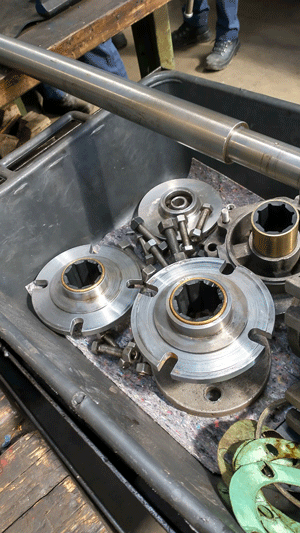
A refinery in Genoa, Italy, produces diesel fuel, bitumen and fuel oils with a low sulfur content for use in a wide range of applications, including vehicles, ships and domestic heating products. Having operated reliably since 1931 and certified to International Organization for Standardization (ISO) standards, the refinery prioritizes the quality of its operations and the maintenance of its equipment.
In May 2021, a representative for a graphite company visited the refinery’s internal maintenance and repair shop. There, he met with the refinery’s machineries department manager. During this visit, the representative learned about an issue the maintenance team was working to address.
One of the refinery’s vertical pumps in water-oil service had experienced repeated bearing failures. The original bearings on this vertical pump, which ran at 2,980 rotations per minute (rpm), were water-lubricated metal and rubber bearings, which needed to be continuously immersed in fluid.
The vertical pump had experienced numerous bushing failures, and its service is water in ambient operating temperature. Due to intermittent failure of the level control system, the pump would run dry for extended periods of time, leading to deterioration of the bearings. When these types of bearings run dry for more than a few seconds, especially at startup, they get damaged and need to be replaced. This is a drain on the maintenance team’s time, attention and budget.
While viewing the disassembled pump, the representative explained some of the key features and capabilities of graphite-metal alloy materials, which could help solve the dry run issues, prevent bearing failures and ensure the pump would work efficiently and reliably.
Graphite-metal alloy bushings combine the self-lubrication of graphite with the strength of metal. This nongalling material is suited for bearings and bushings in refinery and petrochemical pumping applications where dry-run or low lubricity scenarios are common. Graphite-metal alloy bushings enable pumps to run dry and survive upset conditions. Pumps can be restarted and continue operating without loss of performance or the need to replace the bushings.
In addition, due to the materials nongalling features, running clearances can be reduced for efficiency gains.
The representative and refinery manager launched a thorough review of the graphite-metal alloy materials.
The maintenance manager’s goals were to repair the vertical pump to ensure it would operate efficiently and reliably, while increasing the mean time between repair (MTBR). Extending the MTBR translates to long-term cost savings.
After 60 days of thorough review and planning, the representative and manager made the decision to order graphite-metal alloy line shaft and throat bushings for the vertical pump.
The new bushings were installed during a scheduled repair in September 2021. The pump bushings have now been operating for over a year without any issues.
Due to this success, the refinery team is now interested in upgrading their bushings and case wear rings, using the graphite-metal materials for their amine recirculation pumps in service.