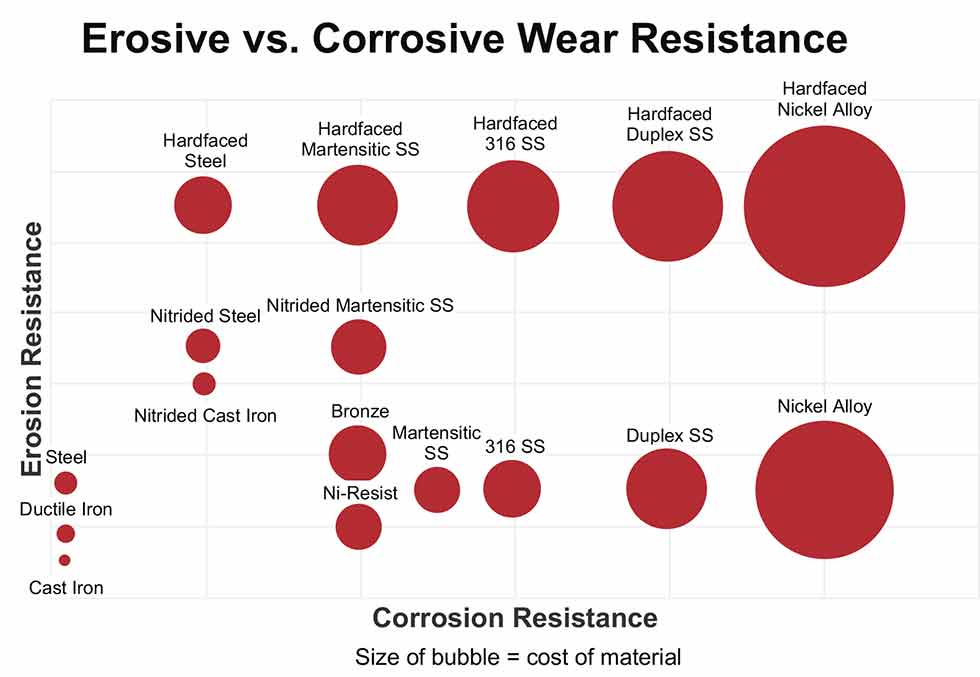
It could be a chemical plant taking on a new formulation or a facility modernizing to meet updated environmental health and safety regulations. The conditions in which a pump is really running are often different than their intended design and operation.
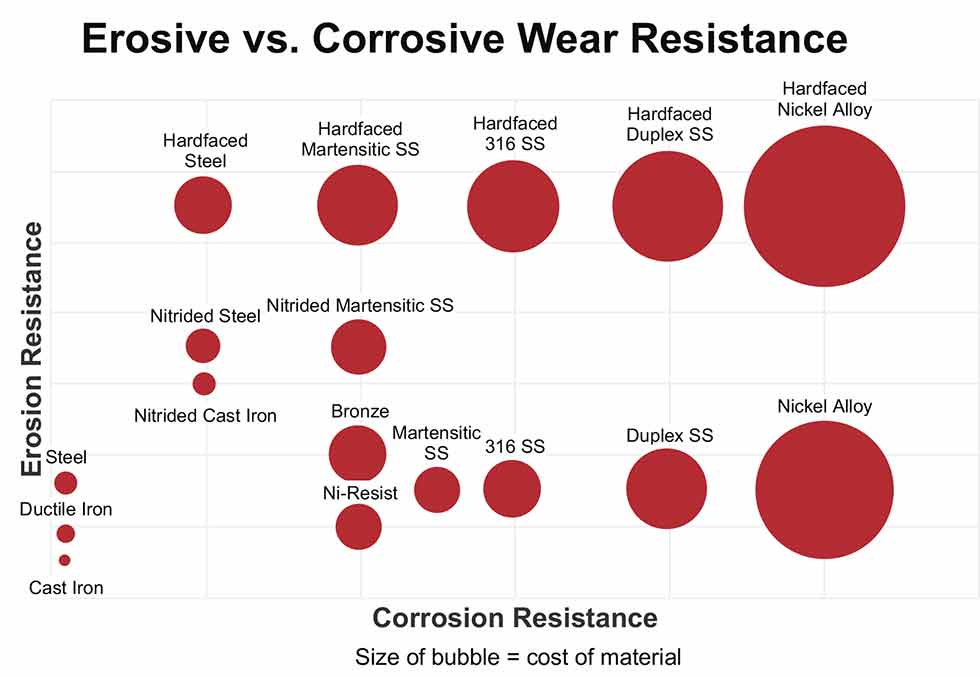
End users will come to a manufacturer wondering whether a pump can run on a new process condition. However, when manufacturers are contacted for service or parts, they often discover that the pump is no longer operating well and is no longer fit for its purpose. When a facility is not producing, it can be losing money as well as putting supply contracts in jeopardy.
Chemical Considerations
In the chemical industry, it is not uncommon for formulations or end products to change. This necessitates a change upstream of the production process and the particulars of how the pump needs to perform. For example:
- Some polymers and adhesives can go up to high viscosities. The high viscosity can reduce the net positive suction head available (NPSHa) of the fluid. It does not move well and can be hard to get into the pump.
- Some chemical formulations can also be shear sensitive. Without the right pump running at the right speed, excessive shear imparted on the fluid by the pump can cause it to change properties and render it unusable.
On a recent visit to inspect a repair of a reactor circulation pump, a reliability engineer for a major polymer manufacturer said they do not always know exactly what the fluid composition will be. The fluid is received from the customer and put in the reactor to process. The manufacturer also manages multiple clients and end products through the same reactor. The pump needs to handle whatever gets sent through it, and the operators need to make it work on the available equipment.
Yet, when the pump or the people are not ready, a catastrophe can ensue. The same engineer shared an anecdote of literally tossing a failed pump in the back of a truck and bringing it to local shops to see who could service it the fastest.
Savvy engineers and operators can insulate themselves by:
- selecting a pump with the flexibility to handle a range of future operating conditions
- keeping a progressive service and maintenance program for the facility
Prepare for Future Wear & Tear
A refinery recently needed spare parts for a pair of twin screw pumps operating on cokers that had begun to vibrate severely. The pump had been installed more than 20 years ago, and while in service, wear parts were replaced periodically. However, the crude started to incorporate more corrosive content, so much that the rotors were being chemically attacked. One pump was pulled out of service due to excessive vibration, and upon inspection the rotor was pitting and cracking due to the corrosive fluid. With the pump out of service, the refinery was losing in excess of $1 million per day and considering reverse engineering.
The moral of these stories is that, when selecting a pump, it is important to consider the current state and the conditions that the pump may encounter. Armed with the right information, a pump manufacturer can design a pump that gives the operator flexibility and reliability through materials, coatings and processes. Sometimes even the initial technology choice can be made with the future in mind.
For example, twin screw positive displacement pumps may be selected for flexibility in discharge head and viscosity handling. These pumps have inherently low net positive suction head required (NPSHr), are resistant to shear and can run at low speeds where appropriate. For some pump styles, it is possible to provide a modular design that can have an element switched out for different capacity or pressure capability when conditions change.
Maintenance & Overhaul
It is important for users to institute a regularly scheduled maintenance and overhaul program. Keeping critical spare parts on hand is best practice and the first line of defense. However, as operators see their process change, it can be worthwhile to partner with the manufacturer to ensure the pump is capable of performing the new operation. The cost of modifying a pump is often peanuts in comparison to the cost of downtime. In the refinery example, the payback period was mere hours.
A pump manufacturer prepared to provide aftermarket, engineering and other support can be a true asset for these producers. That refinery is now working on upgrading the material selection and coatings on their screws to better withstand the new corrosive threat.
A Word of Warning
Avoid overspecifying a pump as a remedy for preparedness. Designing a pump that is too future-proof can have its own consequences. This can mean a bigger pump, or one with higher grade materials. Larger pumps bring increased capital costs along with larger parts, which cost more to replace. The combined extra capital cost and operational expense can damage the project prospects. An engineer with this application must balance specifying enough to meet the need without overburdening the project. Partnering with a pump provider to understand the application can lead to the best solution.