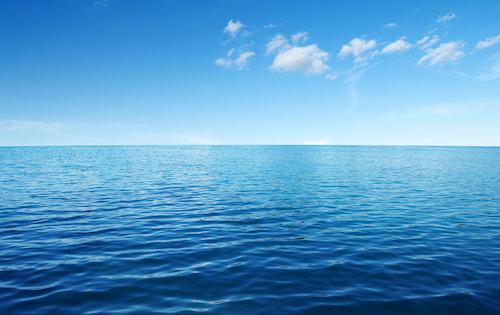
Reverse osmosis (RO), or using a semi-permeable membrane to remove dissolved solids from water, is the most common type of desalination. There is a wide range of reverse osmosis systems, producing anywhere from a few gallons to millions of gallons of clean water per day.
Due to the differences in scale, it is important to treat a system that produces only a small amount of water per day differently than those in the millions. One difference lies in how often the membranes of these systems should be cleaned.
Each membrane, as well as the watermaker around it, is designed differently. The manufacturer of the product will specify how often its membranes should be cleaned to prevent scaling (when salts and other particles plug the membranes) and fouling (when dirt, marine growth or algae clog the membrane). Maintaining a rigorous cleaning schedule, per the manufacturer’s instructions, can help maintain the membrane for a lifetime of three to five years.
However, in smaller-scale watermakers with fewer membranes, there is a better way. With no cleaning at all, and some minor adjustments to the pretreating process, these membranes can last up to two years at a fraction of the cost—even when factoring in the need to purchase membranes more often.
It is a complicated process; so, let’s break it down.
Inconsistent Cleaning Practices
The membrane cleaning process is, to put it mildly, a drain on resources. Since all sources of feed water can have slightly different characteristics, the suggested cleaning method of RO membranes differs greatly from one location to the next. Most manufacturers suggest cleaning when water flow and salt rejection reduce by a certain percent, as well as how to clean the membrane based on the type of scaling or fouling (such as calcium scale, iron oxide and others).
Once users know what the membrane is scaled or fouled with, they may need either acid or alkaline cleanings—or both. During the cleaning process, users also need to maintain a specific temperature, pressure and pH to ensure a full clean. However, since the pH can change during cleaning, the user must constantly adjust the cleaning chemical concentration, soak the membrane, flush and repeat two to three times.
Aside from the manpower required during the process, cleaning-in-place also requires a storage tank, pipes and hoses and a significant amount of expensive chemicals. Once the membranes are cleaned, workers must also dispose of
and store the remaining chemicals, which places an additional burden on the operation.
In many operations, this complex process is left by the wayside, as busy workers prioritize meeting daily quotas over spending precious time and resources on cleaning. Through 40 years of building reverse osmosis systems, even when users are supplied with the needed equipment and instructions to clean-in-place consistently, it usually does not come to fruition.
Those who follow this rigorous process a few times a year still have no guarantee that the system will gain back the flow or salt rejection it lost prior to cleaning.
When Size Makes a Difference
In some cases, following a rigorous cleaning schedule is the most time-efficient and cost-effective way to manage watermaker membranes.
Generally speaking, for watermakers that generate over 80,000 gallons of fresh water per day (which likely have 24 or so membranes), it is preferable to follow the manufacturer’s guidelines and clean the membranes rigorously. The more membranes a system contains, the more expensive it would be to purchase new ones after two years. Also, cleaning hundreds of membranes has a lower cost per membrane than cleaning 10, as a direct function of the chemical and labor costs.
However, for desalination systems under the 80,000 gallons and 24 membranes threshold, that begins to change. As chemical costs add up and the expense of purchasing new membranes decreases, the alternative becomes more attractive. Simply by following a more conservative recovery approach coupled with a powerful method of pretreatment, users can decrease both chemical costs and planned downtime.
Conservative vs. Aggressive Recovery
All reverse osmosis systems can be designed with either a conservative or aggressive recovery. Conservative recovery is designed to generate less output but it also decreases the amount of scaling that occurs. If 100 gallons of seawater are sent through an RO membrane, a percentage of that turns into fresh water. A more conservative recovery of 30% would generate 30 gallons of fresh water, while an aggressive recovery of 55% would generate 55 gallons.
It seems like a no-brainer to go aggressive—until risks are considered. With a system designed for aggressive recovery, membranes must either be cleaned and chemical antiscalant added diligently, as the amount of salt that precipitates and crystallizes on the membrane increases. And, for systems below that 24-membrane threshold, the cost of labor, chemicals, disposal and lost production to clean diligently, resulting in an expected lifetime of three to five years, is greater than the cost of replacing the membranes every two years with no cleaning.
Conservative recovery allows membranes to last roughly two years without excessive scaling—but there is another factor to consider: membranes can also fail due to fouling. Anything from dirt and algae to marine growth can affect the membrane’s lifetime, and conservative recovery cannot stop fouling from occurring. To prevent fouling without the need for consistent cleaning of the membranes, it is all about the pretreatment process.
Pretreating With Filtration, Not Chemicals
A traditional method of pretreating seawater before it enters the reverse osmosis system is using chemicals, such as flocculants, coagulants and antiscalants. This method causes several concerns, from the cost of acquiring and storing chemicals to properly disposing of the chemicals on a consistent basis.
The biggest risk of using chemicals for pretreatment can occur if the chemical pumps fail or if the user runs out of chemicals. For systems designed with aggressive recovery that rely on chemicals for pretreatment, the membranes would scale or foul quickly.
However, by using a higher level of filtration before the reverse osmosis process, a greater amount of suspended solids can be removed, lessening the likelihood of fouling on the membrane. A simple four-stage filtration process can remove most unwanted materials before the water ever touches the membrane:
- Granulated activated carbon filtering out anything larger than 25 microns
- Bag filters to filter out anything > 5 microns
- String-wound filters to filter out anything > 1 micron
- Pleated cartridge filters to filter out anything > 1/2 micron
Some reverse osmosis system manufacturers filter suspended solids down to only 5 microns, to limit costs on filter housings and filters. However, the cost of the additional filters to remove solids down to 1/2 micron pales in comparison to either cleaning consistently to avoid fouling or addressing excessive fouling after the fact.
To confirm this hypothesis, a study was conducted with an offshore platform to determine its costs per gallon of fresh water produced. To do so, it compared a watermaker that followed the above filtration process with conservative recovery and no cleaning of the membranes against a watermaker with aggressive recovery, less filtration and consistent cleanings. Two pieces of data were tracked: total volume of fresh water produced and the total cost incurred on each piece of equipment, including replacement membranes, replacement filters, labor costs, membrane cleaning chemicals and the lost production while cleaning.
The end result: the system designed with conservative recovery and more thorough pretreatment filtration came out to a cost of roughly $0.01 per gallon, while the system designed with aggressive recovery, less filtration and that underwent consistent cleanings landed significantly higher than $0.01 per gallon. When considering the thousands of gallons produced per day, cents add up.
At the end of the day, every RO system is built differently and has its own cleaning requirements. For larger watermakers, there is a cost benefit of cleaning the RO membranes on a consistent schedule to protect against scaling and fouling and improve the lifetime of the product.
However, as the size of the system decreases, it becomes more efficient to cast aside the hassle, cost and time of cleaning in favor of a carefully designed strategy built on conservative recovery and diligent pretreatment filtration. Though a lifetime of two years seems less favorable at first, there is value when considering cost savings over time.