Metering Pump Application and Selection
A wide range of metering pumps has been developed to fit the diverse applications in process engineering. Before selecting a metering pump, consider the following:
1. Chemical
Which chemical is to be metered and which properties does it have?
a. Viscosity
The higher the viscosity, the lower the stroke frequency, requiring a largerpipe cross-section .With viscosities higher than 400 mPas, we recommend using spring-loaded suction and discharge valves.
b. Abrasiveness
Suspensions (e.g., diatomaceous earth) or metering chemicals that tend to crystallize (phosphate solution) may lead to early leakage at the packing in the case of piston pumps. Aramid-Kevlar reinforced packings or diaphragm heads should be used.
c. Aggressiveness
The materials of the parts coming into contact with the chemical should be determined from experience and common resistance lists. The corresponding pump materials should then be selected.
2. Metering Capacity
The pump must be designed so maximum required capacity will already be reached if the pump setting is from 80 to 90 percent and has sufficient reserve capability. The performance of diaphragm metering pumps below 20 percent is not satisfactory.
3. Back Pressure
The back pressure directly at the pump is an important value. If the discharge line from the pump to the injection point is long (e.g., more than 40 ft), pressure pulsations can reach considerable values and interfere with the pressure at the injection point. Non-observance may cause damage to the system or affect the metering performance. In this case, pulsation dampeners should be used.
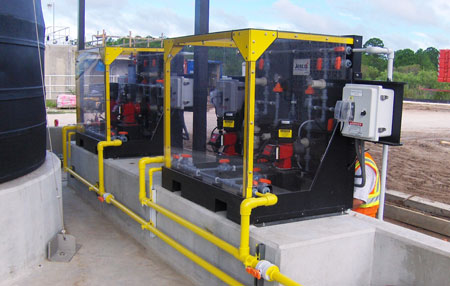
4. Suction Pressure
The suction pressure should not exceed 10 psi during pump operation. With diaphragm pumps, the suction pressure has to be kept as constant as possible (± 2 psi) because an unsteady suction pressure affects the metering capacity. A level oscillating around 12 ft would be extremely unfavorable especially with a density of 1,900 kg/m3. Suction pressure fluctuations up to 12 psi would cause metering errors of more than 10 percent, in extreme cases even up to 25 percent.
5. Pressure Dependence
Diaphragm metering pumps are relatively dependent on the back pressure. A constant artificial back pressure can be provided by setting the back pressure valve to a value approximately 15 psi higher than that of the injection point.
6. Nominal Diameter of the Line
When sizing the line for systems without pulsation dampeners, the nominal metering capacity has to be considered for calculating the nominal diameter at a flow rate applicable to 1m/s on the pressure side and 0.5m/s on the suction side.
7. Metering Pump Controls
Check if the metering pump works with a manually set value or if it is controlled using a remote signal. What will vary the stroke frequency or stroke length? If the input frequency is to be changed, the metering output follows proportionally in the case of diaphragm metering pumps. Will this remote signal be 4-20mA, pulse or simply a remote start/stop?
Answering these questions upfront will yield a correctly sized and applied pump.
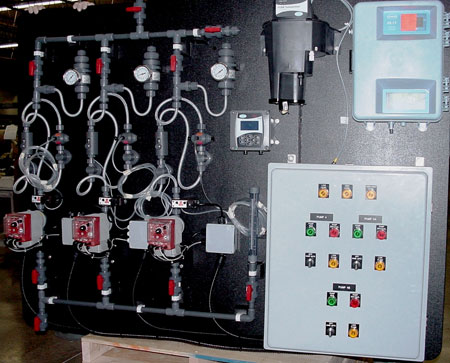
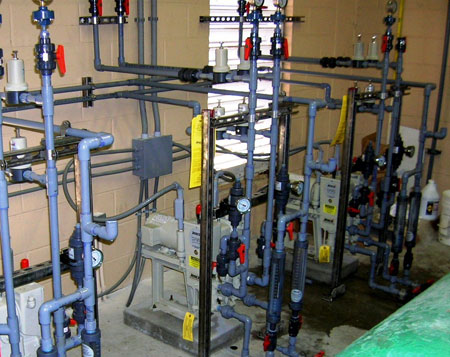
Diaphragm Life of Mechanically Actuated Metering Pumps
Often asked but impossible to answer is how long metering pump diaphragms will last. We will explain why answering is practically impossible.
Diaphragm Specifics
The operational life required from the diaphragm supplier is specified with greater than 5x107 cycles at maximum stroke, against 150 psi, and using water of 20 deg C (68 deg F). The diaphragms mainly consist of fabric-reinforced EPDM that is chemically resistant and mechanically resistant to repeated bending stresses. For assembly, threaded rod and support plate with a large surface is vulcanized into the diaphragm. The liquid-end side is coated with a 0.25 mm thick PTFE layer to be resistant to most media. It also makes the surface "slick" and suitable for food applications.
Abrasive Media
Nevertheless, some media can penetrate the PTFE layer (the PTFE layer is semi-permeable for certain molecular sizes). For example, if chlorine dioxide diffuses, the PTFE might come off of the EPDM. Metering is then reduced or stopped completely because the gas bubble produced between the EPDM surface and the PTFE layer acts like dead space. For these cases diaphragms without PTFE layer can be used. They are made entirely of EPDM or Viton.
When the metered medium increases in temperature, the operating life is shortened. The maximum normal operating temperature is 80 deg C (176 deg F). The operating life might then be reduced by 30 percent. For CIP applications or general sterilization, 120 deg C (248 deg F) are allowed for a maximum of 10 minutes if the pump is not in operation (provided that the head is resistant).
When metering abrasive media, e.g. suspensions such as hydrated or slaked lime, flush cleaning of the head must be provided, which is switched on for a few minutes after the pump has been shut down and before start-up. This ensures that hard sediments formed during standstill do not block the diaphragm in the lower section of the metering head and cause the diaphragm to rupture or the elastomer to tear off of the insertion part.
The maximum normal pressure load of the diaphragm must be known. The pressure losses of the fittings and the flow conditions must be added to the system pressure into which it is metered, including:
- Opening pressure of the injection nozzle
- Friction load of the piping
- Friction load of the installed fittings
- Acceleration pressure if no pulsation dampener is used on the discharge side of the pump
Back pressure valves should not be set to unnecessarily high values. For metering into open atmospheric
systems, a 15 to 25 psi setting is sufficient to avoid siphoning. If the back pressure valve is used to increase the accuracy by avoiding the influence of variable back pressure, the valve must be set to approximately 15 psi above the highest possible system pressure.
Optimized Life
The maximum operational life of a diaphragm in a pump will be reached, provided that the end user and supplier carefully consider the system's features. Suction conditions, maximum system pressure, temperature, chemical compatibility and proper installation are the variables to verify for a "best case scenario."
Given the above, the operational life may range from a few months to several years.
Pumps & Systems, March 2010