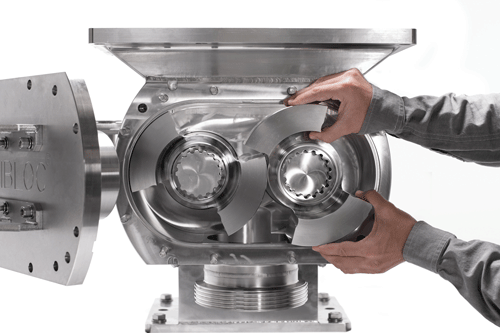
A well-made and properly designed sanitary pump used as intended should last for many years with minimal maintenance. Still, as with any machine, sanitary pumps do have wear items and operating parameters that, when compromised, can impact the life span of equipment and ultimately the quality of the product produced in the facility.
Different applications call for different sanitary pump specifications. A supplier will help a user identify a purpose-built pump for the operation. That pump will come with a recommended maintenance schedule, but generally speaking, faster running, lower viscosity, higher pressure applications will need more attention. In addition, food plants that require daily washdowns are particularly hard on pump wear and tear because the extra handling of individual components naturally leads to potential damage that can degrade pump performance and lead to crevices for bacteria to form.
There is no one-size-fits-all approach to sanitary pump maintenance, but this article will address key subject areas for users to keep at the top of their minds. Ensure peak efficiency in any operation by taking a proactive approach using these tips.
Prevent Foreign Materials
Every food processor is aware of the risk of foreign material intrusion. Organic material and random debris can enter the processing line just about anywhere, despite users taking steps to ensure this does not happen. But suppose a user identifies foreign materials upstream of their sanitary pump. In that case, it is important to check the pump head for any damage—such as scratches, galling or dents—that can harbor bacteria or worse, such as introducing metal shavings and additional debris into the product.
Most food processors use metal detection at high-risk points along the processing line to ensure contaminants never make it to the public. An additional measure that can help to protect a user’s sanitary pump and product quality is to use a strainer. Strainers separate large particles from smaller particles to ensure the purity of consumable products.
Monitor Pump Performance
Perhaps the most obvious of all indications that a sanitary pump needs maintenance is a change in flow rates or repeated pressure drops. If the product running through a sanitary pump has not changed in type or viscosity, and a user needs to increase rotations per minute (rpm) or pressure to meet the desired flow rate, they may damage the pump head.
A sanitary pump works within its specified tolerances, so deviations unrelated to the product could result from debris, corrosion or abrasion. If nothing else has changed and users are
still experiencing performance irregularities, they should check the pump head for damage.
Do Not Ignore Leaks
Any leaks of product or barrier fluids are indicators that shaft seals need replacing.
If running corrosive or abrasive products, a user should replace their shaft seals more frequently.
When a single mechanical seal is compromised, product will leak onto the floor. While it may be tempting to ignore a minor leak, keep in mind that single mechanical seals rely on the product to keep the seal cool. Product on the floor could lead to the seal running dry—and as a result, hot. If this happens, the seal may burn up, which will allow the product to enter the pump housing and could cause further damage.
Double mechanical seals are typically used as an added layer of protection when corrosive or abrasive products are processed. The primary seal is in contact with the product, while the secondary seal is closer to the pump housing. A barrier fluid between the two seals, typically water or oil, keeps the seals cool. Leaks in the secondary seal are harder to detect but essential to prevent primary seal failure.
If a pump has double mechanical seals, users will want to periodically check the flush housing to ensure that the barrier fluid is at the proper levels. Adding a seal pot accessory that senses fluid levels, pressure and temperature will alert users when abnormalities exist. Preventative action can then be taken to protect pumps from damage and product from contaminants.
Conduct Regular Oil Changes
Consult the owner’s manual regarding oil change requirements within the pump’s gearbox as with any equipment. If the application requires strip-down clean-out-of-place procedures (COP), long run times or high temperatures, pressure and speed, consult with the manufacturer about an oil change schedule best suited for the operation.
Inspect Pump Alignment
Most sanitary pumps are a two-piece unit, the pump head and the gearbox. Over time, these two components can become misaligned, which can put unwanted stress on the rotor shafts. Visually check that the two components are flush and adjust if they have moved.
Alternatively, users can consider a flange mounted pump for operations with high pressures and speeds coupled with low viscosity. The flanges ensure correct alignment under the most challenging applications.
Be Aware of Excessive Vibration
Sanitary pumps, like most mechanical equipment, naturally vibrate under normal operation. If the pump is vibrating more than usual, check for misalignment between the pump head and gearbox.
If the components are aligned, users may next want to check the pump head for any galling or pitting that may have occurred, causing the rotors to operate out of tolerance. Finally, if the pump head is pristine and there is still suspected excessive vibration, check the gearbox’s bearings and oil level. Contact the pump supplier for feedback and support if everything seems to be within spec.
Investigate Unusual Sounds
Abnormal operating sounds are another indicator that a pump may need attention. If running highly viscous products, tolerances will be greater, and pump performance may not be affected.
If there is any unusual knocking or pinging, first check the alignment of the pump and gearbox, and then check the pump head for physical damage and finally the gearbox for bearing operation and oil levels.
Pay Attention to External Temperature
It is not uncommon for a new pump to run a little hot during break-in. The same is true when running at higher rpm and tight tolerances.
However, if users notice excessive heat emission from a pump or a change in product temperature downstream of the pump, there may be a need for preventative maintenance. If pressure, rpm and flow rates are normal, check the oil level in the gearbox. If that isfine, chances are the pump is operating normally. When in doubt, contact the pump supplier for support.
Spare Parts & Preventative Maintenance
A pump supplier can recommend manufacturer-approved spare parts to keep on hand, such as shaft seals and O-ring kits. Consult a supplier to establish a preventative maintenance schedule specifically suited for the application. Some suppliers may offer a preventative maintenance agreement as well.