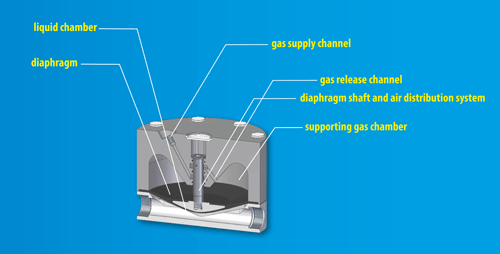
Pulsation dampeners are an essential component in fluid systems, helping to mitigate pressure fluctuations and ensure smooth flow. These devices play a crucial role in preventing damage to pipelines, pumps and other system components. Among the various types of pulsation dampeners, inline active self-regulating diaphragm dampeners serve a distinct function and offer unique advantages. This article explores that specific type and its working principles, benefits and applications in industrial settings.
Understanding the Source of Pulsation
Pulsation dampeners absorb pressure spikes and pulsations in fluid systems, which commonly originate from positive displacement pumps—particularly reciprocating pumps (e.g., piston and diaphragm pumps) and some rotary pumps like hose pumps. While these pumps offer advantages over other types, they operate at relatively low speeds and have noticeable breaks between cycles, leading to pulsation.
Impact on Measurement Devices
High pulsation makes it difficult to measure pressure and flow and can also affect the life span of measurement devices. Pulsating flow is characterized by continuous changes in fluid velocity, requiring a high sampling frequency for accurate measurements. In such conditions, it is often necessary to use advanced and expensive mass flow meters or ultrasonic flow meters.
How Pulsation Dampeners Prevent Water Hammering
Water hammer is a hydraulic shock phenomenon that occurs when a fluid in motion is suddenly forced to stop or change direction, causing a rapid pressure spike. This can result in pipe, valve and pump failure. Pulsation dampeners play a crucial role in preventing and mitigating water hammer by absorbing and redistributing pressure surges. Pulsation dampeners smooth out the flow by reducing pulsations that contribute to pressure shocks.
Inline Active Self-Regulating Diaphragm Pulsation Dampeners: Working Principle
Inline active self-regulating diaphragm pulsation dampeners are designed to actively respond to flow and pressure fluctuations. One of the main features is a flexible diaphragm that separates the liquid from a gas chamber, typically filled with air or nitrogen.
The gas chamber is supplied with a continuous flow of gas at a pressure that should be equal to or slightly higher than the highest pressure peak generated by the pump. For example, in the case of a diaphragm pump powered by compressed air, this pressure should match the pump’s supply pressure.
This type of dampener is equipped with an air distribution system integrated with a shaft attached to the diaphragm. This system automatically opens and closes the gas supply, which supports the diaphragm and ensures pressure balance on both sides.
Inside the dampener, two main scenarios occur during the regulating stage:
- When the hydraulic side experiences lower pressure, the supporting gas pressure pushes the diaphragm toward the hydraulic chamber, simultaneously opening the gas outlet to the atmosphere.
- As gas is released, the pressure drops to a level that causes the diaphragm to move in the opposite direction. At its extreme displacement, the gas supply opens again, allowing gas to enter and support the diaphragm.
After several such cycles, the diaphragm reaches a balanced state, where the supporting gas pressure equals the pressure peaks on the hydraulic side. The support gas is consumed by the dampener during the regulating stage.
This self-adjusting mechanism allows the dampener to adapt to constantly changing discharge conditions of positive displacement pumps, which generate pressure based on the resistance within the system. This is particularly important when valves in the discharge pipelines open and close (e.g., during dosing operations) or when the process requires continuous adjustments to the pump’s output.
Inline Active Self-Regulating Diaphragm Pulsation Dampeners
Pressure peaks of a typical diaphragm pump operating at discharge pressure of 6 bar(g):
1) Without dampener; pressure peaks: 4 bar
2) With pulsation dampener; pressure peaks: 0.8 bar
Benefits
- Pulsation control – Inline active diaphragm dampeners provide pressure stabilization.
- Low maintenance – This design eliminates the need for external control mechanisms, making the system simpler and maintenance-free.
- Cost-effectiveness – Simpler construction leads to lower initial and operational costs.
- Compact and space-saving – This design is ideal for installations where space constraints exist.
- Continuous and active operation – These work automatically without requiring adjustments. They adapt for various applications and work well with air-operated diaphragm pumps and hose pumps.
- Corrosion and chemical resistance – Depending on the material used, these dampeners can be highly resistant to aggressive chemicals and fluids.
- Lower noise and vibration – Active dampening reduces noise levels, creating a quieter working environment.
- Extended equipment lifespan – The reduction of pressure spikes enhances the durability of system components.
Applications
- Food processing
- Oil and gas processing plants
- Chemical and pharmaceutical industries
- Fluid metering systems
Best Practices for Implementing Pulsation Dampeners
- Proper sizing: Select a dampener with an appropriate volume to match the system's pulsation levels.
- Correct placement: Install the dampener close to the source of pulsations for maximum effectiveness.
- Material compatibility: Use dampeners made from corrosion-resistant materials, such as stainless steel (AISI 316L) and plastics like polyethylene (PE) or polytetrafluoroethylene (PTFE), for aggressive fluids.
- Material properties: For abrasive liquids, choose dampeners made of wear-resistant materials, such as high-density polyethylene (HDPE) and ultra high molecular weight polyethylene (UHMW PE).
- Diaphragm design: Choose a composite diaphragm construction with a smooth, uniform surface, free of additional mounting holes in contact with the fluid. This reduces the risk of leaks and diaphragm wear while increasing cleanability.
- Clean design: In food and pharmaceutical applications, choose designs that are suitable for cleaning in place (CIP) processes. These designs eliminate dead spaces that can make cleaning difficult and promote bacterial growth.
Comparing Inline Active & Passive Pulsation Dampeners
While both active diaphragm dampeners and passive dampeners serve the purpose of reducing pulsations, their functional differences determine their suitability for different applications. Passive pulsation dampeners are usually the cheapest solution for constant operating conditions, with moderate and steady pulsations. On the other hand, active pulsation dampeners are great for dynamically changing conditions and when high precision measuring is a factor. The active dampener adapts automatically to the discharge pressure, whereas the passive dampener requires extra equipment like a discharge pressure sensor and a feedback loop to ensure the proper air pressure setting on the dampener inlet. In favor of the passive solution, it could be pointed out that it requires no constant air source. On the contrary, active dampeners require a very small but constant source of air to adaptively regulate themselves to the discharge conditions.
Pulsation dampeners play an integral role in optimizing fluid system performance by mitigating pressure fluctuations. Selecting the appropriate pulsation dampener depends on factors such as system pressure, fluid properties, required pulsation reduction and budget constraints.
Inline active self-regulating diaphragm pulsation dampeners provide a cost-effective, low-maintenance solution. They are a good option for high-precision, dynamic systems where discharge conditions are varying over time.
Understanding these technologies enables industries to select the best solution for their specific needs, ensuring smoother operations and an improved equipment lifespan.