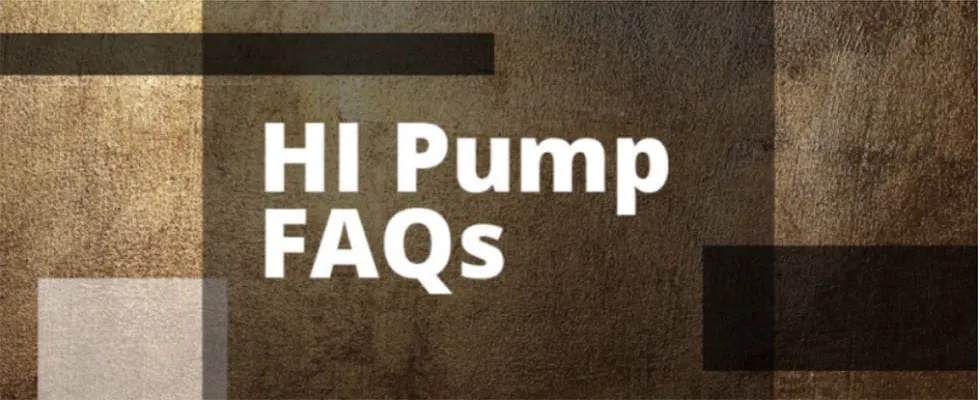
Power is monitored in pump systems to provide information about the operating point and equipment condition. Image 1 demonstrates the total head and pump input power curve as a function of flow rate, and from these measurements, pump efficiency can be calculated. This illustrates how measuring power for condition monitoring provides information regarding the operating point, and if measured in a consistent periodic way, it can provide an understanding of whether the pump efficiency is degrading.
Power can be calculated from mechanical measurements of torque and rotational speed or electrical input power. A variety of instruments are available to measure mechanical and electrical power in a pump system. These include:
Torque meters: These can be installed between the driver and pump and are simple to use and read, with some being able to automatically calculate mechanical power based on the measured torque and rotational speed. This requires installation between the driver and pump shaft, which is typically only possible in a laboratory environment and is often the method used by the manufacturer to determine the pump input power versus flow rate curve as shown in Image 1.
Strain gauges: These can be installed on the driver or pump shaft to measure torque, which in combination with a speed measurement enables the calculation of power. Calculating torque from the strain readings can be complicated by the shaft material properties, shaft misalignments and other errors.
Electrical power meters: These are useful if a system is driven by an electric motor. Electrical transducers measure voltage, current and phase angle, which in turn are used to calculate the supplied power to the motor. The calculated power and its changes over time can then be used to determine if parts in the pump are wearing out or if changes are occurring within the motor itself. This measurement in combination with the motor efficiency can be used to determine the pump input power.
Electrical current meters: These are useful in measuring amperage to determine if the motor is exceeding its full load amperage or a set value. Additionally, this amperage can be used with line voltage and power factor to estimate the electrical input power. Determining the electrical input power with this method inherently has greater uncertainty.
It is important to monitor power in a pump system to understand how it is changing over time, the operating point, the condition of the equipment and if there is opportunity for improvement. This enables intelligent adjustment of the pump operation and scheduling maintenance.
For additional information on methods of power monitoring, its benefits and condition monitoring considerations, refer to ANSI/HI 9.6.5 Rotodynamic Pumps Guidelines for Condition Monitoring at pumps.org.