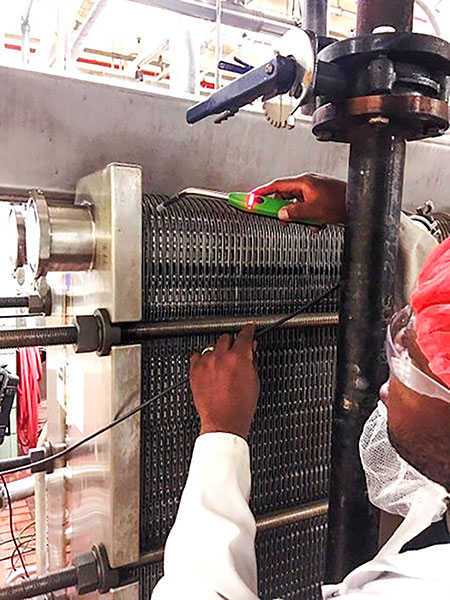
Consumer and product safety is a cornerstone of the food and beverage processing industry. Failure to identify contamination hazards can result in costly recalls, damaged brand reputation, and most importantly, it can put consumers at risk. Proactivity through predictive and preventative maintenance of process-critical equipment, like heat exchangers, is an excellent way to ensure consumer safety and protect brand integrity.
Gasketed plate heat exchangers are widely used in dairy, food and beverage processing applications for heating,
cooling and pasteurization duties. Their compact nature and efficient design make them ideal for demanding heat transfer solutions. Although resilient and flexible, plate heat exchangers require proper maintenance and repair to maintain accurate performance.
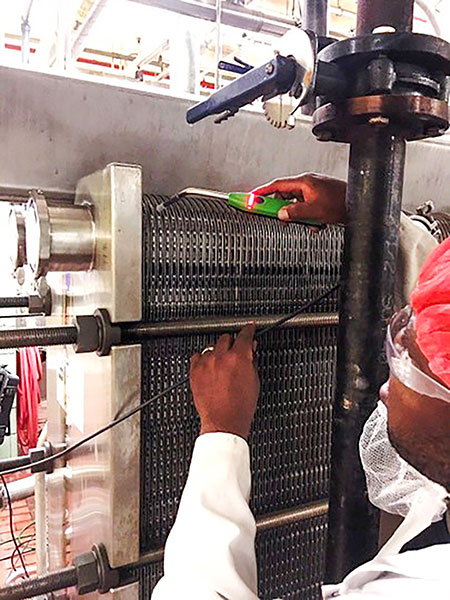
IMAGE 1: A precision sensor is used to detect the discharge of any gas and to signal damage to the plate or gasket. (Images courtesy of Rodem)
Integrity testing of plate heat exchangers allows processors to identify microscopic cracks and material
fatigue before they develop into harmful leaks. This testing method gives processors greater control of their process schedule and maintenance planning with expanded insight and a more detailed understanding of the exact condition of their plates and gaskets.
Why Integrity Testing?
Integrity testing offers an innovative way of providing clear awareness about the equipment’s status, resulting in increased processing safety and effectiveness. By identifying the smallest of emerging flaws, integrity testing empowers processors to address damaged plates and gaskets before breakdowns happen.
A proactive approach
Early detection of gasketed plate heat exchanger leaks gives processors the luxury of thinking ahead. An undetected leak can not only result in unexpected downtime and unscheduled shutdowns, but can cause excessive waste when a product is damaged beyond recovery or lost, negatively impacting the processor’s bottom line.
Knowledge is power
Integrity testing takes the guesswork out of understanding the condition of plates and gaskets in plate heat exchangers. This predictive and preventative maintenance practice gives processors the knowledge they need to schedule repairs on their terms.
Process with confidence
Proactively addressing and planning for process critical maintenance by utilizing integrity testing for gasketed plate heat exchangers gives processors confidence in the reliability of their equipment. This simple, non-disruptive service can have a big impact on overall performance and efficiency.
Detection designed for heat transfer systems
Integrity testing is predictive and preventative maintenance that has been specifically designed for gasketed plate heat exchangers. Years of alternating temperature loads, pulsations, pressure impacts and abrasive cleaning media destroy the thin stainless-steel plates in plate heat exchangers. The result is an above-average extent of fatigue cracks in heat exchangers. Bacteria can migrate through these microscopic plate defects and cracks, causing microbial contamination. Integrity testing uses hydrogen as a test gas method to identify these minute leakage levels.
How integrity testing works
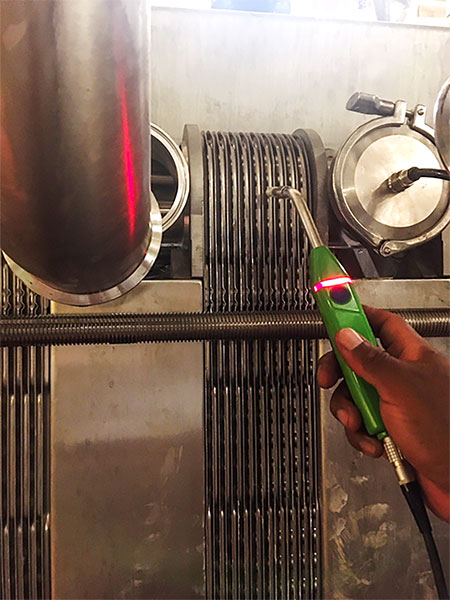
IMAGE 2: The integrity testing precision sensor can identify the type of defect from micro-crack to corrosion, gasket failure and more.
Integrity testing for heat exchangers delivers unmatched convenience, accuracy and safety, but how does it work?
First, a nontoxic, nonflammable mix of hydrogen and nitrogen is pumped through a gasketed plate heat exchanger, revealing any microscopic cracks, corrosion or material fatigue. Then a precision sensor is used to detect any discharge of gas. The detector can identify the type of defect from microcrack to corrosion, gasket failure and beyond.
Why Hydrogen?
Hydrogen delivers maximum precision
A 5% to 10% hydrogen-nitrogen mix is ideal for testing a gasketed plate heat exchanger’s condition. It diffuses quickly and completely uncovers flaws smaller than any liquid inside the unit could penetrate.
Hydrogen minimizes false positives
Compared to other tracer gases, hydrogen has a lower probability of false positives because it has a low parts per million (ppm) in the atmosphere and dissipates rapidly after use. The result is decreased opportunity for error, saving processors time on unneeded repairs and money on unnecessary expenses.
Hydrogen testing yields rapid results
The integrity testing method with hydrogen does not require plate heat exchangers to be opened, making testing convenient and fast. When the gas pumps are connected to a drained unit the results are conclusive within 15 minutes. Disruption to day-to-day processing is minimal, as no cleaning or post-test procedures are required.
Hydrogen is food-industry-approved
The hydrogen mix used for integrity testing is nonflammable, nontoxic and approved for use in the food industry. Additionally, this method will not stress or corrode plates or gaskets, protecting not only consumer products but processors’ high-value equipment.
Hydrogen is an eco-friendly option
Hydrogen and nitrogen are non-scarce, sustainable resources that can be utilized without harmful environmental
outcomes. Other methods depend on hard-to-find and nonrenewable helium.
The Integrity Test Advantage
With its ability to identify material fatigue and microscopic cracks before they turn into harmful leaks, integrity testing has a great advantage over other methods of typical heat exchanger testing options used by food and beverage processors.
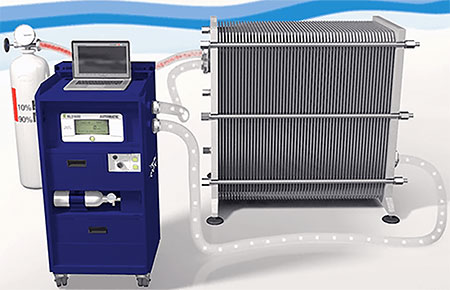
IMAGE 3: Integrity Tester: Integrity testing uses a mix of hydrogen and nitrogen pumped through the gasketed plate heat exchanger to reveal any microscopic cracks, corrosion or material fatigue.
Rapid results: 15 minutes per section test time
Minimally disruptive: No need to open plate packs, clean or perform post-test procedures
Maximum insight: Hydrogen detects the smallest flaws and flaw types with a low probability of error
Safe and sustainable: Integrity testing methods will not damage equipment, contaminate consumable products or cause environmental harm
Integrity testing = overall operational value
From tight production schedules to ongoing expansions and modifications to keep up with rapidly evolving consumer trends and an ever-changing supply chain, processors face a variety of challenges each day. Effective predictive and preventative maintenance through gasketed plate heat exchanger integrity testing is an optimal opportunity for processors to add value to their processing organization.
Protect consumer safety
With the identification of microcracks and corrosion before they develop, processors can mitigate the risk of product contamination and ensure greater consumer safety.
Eliminate waste
Early detection and proactive corrective actions in a calculated manner result in decreased product waste and reduced waste handling charges.
Increased efficiency
The elimination of product waste naturally leads to increased throughput. Processes function at a higher efficiency rate, with decreased unexpected downtimes when operating properly thanks to routine maintenance.
Prolonged equipment life span
Regular maintenance like heat exchanger testing annually or biannually significantly improves maintenance planning and ensures equipment is in good working order, resulting in a prolonged heat exchanger life span.
Integrity testing for gasketed plate heat exchangers represents a proactive approach that holds immense value for the food and beverage processing industry. The benefits of this method are clear and compelling. It offers processors the knowledge, confidence and control needed to ensure consumer safety, protect brand integrity and optimize their operations.
By identifying microscopic cracks and material fatigue before they escalate into harmful leaks, integrity testing empowers processors to plan for maintenance on their terms, preventing unscheduled shutdowns and excessive waste. This method, specifically designed for heat exchanger systems, uses hydrogen to deliver rapid, precise and eco-friendly results, making it a safer and more technologically advanced choice compared to other testing methods.
In the competitive landscape of food and beverage processing, where efficiency and safety are paramount, integrity testing stands out as a game-changer. It adds operational value by protecting consumer safety, eliminating waste, increasing efficiency and prolonging equipment life span. Processors who embrace integrity testing are not only safeguarding their brand reputation but also ensuring their long-term success in an industry where safety and reliability are nonnegotiable.