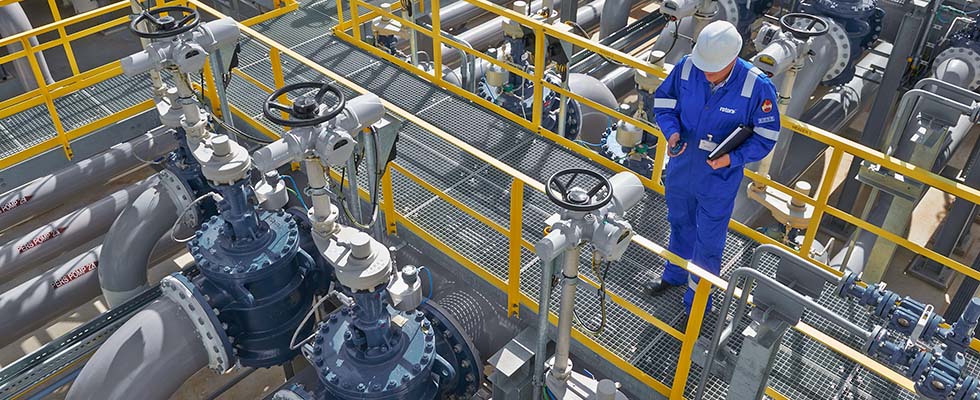
Flow control refers to the management of liquids and gases in industrial applications and markets. Flow control assets like actuators are key items of equipment across many kinds of industries and are installed on thousands of sites all over the world—including in oil, gas, water, power, chemical, industrial and process control applications. Valves that control the flow of fluids can be pneumatically, hydraulically or electrically actuated. The type of actuator is dependent on a variety of factors, such as power sources, location, type of control required, what fluid is being controlled and frequency of operation. Flow control assets often work in challenging operating conditions, faced with extreme temperatures and excess vibration. They can also operate infrequently but still must offer high levels of reaction, accuracy and reliability.
Flow control, when managed well and powered by reliable actuators, maximizes operational reliability and efficiency. For example, within water and wastewater applications, actuators are used to control water, including filtration, desalination, potable water treatment, environmental protection and distribution. Effluent processing and clean safe output from sewage treatment plants can be ensured when actuators are controlling the flow. Actuators within water applications are environmentally sealed and are housed in enclosures that provide watertight protection, preventing water ingress from the environment. Within power operations, actuators are durable and built to withstand harsh environments (including extremes of temperature and vibration). They must have the correct certification to ensure safe operation. Within the oil and gas industry, actuators provide routine flow control at tank farms and wellheads, while critical safety duties are provided by actuators with fail-safe functionality.
Process control applications (where repeatable and reliable valve operation is an essential requirement) are found within a variety of industries; this type of control may be seen within food and beverage, chemical production and steel/aluminum industries. Within these applications, specialist knowledge from flow control providers for isolation, control and flow regulation of liquids can maximize productivity and uptime. Accurate dosing of liquid ingredients results in less wastage. Precision and repeatability from process control actuators ensure reliable and consistent results.
The Importance of Asset Uptime
Efficient, reliable, safe and effective flow control is at the heart of many industries. The availability of these flow control assets is key to successful operation. Asset failure and obsolescence are damaging to output, productivity, reputation and profit. The work actuators do is vital; even if a site does not have full access to their flow control assets for a short period of time, the damage can be severe. For a site to be profitable and productive, it must have high periods of uptime. Unplanned downtime (due to failure or datedness) is one of the most serious situations that a plant manager can face. To minimize this, flow control assets must be managed by maintenance services to keep them working in as optimal a way as possible.
The Importance of Maintenance
Uptime is a key factor in the success of many plants and sites all over the world and is essential for a site to achieve its core objectives. The maintenance and upkeep of these key assets should be at the forefront of operators’ minds. An effective asset maintenance program ensures actuators always operate at optimum performance level, performing their duties to make sure sites work reliably, efficiently and—above all—safely. If service and maintenance programs are not in place, there can be serious effects on productivity and performance. Any unplanned downtime due to lack of equipment availability can result in economic loss and reputational damage, even if a site is offline for only a short period of time. Reputational damage is also a concern, as is the potential for regulatory fines for utility or power services.
Failure of the key assets that keep a site running can result in operators seeing reduced productivity, poor performance and a drop in quality. Unintended downtime is the most serious consequence of ineffective maintenance. Effective management of flow control assets is therefore an essential consideration for their long-term reliability and viability.
An asset management service and maintenance strategy, focusing on the entire life cycle of an asset, is essential to ensure the long-term reliability and viability of the flow control assets on site. A comprehensive program for maintenance allows critical assets to operate optimally, ensuring they are always available. A program of this kind should be holistic, considering the entire life cycle of each asset and the management of its potential obsolescence and how this will impact the entire site. A full life cycle asset management program is likely to offer increased uptime, improved performance and a reduction in unplanned costs.
It looks at each flow control asset as part of a bigger picture, with bespoke maintenance processes which are customizable. Service programs of these kind provide a set cost to operators, allowing for easy management of budgets. They offer maintenance programs that will not simply send an engineer to fix a broken or underperforming actuator; they plan for the likelihood of such an event, focusing on long-term maintenance and support. This approach can increase uptime, eliminate unexpected maintenance costs and help manage long-term viability of a site.
The most important part of a service program is the consideration of the entire life cycle of an asset. The risks of aging equipment can be considerable, but with dedicated service and maintenance programs, operators can manage potential datedness alongside the important task of keeping a site running at an optimum level, with minimal-to-no unplanned downtime.