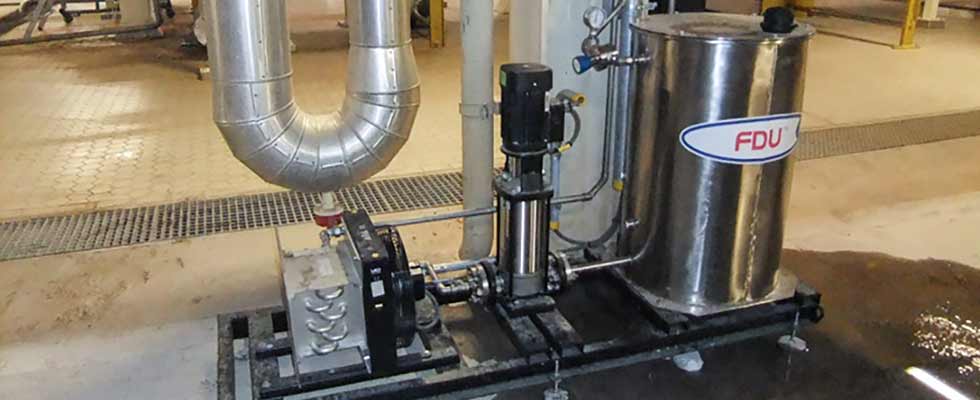
The drive to reduce energy consumption and conserve water is a universal one, and it is rare to see a company that has not outlined, in principle at least, its commitment to adopting more sustainable practices.
Understandably, efforts to meet sustainability targets often focus on the macro, for example, reevaluating high water and energy use across entire processes such as cleaning or cooling.
These actions are valid and often productive. However, further opportunities exist to improve sustainability if companies also turn their focus to the micro.
Mechanical seals are relatively small pump components and can, therefore, be easily overlooked. Yet, by examining in detail their impact on the energy and water consumption in industrial processes, it is possible for companies to make changes in improving the sustainability of an entire plant. They can also reap additional benefits including enhanced pump reliability, a return on investment and long-term operational savings.
Mechanical Seals & Sustainability
When looking at the mechanical seal in isolation, the energy savings are relatively small.
For example, a 3- to 4-inch mechanical seal will consume over 3 horsepower (hp)(2.24 kilowatt [kW]) as a maximum power absorption. That is a tiny percentage of the total power consumption of a pump and, understandably, would not be considered a real source of savings.
However, with the exception of gas-injecting seals, a large proportion of mechanical seals across all industries require a supply of clean, cool flush liquid to keep the seal faces lubricated and prevent overheating.
This constant supply of flush liquid is provided by a seal support system or piping plan, often from an external source, and is evaporated off or discarded down the drain at the end of the process. When the thermal efficiency of this system is taken into account, the relevance of the sealing solution becomes more significant, in terms of both water and power consumption.
A Sustainable Seal Support System
The way in which a seal support system is configured can reduce the amount of water consumed to virtually zero. Additionally, it can reduce a pump’s energy costs by as much as 96 percent.
The solution lies in employing a continuous loop water management system. This recycles the flush water to provide an unbroken, regulated supply of clean liquid to lubricate and cool the mechanical seal faces.
Unlike traditional systems, which require downstream separation/evaporation and/or effluent treatment, virtually the only waste this system generates is roughly 1 teaspoonful of liquid a day, in the form of evaporation.
While traditional piping plans inject the cool water into the process stream, necessitating reheating, this system only dissipates the heat that is generated at the seal faces, allowing the process to be maintained at the appropriate temperature.
Power Saving Equals Cost Savings
The comparative energy efficiency of these different systems has been calculated using a hypothetical, but typical, hot oil pumping application.
This configuration involves a single-stage, end suction centrifugal pump, sealed using mechanical seals, with the assumption that heat lost at the pump must be replaced at the system boiler/heat exchanger, and based on:
- pumped fluid—hydrocarbon at 600 F
- specific gravity of 0.8
- specific heat—1.67kJ- C (0.4 BTU/lb- C)
- system pressure—50 pounds per square inch gauge (psig) in seal chamber
- pump driver—50 hp (37 kW)
The power consumption for a traditional seal support system, supplying cool flush water from an external source directly into the process fluid, was calculated at 47.4 kilowatts per hour (kW/hr).
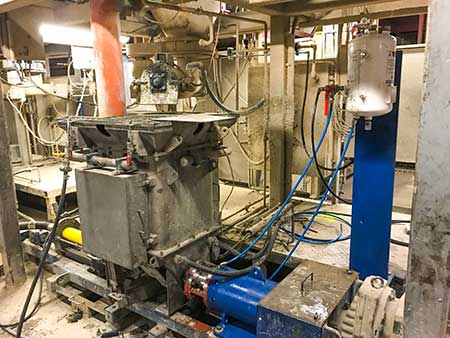
The power consumption for a continuous loop seal support system, which dissipates heat generated at the seal faces only, was 1.7 kW/hr. To put this 45.7 kW of saved energy into context, if a pump is running
24 hours a day, 365 days a year, a continuous loop seal support system could save around 400,000 kW of energy per year. This equates to a 96 percent reduction in energy costs for that seal support system—savings that are more meaningful when applied to multiple pumps and locations.
There is, therefore, a powerful argument for proactively investigating where mechanical seals and their support systems might bring about environmental benefits.
A seal energy audit is an efficient way to identify and quantify the monetary value associated with upgrading seals and support systems. This kind of audit involves inspecting the seal and seal support system of each pump, recording the seal arrangement, support system configuration, process data and seal system parameters such as water flow and temperature.
This data is used to calculate the energy impact of every mechanical seal in the plant. High energy use can be easily identified and reviewed to see if a more efficient piping plan configuration, such as a continuous loop water management system, is appropriate.
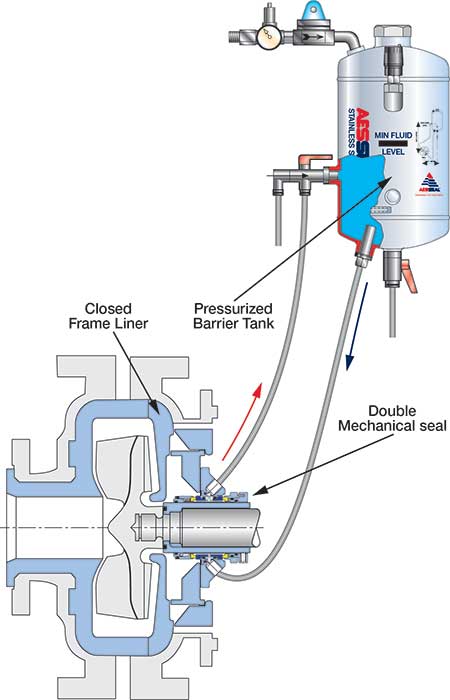
An audit summary will provide decision makers with a review of potential opportunities, the investment required and potential returns.
This should include a “quick win” overview that identifies where maximum efficiencies can be achieved for the minimal outlay.
There can be a considerable communications gap between plant maintenance and reliability personnel, who often make decisions about piping plans in isolation, and company members responsible for overseeing and reducing energy consumption.
A seal energy audit can help bridge this gap, bringing greater visibility to one element of a plant that might be considered small and, therefore, inconsequential, but which has the potential to transform operational efficiencies and achieve cost savings.
Responsible companies constantly strive to meet the requirements of the International Standards Organization (ISO) 14001 Standard for environmental management systems and ISO 50001 standard for energy management systems. But those that are willing to consider the bigger picture, and the smallest components, are the ones most likely to achieve positive environmental impacts that go hand in hand with operational improvements and cost efficiencies.