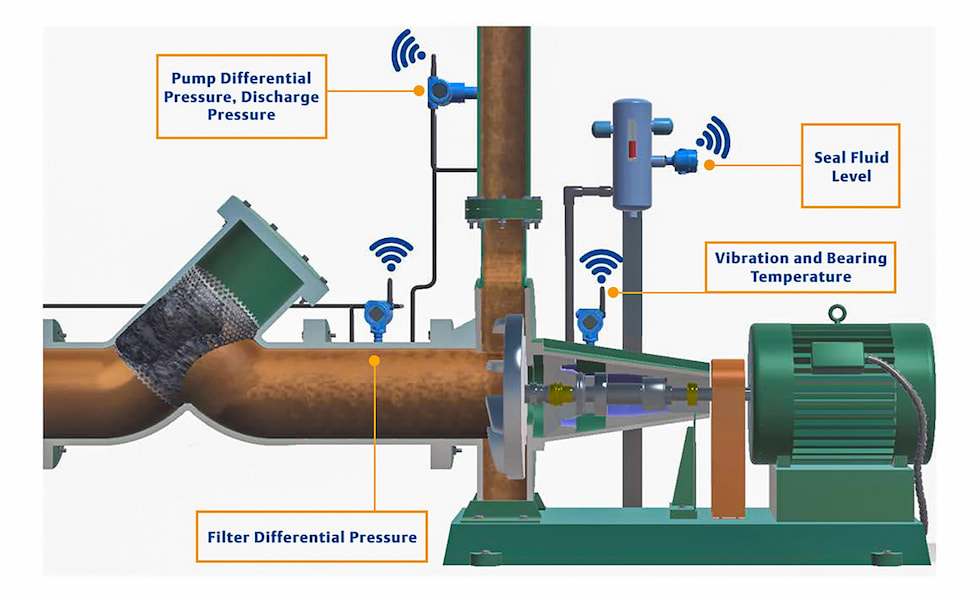
Power plants rely on pumps. This has not changed even though the power industry itself has undergone many changes in the past decade. Each of those pumps—whether they are lube oil pumps, water pumps or ammonia pumps—needs to be monitored or at least checked regularly to ensure safe and reliable operation.
However, checking on pump health has historically been a manual process where someone must travel to the pump and manually check levels, vibration, temperature, test operations and inspect it for possible hydrocarbon leaks. This time-consuming and potentially hazardous task is often performed on a rotating schedule, which means insight into pump health is not up to date, and maintenance is more likely to be reactive once a problem causes a process interruption.
If an operator is only able to check on a pump once a month, that means data on the pump’s health can be up to a month old, and the risk of missing a potential problem in the early stages is likely. Add to that the trends in the industry of a reduced workforce and it becomes a reliable tool to track pump health. To understand how an integrated pump health monitoring system can reduce the need for manual records while improving accuracy and reliability, the typical issues that cause pump problems must be considered.
Understanding the Problems
The lube pump, as the name implies, ensures that adequate lubrication is sent through a system to ensure all equipment is lubricated within acceptable standards and there is no chafing of metal that can cause damage. However, measuring the lube oil levels can be difficult if the pump is in the elements. The site glass or visual indicator that shows lubrication oil levels can become varnished, making it harder to get accurate lubricant levels. Additionally, a leak in the lube oil reservoir or hoses could result in a rapid loss in lubrication that may occur between manual inspections.
Water pumps can be part of cooling towers in steam operations. These pumps are critical in returning cooled water to the steam system to be reheated into steam. If anything causes the pump to malfunction or leak, it creates problems throughout the process.
Ammonia pumps are used in combined-cycle power plants, where ammonia is injected into the heat recovery steam generator through the selective catalytic reduction process. These pumps play a critical role in the reduction of nitrous oxides emissions into the atmosphere.
The two main fault conditions recorded on pumps have been vibration and hydrocarbon leaks. In many cases, over time, hydrocarbons can leak from the pump, causing it to run without proper lubrication, which ultimately leads to vibration issues and potential damage. Any pump subject to vibration—either from internal motor issues, bearing damage, speed of fluid flow or other equipment attached to it—can experience failure due to that vibration. This can occur in regular operations or due to a malfunction and can often lead to a plant outage. What makes continuous pump monitoring compelling is the value of enabling a user or technician to be upskilled. Instead of recording the problem manually and relying on operator experience to identify issues, continuous monitoring provides the pump health data and runs continuous analytics. Personnel can now focus on running the process and responding to problems before they result in an outage, thus increasing pump health, operator productivity and plant reliability.
Challenges of manual pump rounds are compounded if the location of a pump is hard to reach, inclement weather occurs, or rounds are not completed because an issue was found with a pump and the user is diverted from completing the rounds. This makes the job more challenging and problems are more likely to go undetected until they cause process upsets.
Going From Problem to Solution
The impact from a failure can be significant but some options will dramatically mitigate risk. One option is a continuous pump health monitoring system that enables users to detect and predict problems based on accurate, real-time data collected from the pump and sent wirelessly to the operator’s device. Alerts from the continuous monitoring system can be integrated into a computerized maintenance management system (CMMS) to drive automatic work orders.
Continuous monitoring allows for greater visibility into process and equipment conditions. The question is, how does a facility make that happen without an investment in new equipment, cabling and other infrastructure items, as well as training on how to work this new setup? The answer is found in wireless sensor networking technology and existing sensors, which feed all of that data into a continuous monitoring software package. Wireless sensors allow for a cost-effective multimeasurement approach:
- Using existing infrastructure provides value from the wired data being collected.
- Predictive analytics ensure problems are caught before they lead to process upsets.
Wireless sensor networking technology makes it possible to build a wireless network within a facility without the cost of additional wiring. Devices that measure such things as acoustic interference, vibration, pressure and temperature, and level metering are available with native wireless sensor networking technology connectivity supporting smart transmitter capabilities without the need for power or networking cabling.
Data Becomes the Predictor of Pump Health
Having a continuous monitoring solution to monitor pump health also means more data is generated. Knowing how to use that data without additional time-intensive training or resources becomes key. Selecting a company that provides not only the wireless-enabled sensors and transmitters but also the software that collects the data and presents it in an easy-to-read format on a dashboard will make the upgrades and adoption of the technology more successful.
When properly presented, the collected data will provide actionable information on each pump connected to the system and give insight into process efficiency. The data allows for predictive maintenance and process optimization where applicable. With the right, real-time data, it is possible to know when an oil pump is running sluggishly or is too low on seal oil. It is possible to instantly see if the water pumps feeding into the steam system are running with high cavitation levels and require maintenance or process changes—or to know when the ammonia pumps are in the beginning of bearing wear due to under lubrication.
All of this can be accomplished through deploying a continuous monitoring solution and without the user needing to walk through the plant to check each pump. This can free up resources and, where pumps are a concern, ensures a more efficient, reliable and safer process.