Understand these concepts before starting squirrel cage induction motors.
designmotors
06/19/2019
Questions about starting electric motors are common. Motor starting problems resulting from these questions can be costly and confusing, leading to production delays and sometimes catastrophic motor failure. This article will briefly explore some of the most common questions about the direct online (DOL) starting of squirrel cage induction motors. Through proper application, end users can have confidence that their motors and related equipment will not incur damage during the starting cycle.
Reading Speed-Torque-Current Curves
Speed-torque-current curves are plots of a motor’s torque and speed characteristics from zero speed up to no load speed (practically synchronous speed for an induction motor). All terms are commonly plotted as either percentage of full load or in their actual units (e.g. revolutions per minute [rpm], foot-pounds of torque and amperes). It is conventional for torque and current to both be plotted on the same graph, as well as being presented separately as shown in Image 1. Typically, plots of reduced voltage torque and current, as well as the load’s speed-torque characteristics, are also given. For the latter, it is key to obtain the load’s speed-torque curve and not simply the “running curves” for pumps and fans. Finally, these graphs can be plotted either horizontally (speed on the x-axis, torque and current on the y-axis) or vertically (speed on the y-axis, torque and current on the x-axis).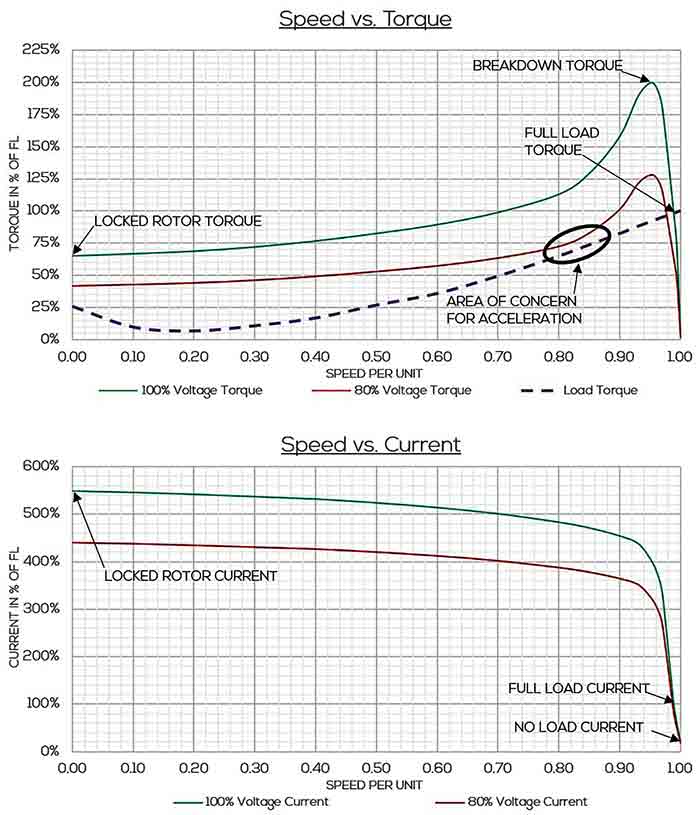
Reading Thermal Damage Curves
Thermal damage curves are plots that provide information about acceleration times, operational time limits at finite current levels and time limits on operation above full load. These curves are also known as “thermal limit curves,” “safe operating time curves” or “acceleration curves.” They are typically plotted with motor current as the x-axis and time in seconds as the y-axis on a logarithmic scale. As seen in Image 2, the plots found closest to the current scale show motor current during acceleration. These plots, typically at various voltage levels, intersect the speed scale at a point that represents LRC and intersect the time scale at the full-load current point to show anticipated acceleration time.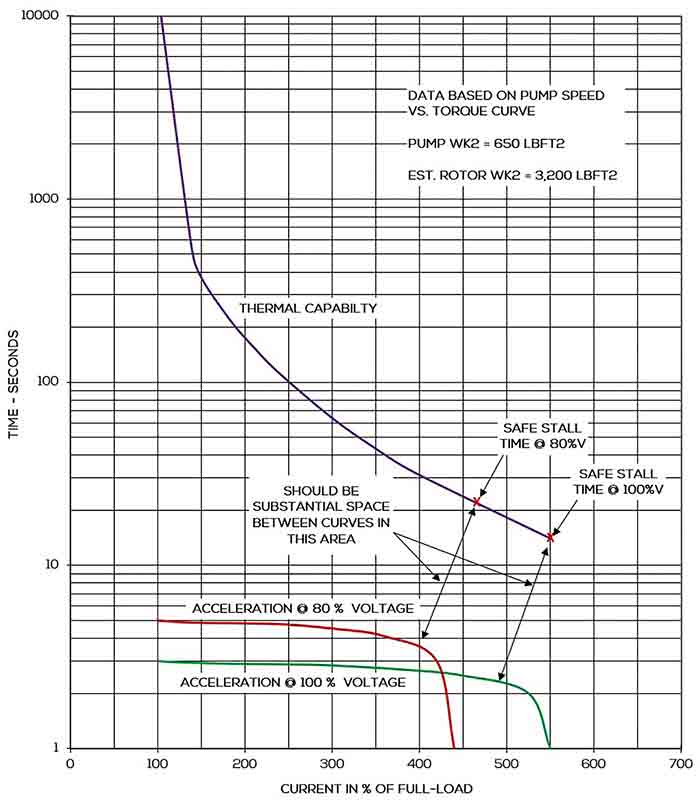
Locked Rotor Performance
Locked rotor performance encompasses the motor characteristics related to when a motor is in a locked (stalled) condition, such as at initial energization. Locked rotor performance is affected by combinations of the motor design, driven-load characteristics and onsite conditions. Typically, end users will specify locked rotor performance requirements and provide information on the driven load in addition to installation details such as typical voltage dip levels or if the motor will be started via a method besides DOL. Typically, the motor design for locked rotor is centered around providing the required torque while minimizing LRC and potential ill effects on full-load operation. Most standard commercial induction motors are rated as National Electrical Manufacturers Association (NEMA) Design B, which provides a reasonable balance between LRT and LRC for most loads. For larger motors or specialty applications, however, finer performance requirements might be in place, which require a motor design with features like a custom rotor bar shape or specialized rotor alloy. Aside from starting the motor via a device such as an auto-transformer, special contactor arrangement, or variable frequency drive (VFD), the greatest effect that on-site conditions have on locked rotor performance is the customer’s voltage dip level. LRC decreases in basically direct proportion with voltage, while LRT decreases as approximately voltage squared and can quickly cause starting issues for processes that start under load. Careful coordination between the end user and motor supplier is required to ensure that a proper motor design is selected for both onsite conditions and the load’s profile to provide reliable, safe locked rotor performance.Determining Acceleration Time
Closely related to locked rotor performance is the acceleration time a motor takes to start its load. Many of the same cause and effect relationships between motor design, onsite conditions, and load characteristics hold true for effects on both locked rotor performance and acceleration time. In the case of acceleration time, however, the entire speed-torque characteristics of the motor and load must be considered with net accelerating torque and total inertia being the most vital characteristics.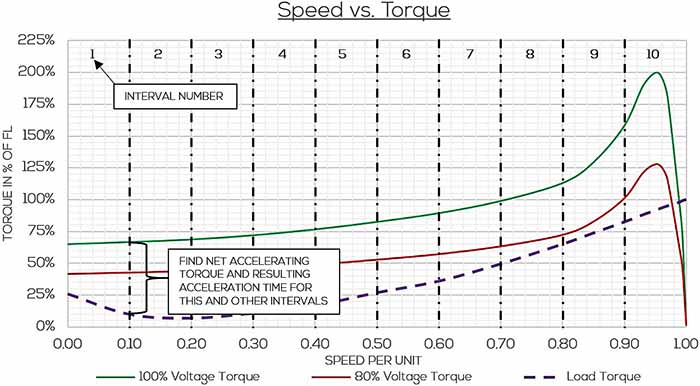
Other Related Areas
There are numerous questions surrounding motor starting that can be explored outside of this analysis, but some other points for consideration are:- a motor’s rated KVA Code Letter (assigns a “code letter” defined by NEMA MG-1 that gives an idea of the motor’s locked rotor current level when compared to its rated hp)
- how to interpret a large motor’s acceleration nameplate information (for example, understanding what the number of hot and cold starts means and how to interpret the time required between them)
- the theory behind safe locked rotor times and how these values are derived (principally these are based on the amount of time anticipated for critical motor components like rotor bars, end rings and stator windings to reach damaging temperatures)