Detect failures early and prevent downtime.
UE Systems
10/02/2017
For more than 40 years airborne/structure-borne (AB/SB) ultrasound has evolved from working in single applications, such as leak detection, to electrical surveys and inspecting mechanical or rotating equipment in the maintenance and reliability world across all industries. Ultrasound is a versatile, non-destructive technology with multiple applications that is not limited to any one particular scan, survey or trend.
What is AB/SB Ultrasound?
Essentially, AB/SB ultrasound can be described as non-destructive technology that is listening to the frequency range above human hearing. Normal human hearing is between 20 hertz (Hz) and 20 kilohertz (kHz). Any frequencies above 20 kHz would be classified in the ultrasonic range. AS/SB ultrasound is only listening for sounds created by turbulent flow, ionization or friction. It is different from pulse echo or power ultrasound, which send out a signal and receive it or only send a signal from the end of a transducer. The equipment then reads out in decibels (dB) to indicate how loud the ultrasound is at a particular frequency. Table 1 shows examples of frequencies that have been proven over many years to hold true while monitoring different applications with both analog and digital AB/SB ultrasound.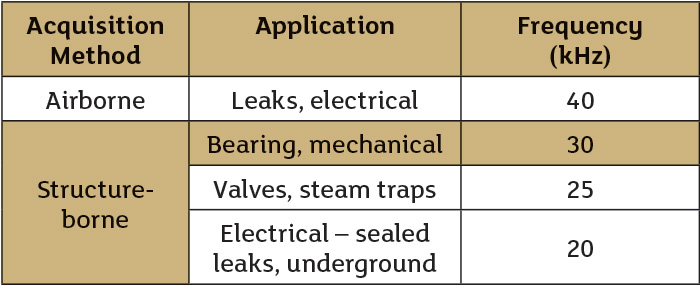
- Relatively inexpensive entry point with quick opportunities for return on investment (ROI)
- Ease of learning curve for all skill levels, from top to bottom with software reporting to gathering data
- Proven track record of trending and reporting to make confident analysis in a condition-based maintenance (CBM)/predictive, preventive, prescriptive maintenance program
- State-of-the-art digital equipment allows for user friendly operation
- Ever-growing remote monitoring applications, perfect for assets that are guarded or shielded for safety reasons, a plus for route-based or continuous-monitoring systems
Monitoring Bearings the Ultrasound Way
Vibration, infrared, motor circuit testing and oil analysis have all been technologies used to monitor bearings. Ultrasound has become a heavy hitter due to its ability to detect faults or subtle changes much sooner than other technologies (see Figure 1).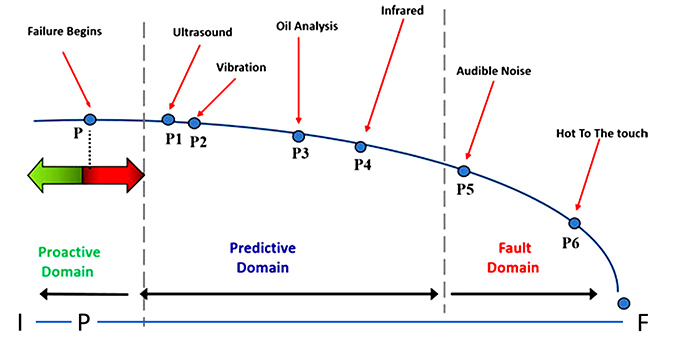
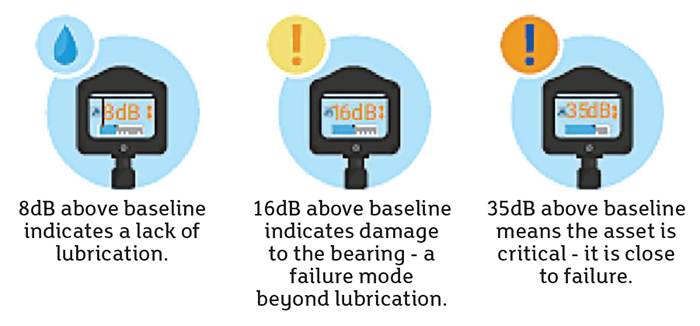
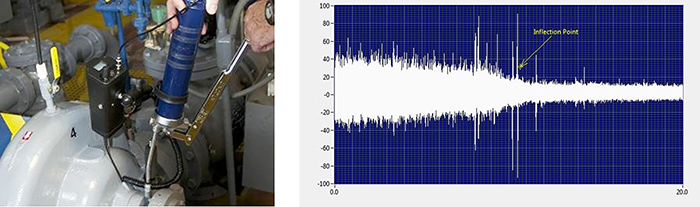
Think Safety, Monitor Remotely
More and more facilities are continuing to engineer safer environments to help prevent near misses—or worse, reportable incidences. With the increase of guarding to prevent workplace injuries, remote monitoring is on the rise. Traditionally, SB ultrasound has been a go-to option due to the mobility of hand-held devices. Remote access sensors (RAS) are becoming more and more affordable to install. These sensors can collect the data via a switch box or continuous monitoring system that can forecast bearing needs or failures. Pump bearings can be inaccessible because they are either out of reach or obstructed by a cage. Possible solutions are a 100-foot cable with an RAS on the end or Wi-Fi sensors. Depending on remote monitoring needs, ultrasound can provide a solution to safely gather data that helps monitor that highly critical asset.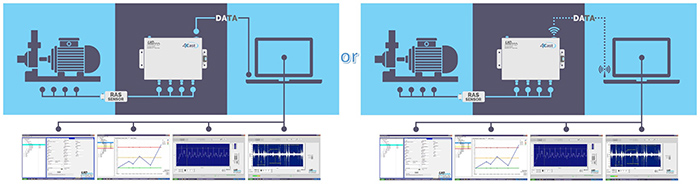