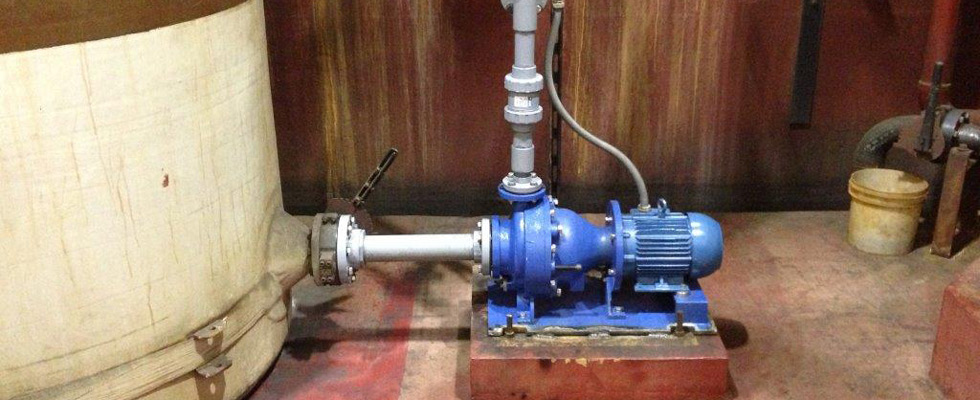
Magnetic drive centrifugal chemical pumps provide proven solutions for many of the most demanding applications. They can enhance safety and improve reliability, while also offering improved productivity and regulatory compliance.
This is, in large part, because where a mechanically sealed centrifugal pump has a direct connection between the motor shaft and the pump impeller, a magnetic drive pump has no physical connection between the motor shaft and the pump impeller.
Magnets mounted on the motor shaft transfer the motor power through a solid barrier (frequently corrosion resistant plastic) to magnets inside the pump that rotate the impeller. This allows the mechanical seal to be eliminated.
Given this structure, magnetic drive centrifugal pumps have many advantages. The most notable is the life cycle cost is generally lower compared to a mechanically sealed pump due to the lower maintenance cost (no seals to replace), ease of instillation (no water/drain lines for seals that require a flush fluid) and increased productivity (less downtime). Other advantages include:
- Eliminates release of corrosive fluids due to seal failure
- Increases productivity by eliminating downtime to replace failed seals
- Can run dry without damage depending on the manufacturer and bushing type
- Greater mean time between failure (MTBF) due to lack of bearings or seals
- Easier to install with no need for water/drain lines for seal flushing
- Low life-cycle cost
Industries & Applications
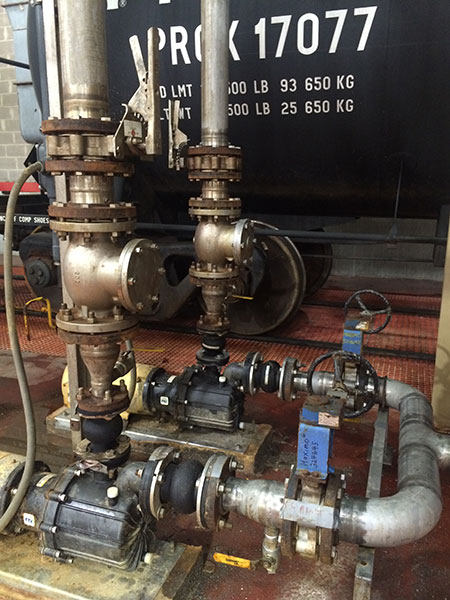
A number of industries benefit from the use of magnetic drive chemical pumps:
Chemical manufacturing
Pumps are used to transfer chemicals from bulk storage into blending tanks and to mix those chemicals in the blending tanks. They are also used to unload chemicals from trucks and railcars and into containers or container filling machines. Additionally, they transfer chemicals from one part of a plant to another through piping.
Battery manufacturing
Lead acid battery manufacturers use magnetic drive pumps to transfer sulfuric acid (93% to 98%, depending on the season) from outdoor bulk storage tanks to indoor blending tanks. Magnetic drive pumps can also transfer deionized water into the blending tank to achieve the proper dilution for battery acid (typically 29% to 32% sulfuric acid).
While the blending tank is being filled, magnetic drive pumps can recirculate the mixture through a heat exchanger. This is critical, as sulfuric acid is extremely exothermic (liberating large quantities of heat) when mixed with water.
Chemical distribution
Chemical distributors transfer a wide variety of chemicals from bulk storage tanks into a variety of containers. These can be pails, drums, totes/intermediate bulk containers (IBCs) and even chemical tractor trailers for large quantities. Magnetic drive pumps are frequently specified due to their reliability and inherent safety since they do not have mechanical seals (which eventually fail, allowing toxic materials to leak and creating environmental and human safety issues).
Water and wastewater treatment
The most common application is to transfer chemicals from bulk storage tanks to day tanks. Large water departments typically receive the sodium hypochlorite (bleach) used to disinfect the treated water in high concentrations (12% and higher) to reduce the transportation costs. However, sodium hypochlorite is unstable at high concentrations, so it is diluted with high-quality water to approximately 5.25%, which is much more stable. Magnetic drive centrifugal pumps are used to recirculate the concentrated bleach and water to ensure it is uniformly diluted.
Other applications include continuous sampling pumps to monitor the treatment process and pumping regeneration chemicals (sodium hydroxide and hydrochloric acid) through ion exchange resin tanks.
Electroplating and anodizing
Magnetic drive pumps are used in a variety of applications. Plating tanks are frequently hot and require mixing to keep the temperature uniform. Magnetic drive pumps are used to provide flow through devices called eductors.
Eductors use the venturi effect to allow more flow by inducing additional plating solution to be pulled into the flow stream created by the pump. This allows up to five gallons for every gallon pumped to be circulated, keeping the tank at a uniform temperature.
Plating tanks also need to be kept free of contaminants like dust and dirt to ensure high-quality finished products free of imperfections from the dust and dirt. Magnetic drive centrifugal pumps provide reliable flow through filters.
Large quantities of wastewater are created from rinsing at various stages. Magnetic drive pumps are used to transfer wastewater and water treatment chemicals in on-site treatment plants.
Steel processing
Magnetic drive centrifugal pumps are used in the manufacture of hot rolled steel, a process in which steel is rolled to a specific thickness at a temperature above its recrystallization temperature, frequently exceeding 1,000 F (538 C). However, the exterior is covered in unusable iron oxide scale. Pickling is an acid bath (most commonly hydrochloric acid) that is heated (frequently 140 F/60 C). The steel is unrolled and passes through a series of baths, including acid and rinsing with water. It is then coated with oil to prevent rusting.
Magnetic drive centrifugal pumps are used to return liquid from the process tanks that overflow into surge tanks (the steel displaces liquid as it enters the tank, similar to a bathtub level rising when a person is in the tub). Self-priming magnetic drive centrifugal pumps are used to transfer rinse water from below grade sumps to on-site processing before reuse or discharge.
Printed circuit board manufacturing
Printed circuit board manufacturing is a precision-based process in which the board has extremely fine circuit details. Magnetic drive pumps are used to provide pressure and flow for etching and rinsing. They also provide high flow rates for flood bars and solution filtration. In solution, vertical magnetic drive pumps have an advantage over open-column vertical pumps. The magnetic drive pumps do not introduce any air (microbubbles) into the solution being pumped, decreasing the number of boards that fail final inspection due to a microbubble causing an open circuit.
Biofuels
Ethanol is used to oxygenate gasoline. This allows the fuel to burn more completely, producing cleaner emissions. In the United States, corn is commonly used in the production of ethanol. Magnetic drive centrifugal pumps are used to transfer enzymes, sodium hydroxide, acids and other corrosive fluids to manufacture fuel-grade ethanol.
Odor control in municipal wastewater treatment plants
Wastewater treatment plants can produce objectionable nuisance odors that may have detrimental effects on property values and individuals living nearby. During the processing of municipal wastewater, organic and inorganic forms of sulfur (such as hydrogen sulfide, which smells like rotten eggs), ammonia and other chemicals can be produced, resulting in objectionable odors.
To treat these odors, the process tanks are enclosed to capture the odors and pass them through wet chemical scrubber systems that use sodium hydroxide and chlorine (bleach) to remove the chemicals responsible for the objectionable odors. Magnetic drive centrifugal pumps are used to provide flow to the spray nozzles inside the wet scrubbers.