Using supplemental specifications and upgrading during pump repair provides reliability.
09/20/2015
Purchasing the least expensive pump is rarely the wisest choice for users wishing to achieve long run times and low or moderate maintenance outlays. Although a new company may be able to design and manufacture a better pump, newcomers do not always suddenly produce a superior product. Many users choose from the most respected existing manufacturers. The first step in purchasing should involve selecting and inviting only those bidders who pass certain tests. The following criteria must be met to determine acceptable vendors for situations demanding high reliability:
- Acceptable vendors must have experience with the specified size, pressure, temperature, flow and service conditions.
- Vendors must have proven capability in manufacturing with the chosen metallurgy, surface conversion treatment and fabrication method, such as sand casting or weld overlay.
- Vendors' "shop loading" must be able to accommodate the order within the required timeframe.
- Vendors must have implemented satisfactory quality control and must be able to demonstrate a solid on-time delivery history over the past several (usually two) years.
Use Supplemental Specifications
Reliability in a process pump is critical. Without an adequate specification, many pump suppliers default their offers and supplies to least expensive initial cost and relatively uncertain delivery times. Neither of these default situations will be in the user's best interest. So, the next steps users should follow when purchasing are:- Specify for low maintenance. Selective upgrading of certain components will result in rapid payback. Components that are upgrade candidates have been described in the references at the end of this article. Be sure you specify upgraded components whenever these are available. For example, review failure statistics for principal failure causes. If bearings are prone to fail, realize that the failure cause may be incorrect lube application or lube contamination. Address these failure causes in your specification and insist on the best available components, such as the seemingly insignificant bearing protector seals (see Figure 1).
- Evaluate vendor response. Allow exceptions to the specification if the exceptions are well-explained and valid. The potential reliability impact of waivers should be quantified.
- Clearly document pump design. The plant will certainly need pump cross-section views and other documents for future repair and troubleshooting work. Do not allow the vendor to claim these documents are proprietary and that you, the purchaser, are not entitled to see them. Place the vendor under contractual obligation to supply all agreed-upon documents in a predetermined time frame. Include in the agreement that you will withhold 10 or 15 percent of the total purchase price until all contractual data transmittal requirements have been met.
- On critical orders, contractually arrange for access to a factory contact. Alternatively, insist on the nomination of a management sponsor. The salesperson cannot fill this role. A management sponsor is a vice president or director of manufacturing (or a person holding a similar job function) working at the manufacturer's factory or head offices. Communicate with this person for help on issues that could impair pump quality or could seriously delay delivery.
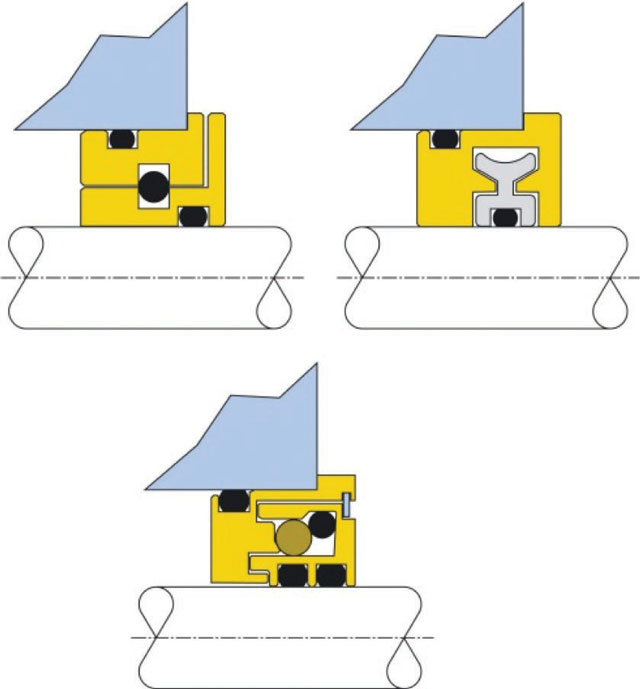
Upgrade During Repair
As pump manufacturers go through cycles of consolidation and employee attrition, they often lose valuable employees to early retirement or to pump rebuilders. The rebuilder's focus is competence and customer satisfaction, although valuing the customer's needs should be a priority for both OEMs and non-OEM pump upgrade providers. Users should look for competent pump repair shops (CPRS). A CPRS will understand the unquestionable merits of having oil rings manufactured with stress-relief annealing as an appropriate intermediate procedural step. A CPRS knows and can readily explain component upgrades worth an incremental cost over inexpensive, risk-prone or traditional products. One particular CPRS headquartered in the U.S. has branches in the Middle East and other regions. This CPRS uses 3-D mapping of existing pump parts and can catalog these for future use (see Image 1). The facility and its worldwide associates can rapidly produce 3-D casting patterns and molds for needed parts.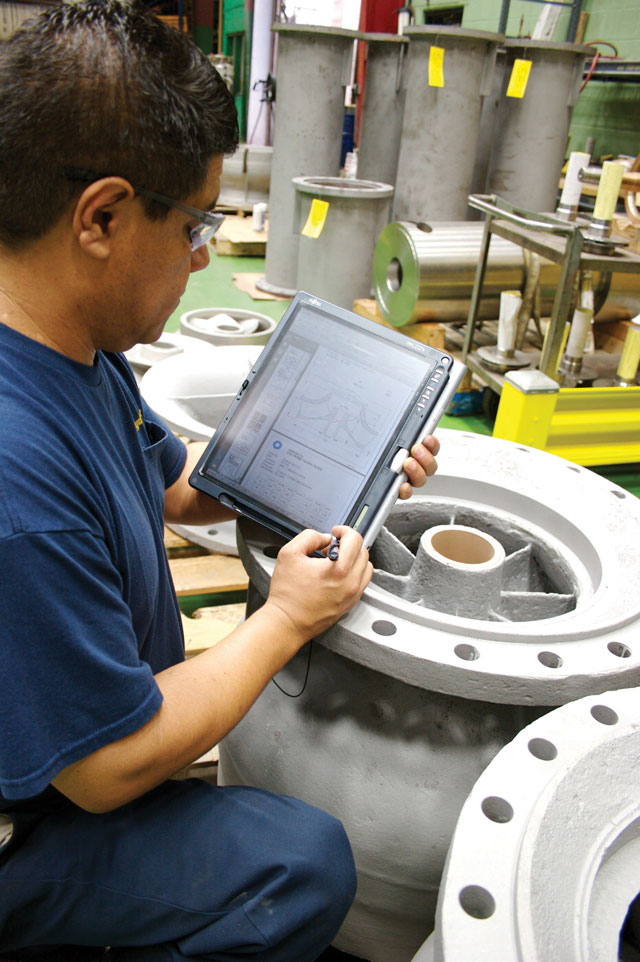
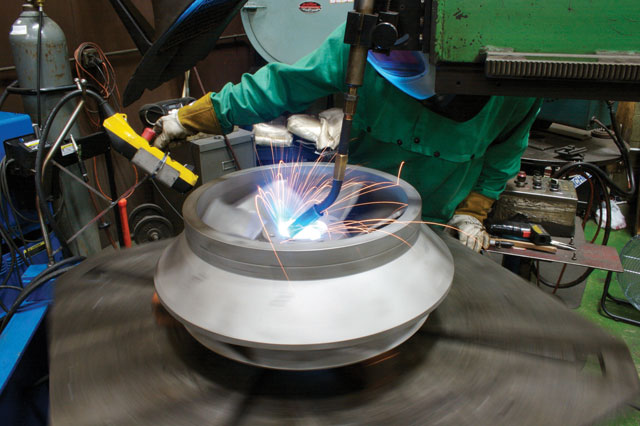
- Understand that equipment vendors base judgments on operation of machinery under near-perfect conditions, and field conditions are far from ideal.
- Accept the fact that cost-effective upgrades are possible and that your plant must become familiar with these.
- Implement the basics that appear in this article.
- Insist on root-cause failure identification.
- Refuse to tolerate repeat failures.
- Is an upgrade possible, and what is the benefit-to-cost ratio of such upgrading?
- Which CPRS should be pre-qualified and pre-selected as the pump spare parts and upgrading provider?
- Bradshaw, Simon; Bradshaw et al., Proceedings of the 17th TAMU International Pump User's Symposium, (2000)
- Bloch, H.P., "Pump Wisdom: Problem Solving for Operators and Specialists," (2011) John Wiley & Sons, Hoboken, NJ
- Bloch, Heinz P., (1998) "Machinery Reliability Improvement," 3rd Edition, Gulf Publishing Company, Houston, TX
- Bloch, Heinz P., and Allan Budris; (2013) "Pump User's Handbook: Life Extension," 4th Edition, Fairmont Publishing Company, Lilburn, GA
- Bloch, Heinz P.; Updating your Sealing Knowledge," Hydrocarbon Processing, March 2008