Q. What are some ways to monitor the power used by a rotary pump? A. Instrumentation and systems can be used, such as: Torque meter—The most direct way to monitor power is a torque meter with integral speed pickup between the driver and pump. This system directly senses the pump speed and torque required. Some torque meter readouts calculate the actual power transmitted. Under controlled operating conditions, torque measurement can sometimes detect internal component rubbing and wear in rotary pumps. Power meter—This device is useful if the pump is driven by an electrical motor, either directly coupled to the pump or through a gearbox, belt or hydraulic coupling. Electrical transducers are typically installed in the electrical motor starter to measure voltage, current and phase angle. The product of these values results in the power supplied to the motor. This approach monitors the power increase or decrease pump parts deteriorate or drag. It also indicates the general health of the electrical motor and/or the gearbox, belts or hydraulic coupling. This device may not be suitable for use with variable frequency drives, which alter voltage and current characteristics. Electrical current monitor—Similar to a power meter, it only monitors the motor current. The line voltage and power factor are assumed to remain constant, calculating the power supplied to the motor. While this method monitors the pump and motor condition, it is susceptible to error caused by variations in the electrical supply grid and motors with a low load. Strain gauges—Strain gauges installed on the pump shaft near the coupling or the drive output shaft with proper telemetry or slip ring equipment will indicate the torque required to drive the pump. This approach is similar to using a torque shaft except that a longer baseplate is not required to accommodate the length of the torque shaft. However, some accuracy is sacrificed. If the pump speed is constant or known, the power required by the pump can be calculated. With positive displacement pumps, a power monitoring device must not be used for overpressure protection. The pump must be protected by a pressure relief valve.
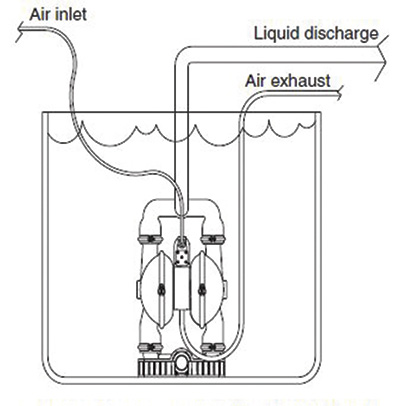