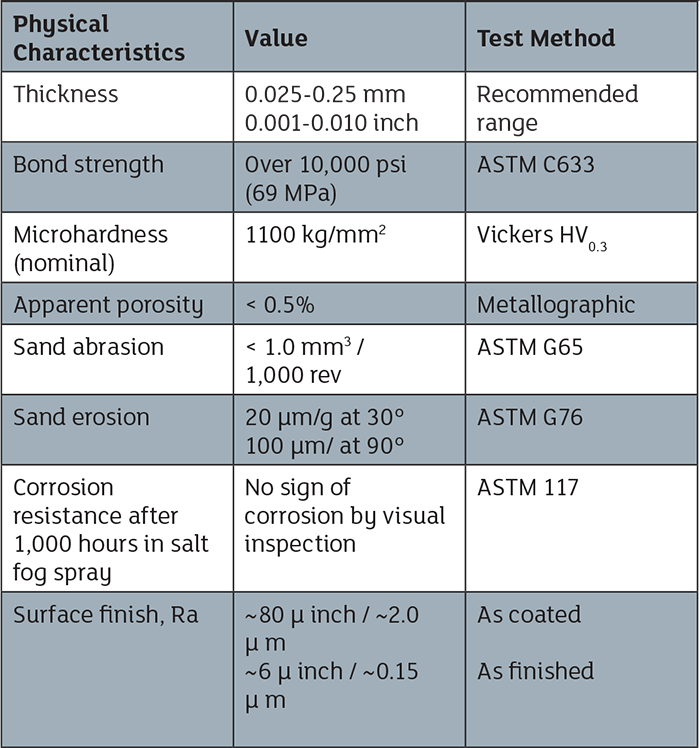
Developing Coatings for Small Inner Diameters
It is difficult to coat within the small diameter of internal surfaces such as cylinders, flow tubes, housings, valve bodies, sleeves and tubes. Powder particles must be heated and accelerated over a small spray distance, in milliseconds, in order to produce and adhere the dense, carbide coating on the substrate. A few varieties of thermal spray inner diameter (ID) solutions have been developed, such as a solution that creates a dense coating on the surface of internal diameters in tight spaces. The internal diameters can be as small as 2.8 inches, or 71 millimeters (mm). Significant effort has been used to overcome the difficulties in spraying internal surfaces in a confined space. While the application process is similar to standard HVOF systems, the process must occur within a much smaller space. The minimum distance from the torch to the surface is approximately 1.0 inch (25 mm). As part of adapting to the shorter spray distance, finer powder must be used. This allows the powder to be properly processed and result with a coating strongly adhered to the substrate. Another concern when coating in a confined space is heat. Special equipment must be used to ensure the substrate temperature is controlled. To ensure the mechanical properties of the substrate are not affected by the coating process heat, the component temperature is controlled so the temperature never exceeds 250 F (120 C). In this manner, the properties of the substrate are not affected by the heat, and there is no distortion to the part. Special attention must also be paid to the design of engineering components used to handle the part during coating (tooling). Tooling must address different geometries of the part including ridges, holes, bends and other areas that change along the component’s length. Part of the tooling design includes masking to ensure that the coating is not applied to areas that should not be coated. Because every part is different, the coating cannot always be applied in the same way. Coating composition, position of the torch and design of the tooling must all be customized for each application. Design of the component should be reviewed with coating application engineers to find the best solution.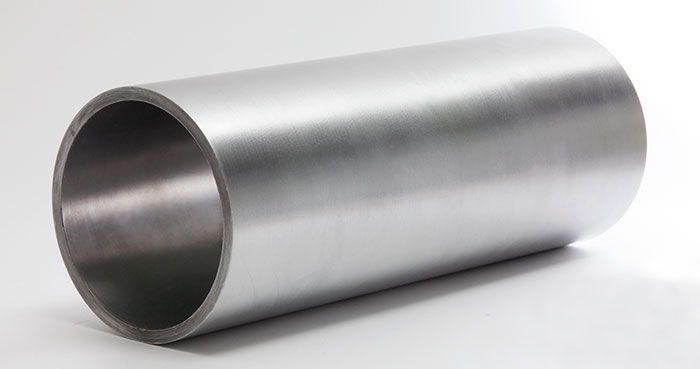