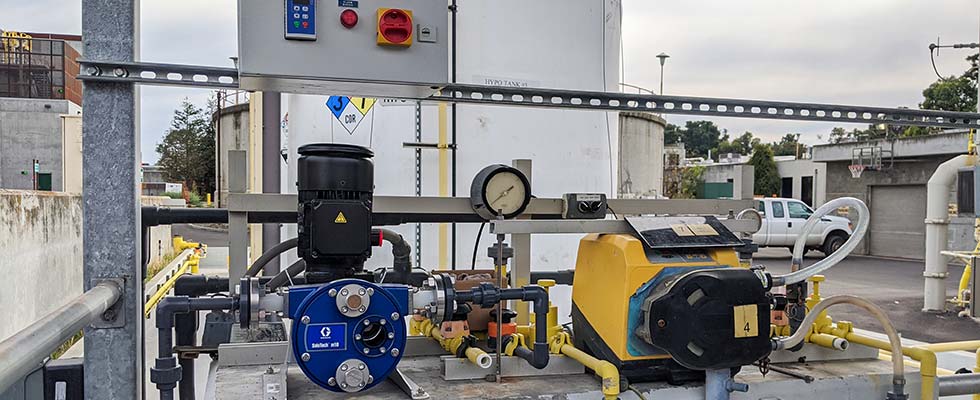
Water treatment infrastructure plays a pivotal role in the operation of today’s modern industry and society as it provides the means to manage the products, waste byproducts and the water itself as a resource. The processes vary from region to region and are governed by various agencies and oversight standards, but the ultimate aim remains universally linked to responsibly accounting for the water in situ, sequestering waste and effectively recycling the water being used.
It is often best to divide water treatment into categories based on what the water is being used for and the processes and materials/additives used to treat the fluids. For this article, water treatment will be separated into two main fields: municipal and industry/plant-level water treatment.
Industry/plant-level water treatment is the mandated and regulated practice used in industry to collect a facility’s waste fluids and treat them internally before sending them on or into the general water system.
Municipal water treatment is related most generally with the populace stream, grey water and environmental runoff (rain, erosion, etc.). This is often the end destination of industry’s water post-internal treatment.
With those defined, it is important to note that the style/system of treatment and scale of intervention is often dictated by the size of the facility and hazards/risks inherent to the processes in the facility. Some facilities have a primary means of waste management that handle fluids on-site, such as using evaporator systems and disposing of the solid waste completely free of the water stream. However, for large parts of the industry, waste liquids and fluids find their way to drains, collection tanks and treatment rooms.
For larger installations and facilities, there may even be the need for on-site water treatment facilities not unlike those found at the municipal levels, where waste fluid comes in and is fed back to the municipal lines completely treated. For smaller facilities, this may be scaled down to simply chemically treating or pH balancing the material before passing it on for processing at the municipal level.
The municipal category is largely focused on the complete treatment of wastewater by use of a variety of different chemical, mechanical and physical means. This process can consist of the combination of several steps and at varying levels, depending on the requirements of the locality:
Simple system:
Coagulation > Sedimentation > Filtration > Disinfection > Storage
Expanded system:
Collection » Screening and Straining » Chemical Addition » Coagulation and Flocculation » Sedimentation and Clarification » Filtration » Disinfection » Storage » Distribution
Chemical Metering, Dosing & Transfer of Fluids
As a fluid management process, wastewater treatment is heavily dependent on the transfer, metering and dosing of chemicals using various forms of pumping solutions. Throughout the process, a variety of technologies can be used to move, combine and separate fluids.
Fluid transfer is the dedicated equipment that is moving waste materials from their collection areas into the treatment process area and through the various stages in the process. Most often, large volumes of fluid are moved with positive displacement pumps, centrifugal or booster pumps for their sheer flow capacity. It is also common to see double diaphragm pumps being used where higher volume transfer is required, with less concern on concentration such as overflow or secondary processors.
Throughout the process of water treatment, a variety of chemicals is added in a controlled and measured way to maximize the effectiveness of the chemical reactions and minimize the waste of the chemicals in the process. This method of chemical dosing and metering is often performed by peristaltic pumps and/or double diaphragm technology.
For small applications or lower volume materials, peristaltic tube pumps are used because of their size and accuracy. For mid-to-large volumes of metered materials, peristaltic hose pumps are often used because of their durability and similar metering accuracies per size increase. It is important to remember that any pump technology used in these high-care functions has to be able to meet standards like the American Petroleum Institute (API) 675: steady-state accuracy (+/- 1%), linearity (+/-3%) and repeatability (+/-3%).
Most often, wastewater in-plant or in-line in the municipal system needs to be pH treated to neutralize inherent reactivity and render it more sterile to pathogens. This is often done on the plant level with chemical slurries such as sodium hydroxide (lime slurry) in the chemical processing areas. The process often consists of diaphragm pumps being used to transfer concentrated lime slurry to the dosing area/tank where a peristaltic provides the measured dose per volume or batch of wastewater. A two-pump solution makes use of both technology’s benefits.
Coagulation & Flocculation
Once the wastewater is balanced, it needs to be separated to effectively remove the waste component and recycle the carrier water. Coagulation and flocculation are the combined processes where a charged material is added to the waste stream, neutralizing the charge of dirt, debris and other dissolved particles causing them to bind to form larger particles. Commonly alum (aluminum sulfate), ferric sulfate or activated silica/carbon polymers are used, depending on the nature of the water being treated. Movement of the coagulated/flocculated materials is often more challenging because of the solid/semi-solids formed by the process and the requirement to keep them separated (and semi-intact).
The type of separations at play in this process is displayed by some materials bonding and collecting on the surface while others form sediment on the bottom. Different pump styles may be used for each, siphoning from the top with a diaphragm pump versus using a submersible waste pump for the bottom layers, etc. Commonly, the collection and transfer of this floc or sediment out of this stage are done with a gentler style of pump like a diaphragm or peristaltic hose pump to reduce the amount of reconstitution or mixing that occurs.
Water Disinfection
Water that has been balanced, separated and filtered to this point still requires a chemical additive to sanitize and disinfect it. Peristaltic-style pumps and double diaphragm pumps may be used in these steps to bulk-transfer the chemical into batches or dose the ingredient directly into the line. Most often, the disinfectant being used is a form of chlorine or chloramine, both of which prove difficult for traditional metallic pumps to handle—whereas the double diaphragm and peristaltic pumps can be configured with resistant fluid contacting materials.
Chemical Additives
A final step in the municipal process is the addition of chemicals for consumption or use downstream. The most common of these additives are fluoride or sodium chloride, depending on locality and water use. The addition of mineral solutions is often done prior to water storage and in line with the process, dosed accordingly for the volume or metered to the bulk storage location. Yet again, large systems generally use peristaltic hose or diaphragm pumps for adding these solutions, while smaller operations may rely on peristaltic tube pump systems.
Collectively, water treatment, especially wastewater, requires a wide array of pumps to facilitate the transformation of the water into a usable source and waste products. Because of the nature of the chemicals being used, and the volumes and the solids being removed, no single pump technology fills the bill as a total solution. By understanding the differences between the pumps being used and selecting the right style of pump, users can help eliminate waste and operations inefficiencies within the system and better manage the wastewater being treated.