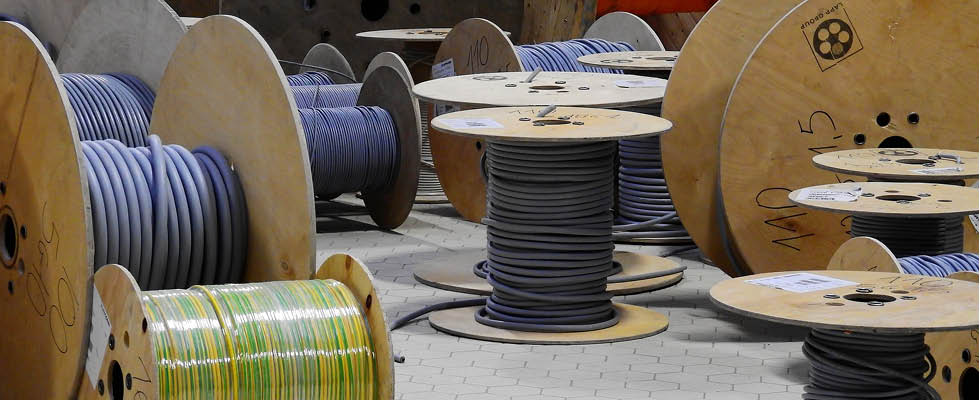
It may seem obvious, but it is worth remembering the right cable selection must be done according to international and local standards.
There are four key recommendations:
Wire type: Choose copper over aluminum conductors for better conductivity.
Type of insulation: Select according to the operating temperature of the system.
Sizing: The cable size depends on the motor’s full load amps (FLA) and the distance between the motor and switching gear. According to the International Electrotechnical Commission (IEC), cable sizes are calculated from IEC 60364-5-52: Low-voltage electrical installations - Part 5-52: Selection and erection of electrical equipment - Wiring systems. In the United States, determination of current-carrying capacity for conductors is made in accordance with National Fire Protection Association (NFPA) 70: National Electrical Code (NEC). The section that speaks about the cable to be used to power three-phase motors is Article 430 (part II): Motors, Motor Circuits and Controllers.
IMAGE 1: The choice of cable and its length is more problematic when the motor is driven by a variable frequency drive (VFD). (Image courtesy of Bru-nO, Pixabay)
Environmental conditions: Check and adapt to environmental conditions—ambient temperature but also humidity levels, presence of foreign solid bodies, presence of corrosive or polluting substances, mechanical stresses such as impacts and vibrations, presence of flora and/or mold growth, presence of fauna, solar radiation and ultraviolet radiation, seismic effects, etc.
What Is the Maximum Length Between a Motor & Its Starter Gear?
When it comes to understanding motor connections, it is a good idea to begin with the straightforward setup of a direct-on-line (DOL) starter powering a three-phase motor. Here, the cable length plays a crucial role due to voltage drop along the line. While cables boast low impedance, it is not nonexistent. As current flows through, a voltage drop occurs between the starting point and end.
This voltage drop matters. The motor’s proper operation relies on the voltage reaching its terminals. Therefore, line voltage drops must be kept in check by carefully choosing the appropriate supply lines. Generally, optimal motor performance thrives on a voltage within ±5% of its nominal value at steady state.
However, it is important to remember the NEC sets standards for maximum permissible voltage drop in circuits, typically around 3% for branch circuits. This means finding a balance between cable length and acceptable voltage drop to ensure both regulatory compliance and motor health.
The next step is to delve deeper into the factors influencing voltage drop and how to calculate it effectively.
The simple voltage drop formula is:
Line drop voltage (V) =
√3 x current (A) x wire resistance (Ω /m) x wire length (m)
The complete formula for a balanced three-phases is as follows:
Line drop voltage (V) = √3 x current (A) x [(wire resistance (Ω /m) x cosφ) + (wire reactance (Ω /m) x sinφ)] x wire length (m)
If the cable is a lightweight player—anything under 25 square millimeters (mm²)—there is no need to be concerned about the reactance (cable resistance effect). But for thicker cables, it may be necessary to consult the manufacturer’s manual or use these handy values:
Regular cables (single or multi-conductor): 0.08 milliohms per meter
Overhead lines: 0.3 milliohms per meter
Once the details on the motor—including its environment and any local regulations—have been gathered, it becomes much easier to choose the right cable for the DOL starter. There are even online calculators and tables to make it even easier. The choice of cable and its length is more problematic when the motor is driven by a variable frequency drive (VFD).
Why Cable Length Matters
VFDs offer significant benefits for controlling induction electric motors. However, there is a potential downside: damage to the motor due to the inverter effect. One of the causes of this damage occurs when the power cable connecting the VFD to the motor is too long. But why does cable length matter?
The PWM Signal
The output of a VFD is characterized by a pulse width modulation (PWM) signal. This signal is a bit like a light switch that flickers on and off rapidly, and that flickering is happening in the cable connecting the VFD to the motor. When this PWM signal encounters the motor terminals, problems can arise if the impedance of the power cord and the motor are not consistent (which happens with excessively long cables).
Long cables create “reflections” that bounce back toward the motor, adding to the original signal. This results in a significantly higher voltage and fast rise steepness (dV/dt) at the motor terminals. This can lead to dangerous voltage spikes that fry the motor’s insulation.
Fighting Back: Filters to the Rescue
To limit the steepness of voltage rise (dV/dt), a tried-and-tested approach is to use dV/dt filters. These filters reduce the risk of damage to motor insulation, lower operating temperature and minimize motor noise. They also allow for longer motor cable lengths, typically for 100 to 300 feet (30 to 100 meters) depending on the switching frequency.
For longer length and avoiding peak voltages, the approach is to use sinus wave filters instead of dV/dt filters. At the output of the filter, a perfectly sinusoidal signal should be obtained.
The need for filters is even greater in the case of retrofitting an application where the existing motor is kept. If the motor is not conforming to IEC60034-25 or National Electrical Manufacturers Association (NEMA) MG1, the user should always add a dV/dt filter up to 100 feet long cables and sinus wave filter above this length. The distance between a VFD and an electric motor can be considered long when it exceeds approximately 300 meters and requires mitigation means.
Protecting a VFD From EMI
When connecting a three-phase motor to a VFD, it is a good idea to use a shielded cable. Shielded cables are like bodyguards for the VFD and nearby electronics. VFDs generate electromagnetic interference (EMI) like tiny electrical storms that can interfere with other devices. Shielded cables act like shields, deflecting this EMI and keeping electronics safe.
But is a shield always needed? Not necessarily. If the user is not following European EMC regulations (89/336/EEC), unshielded cables can be used. However, a safe distance must be kept between motor cables and other wires in the setup.
A shield is only as good as its grounding. It is best to connect both ends of the shield to a good ground for maximum protection. It is also important not to forget to keep motor cables away from control and network cables—physical separation helps too.
Harmonic Havoc: Why It Matters for Cables
An electrical system is like an orchestra. Each device plays its part at a specific frequency, creating a harmonious tune. But then, power-hungry electronics like VFDs come in, throwing in extra notes (harmonics). These unwanted notes
disrupt the harmony, causing problems for cables, equipment and even the user’s wallet.
What are harmonics? They are higher-pitched versions of the main frequency,
like a screeching guitar solo in a gentle melody. They distort the perfect sine wave, leading to:
Hot cables: Harmonics act like extra passengers on a train, overloading cables and making them run hotter.
Confused equipment: Some devices misinterpret harmonics, leading to malfunctions and errors, like a
musician trying to play along with a wrong key.
Torque troubles: Motors can experience pulsations and vibrations due to harmonics, affecting their performance and life span.
So, what can be done? The answer lies in cable selection. Just like choosing the right size shirt, picking the right cable size is crucial. Here is how regulations help:
IEC 60364-5-52: This standard says if the “bad notes” (third harmonic and multiples) are too loud (over 33%), a bigger “cable singer” (a larger conductor) is needed.
Reduction factors: The cable’s capacity is like a song’s volume. If harmonics are present, this capacity needs to be “turned down” by a certain factor by choosing the right size cable.
For example: A user has a 39 amp (A) load and a 6 mm² cable (a small singer). It can handle 41 A normally, but with 20% “bad notes,” its capacity shrinks to 35 A (reduction factor of 0.86). A bigger “singer,” like a 10 mm² cable, is needed to handle the extra load without overheating.
To summarize the case of motor cable with a VFD:
Cable length is key. VFDs use a PWM signal that can cause issues with long cables. A mismatch between the cable and motor is like a tangled phone cord. It can lead to high voltage and fried motor insulation. The solution? Filters.
• Short cables (up to 100 feet): Use dV/dt filters to shield the motor.
• Long cables (over 100 feet): Sinus wave filters create a smooth signal, protecting the motor and preventing voltage spikes.
Shielded cables act as bodyguards, deflecting electromagnetic interference (EMI) from the VFD. It is important to ground both ends of the shield and keep motor cables away from control and network cables for extra protection.
VFDs can generate harmonics, extra electrical notes that interfere with the system. These can overheat cables and equipment. Follow IEC 60364-5-52 to choose the right cable size based on harmonic levels.
In short, VFD motor cables need special care. Choosing the right length, filter, shield and size based on the setup will keep the motor happy and the system humming smoothly.
The Benefits of Sine Wave Output
Next-gen VFDs offer a pure sine wave output, minimizing harmonic distortion and extending equipment life. Here are some of the benefits of this equipment:
Filter-free: These VFDs run clean, eliminating the need for additional components like filters, which saves money and simplifies maintenance.
Standard cables: Instead of costly
VFD-rated cables, the clean sine wave allows for the use of standard motor cables, reducing upfront costs and simplifying wiring.
(Almost) unlimited cable length: Unlike traditional VFDs, next-gen VFDs don’t suffer from energy buildup in the cables. As such, the only limitation is voltage drop, not special cable lengths.
Low harmonics: Ultra-low harmonics on both input and output eliminate the need for larger cables, reducing electrical noise and boosting energy efficiency. Additionally, the active front end ensures near-unity power factor, further enhancing efficiency and reducing costs.
The next generation of VFDs can go beyond controlling speed and torque. They minimize distortion, extend motor life and simplify installation.