If lubricants are a part of your services, you could be leaving money on the table, or more specifically, in the container. Manufacturers and operators use a wide range of specialized, high-tech lubricants that improve performance and extend the service life of equipment in extreme temperatures, harsh environments, heavy-duty service and other adverse operating conditions. These lubricants are available in a number of formulations for manufacturing, mining, construction and vehicle service applications. Specialized lubricants cost hundreds of dollars or more for a single container. Due to airborne dust, grit or other contaminants in facilities, excess lubricant that escapes from its original container and is exposed becomes contaminated and cannot be collected and recycled for use in a new container. To reduce costs associated with wasted product, it is critical that lubricant application systems use all of the lubricant in each container and avoid operating practices that result in waste during the application process. That is where piston pumps can help.
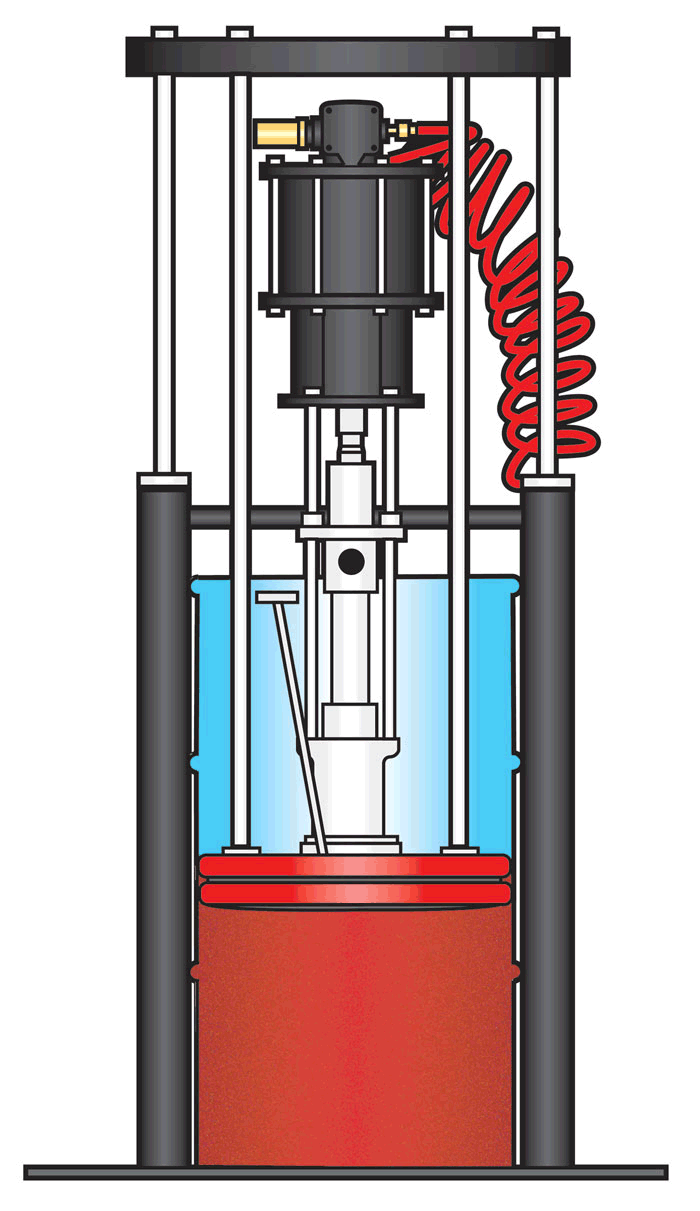