Remote terminal units help an Oregon utility monitor 40 major pump and lift stations.
04/29/2015
Clean Water Services (CWS), a water reuse provider in Oregon that serves more than 500,000 residents, has partnered with local organizations to educate the public about the importance of wastewater reuse.
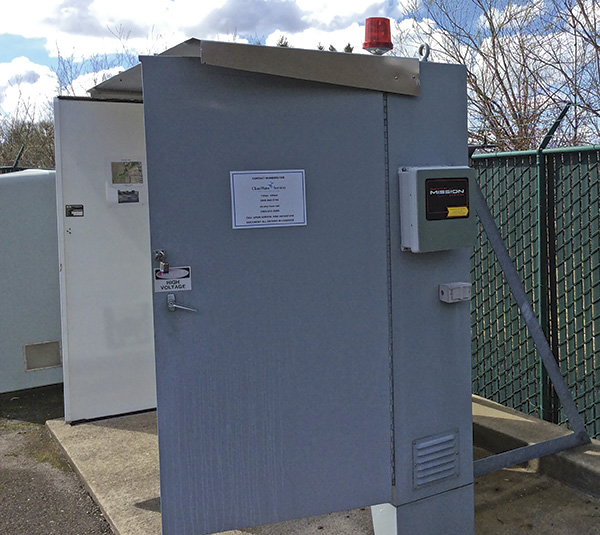